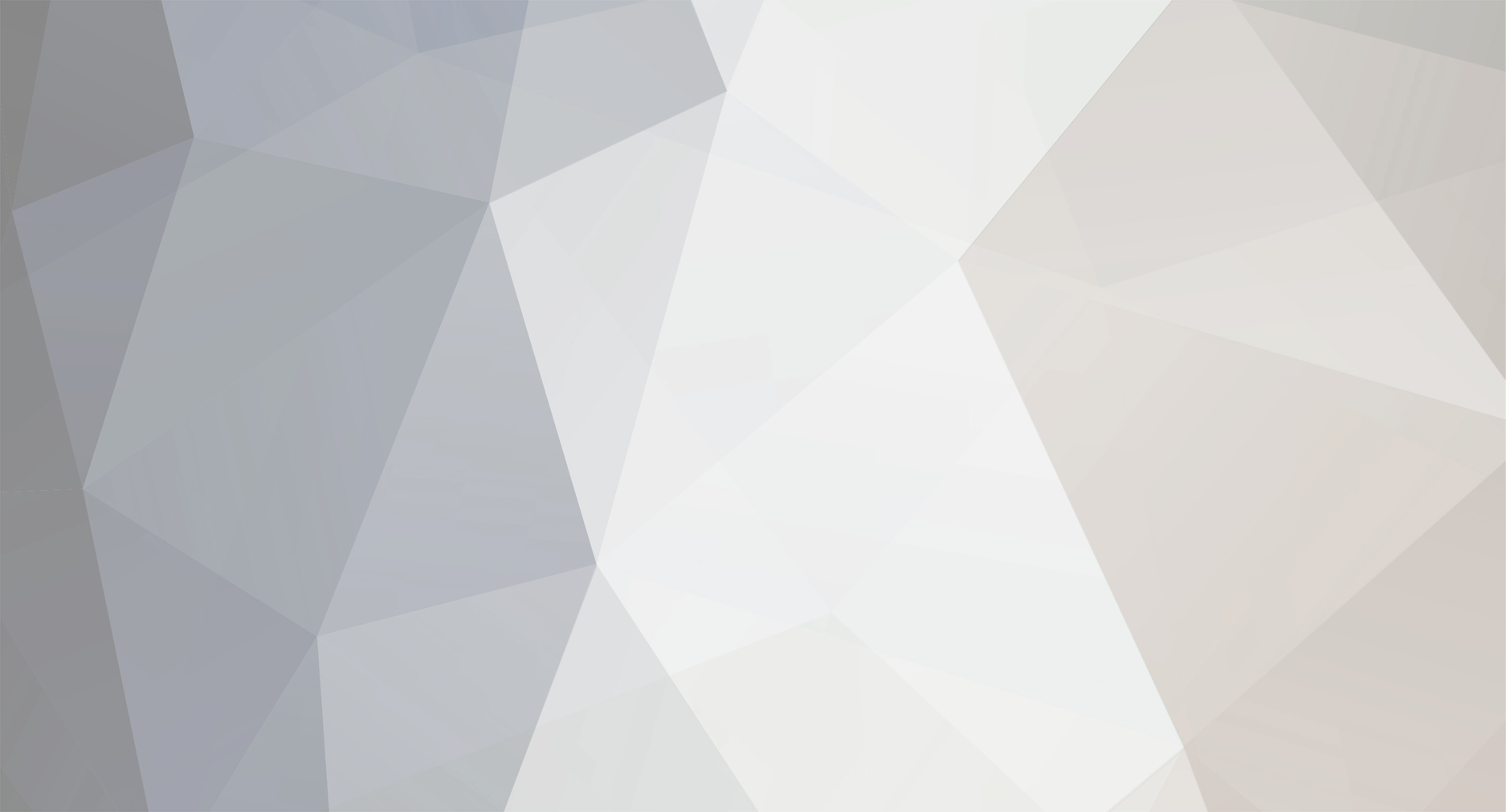
epfunke
Members-
Posts
33 -
Joined
-
Last visited
Everything posted by epfunke
-
just looked at the aube unit. that has the 24volt transformer built in. so you can use that themostat you quoted, and hook that between the iolinc and the aube. Aube low voltage side (screw terminals) W to IOlinc Common, IOlink NO to thermostat W, Thermostat R to aube R. thermostat and heat active when the IOlinc is on Then connect the heater to the 240 side of the aube as labled on the device
-
It is my understanding that your heater is a 240 electric heater. so you will need a line voltage thermostat like https://www.homedepot.com/p/Cadet-Double-Pole-22-Amp-120-Volt-240-Volt-Wall-Mount-Mechanical-Non-programmable-Thermostat-in-White-T522-W/303733757 does the heater have a built in thermostat? what is the model of your heater
-
If you connect the output of the contactor (controlled by iolinc)to the input of the thermostat (can be old school mechanical) and the output of the thermostat to the heater.... In order for the Heater to receive power, 1. The contactor controlled by iolinc must be on. AND the room has to be below your set temperature. This configuration will only apply power when you want it, and the room is actually cold enough to need heat
-
If you go the route of the iolink control, I would at least have an old school thermostat in line with the heater, set to your desired temperature. save energy by not overheating the room, and if something failed and the iolink did not turn off at least the themostat would limit the room temperature to a nominal temp and not a runaway temperature.
-
Thanks, I downloaded and also tested that link. Both worked and i can access ISY without the broadband connection
-
Yes I am using launcher, I will request the console for my firmware. Thanks for clarifying this
-
Today we were having outages with our ISP, Cable modem was off line. While we were offline I attempted to log into the admin console on ISY but was unable to. I would click on the start.jnlp file and the ISY finder would launch, I finds my ISY correct IP address displayed, but when i clicked on the admin console, I got nothing. I am on 5.0.16C. and could ping my isy while it was unresponsive. As soon as the ISP connection was back, I was able to access the admin console. and everything was back to normal. Any ideas of where to look so I can fix this so I can get to the admin console when I do not have access to public internet. Any and all help is greatly appreciated. If this has already been covered can you point me to the thread and i will start with any possible solutions there Thanks
-
You can use just about any insteon switch to turn on an appropriately sized contactor to turn on your heat. Just choose a contactor that has a 120v coil I have just that setup on my shop dust collector. Mounted the micro module right in large junction box with contactor. works like a charm
-
I have not re-labeled one in a while. I think i used 1/2" tape? any size can work if it is too wide you can always trim with scissors. as far as placing it I use a pair of fine tweezers to line it up and then just press on it to secure.
-
I have had great luck using clear p-touch labels. their software allows you to import graphics too.
-
Glad you got it working, but would recommend a slightly different connection. I would connect the positive power terminal of the relay to an always on power source on your board, and the input connection, to the #1 led circuit. As you have it wired the led pin is supplying all the current for the relay, on not knowing the rating on that pin, it may fail eventually? the input terminal on the relay board will put essentially no load on that led pin.
-
now that I zoom in it looks like you traced that out and R63 is the resistor for that LED. Just solder to R14 on the side closest to the chip and you should be all set
-
you can also use one of these small relay boards to buffer the sensors output and provide the contact closure for the iolinc https://www.amazon.com/HiLetgo-Channel-optocoupler-Support-Trigger/dp/B00LW15A4W/ref=sr_1_6?dchild=1&keywords=low+voltage+relay&qid=1602009072&sr=8-6 from what I can see from the picture, the one side of the LED appears to be grounded. and the other side jumps to the other side of the PCB, can you look at the other side of the board and follow that trace? you may find the series resistor on the other side of the board, maybe send another pic of the other side? and indicate where that led is on the other side so one can follow the trace. I would recommend soldering at the resistor it is more forgiving of heat than that tiny surface mount led
-
Thanks. Let me know what you find when you open it. if you use just a relay, dont forget a reverse diode across the coil. I have seen little modules that have a little driver transistor, etc on a pcb with screw terminal Have a good trip
-
you would not connect inline with the led, but across the led and current limiting resistor. The led will have a series resistor to limit the current so if you can find the led and its associated resistor, try testing from the other side of this resistor to ground with a voltmeter and see what you get when the led is on vs off. if you find something like 5 or 9 or 12?? volts when on and 0 when off. then there a number of easy to use relay modules on amazon that will give you the contact closure
-
Good morning the link for the voltage detection arduino in the previous post will not work, it is simply a voltage divider. the link that @gzaharposted look like it should work well.... Looks like it has adjustable input levels/ timeout, but may take some adjustment to make it work i looked at a picture of what may be you unit. is there an led that lights when motion is detected? not sure of your electronics knowledge, but maybe connect to that led and have a transistor drive a small relay, or the IOlink directly?
-
What is the make / model of the sensor?
-
Did you have any nearby lightning strikes around the time of the failure? Last summer I lost an iolinc to a nearby strike. was home at the time of the strike and later that day noticed our driveway vehicle sensor was not sending updates to isy. (magnetometer probe type) so has about 150 ft of cable back to the house, aka a nice big antenna to pick up a surge,