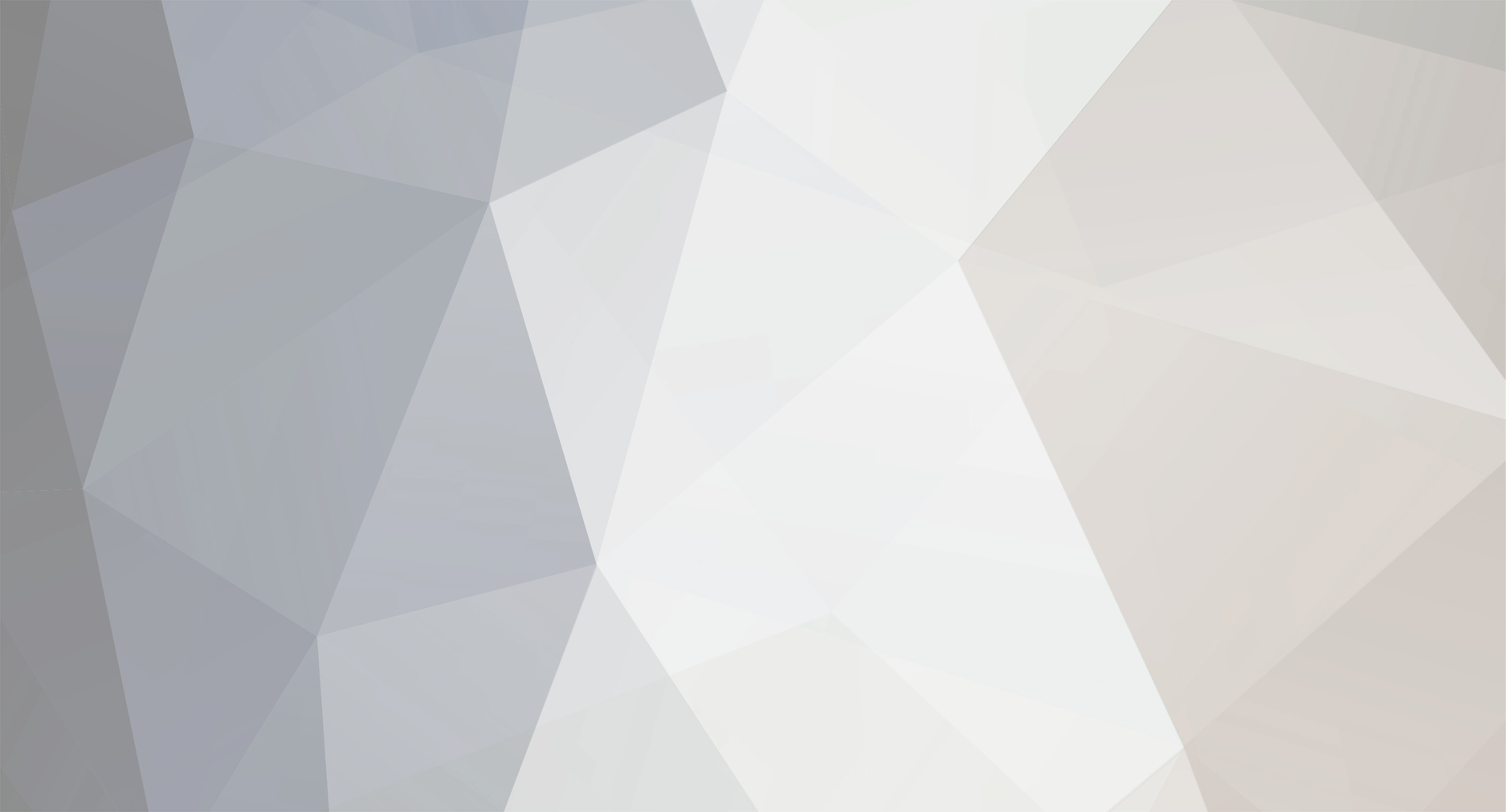
LeeG
Members-
Posts
12943 -
Joined
-
Last visited
Everything posted by LeeG
-
Program If From 9:00:00PM To Sunrise (next day) And Status 'KeypadLinc 8 Button-2 / KeypadLinc 8 Button-2 - B' is On Then Wait 15 seconds Set Scene 'Scene KPLButton B' Off Else - No Actions - (To add one, press 'Action') Scene ‘Scene KPLButton B’ contains Keypadlinc button B as a Responder
-
What is not present in the 4 Program implementation is Or ( Time is 4:30:00AM And Status 'Kitchen / Kitchen Motion - Sensor' is On ) The original single Program triggers True when the Kitchen Motion Sensor detects motion and enters a Wait. Because the Status of the Kitchen Motion Sensor has changed the If is reevaluated, now False and runs the Else. The Set Scene 'Entry Hall / Rear Entry Hall' On following the Wait does not run because of the reevaluation that happens when the Wait is executed and Kitchen Motion Sensor Status has changed.
-
I think wired Dual Band devices can have environmental conditions that reduce RF effectiveness compared to a pluggable Access Point for example. Look at the Hops Left=x count for the problem devices as well as some of the devices that appear to be working. See if there is a pattern relative to which phase the devices are on, how far from the PLM, related to a particular 120v circuit or circuits, etc.
-
arw01 The same thing that changes Status to On triggers an If Control xxxx is switched On statement. Assuming they are logically coded the same (both looking for On) they are both triggered by a Motion On message from the Motion Sensor when the Motion Sensor senses motion. If Control can be useful in an Occupancy sensing situation because If Control triggers on consecutive Motion On messages where If Status triggers only once for consecutive Motion On messages. Just depends on what the Program is trying to accomplish.
-
You have identified the problem with the Help | About information. The UI which is the Admin Console is still at 3.2.6 where the cat/subcat for the Dual Band 2487S did not exist. Thus the unsupported device message. Clear the Java cache and be sure the URL being used to invoke the Admin Console is for 3.3.10. Once Help | About shows 3.3.10 for the UI delete the device and add it back using the correct level of the Admin Console. It will be added as a supported device.
-
As far as the wet detection goes, it depends on what is in the water. The event trace was started when I initially read your last post. Once the Leak Sensor turned Wet On and stabilized no additional messages were generated until I remove the Leak Sensor from the water. About 10 minutes elapsed once the Leak Sensor stabilized Wet until I removed it from the water and it went Dry. Group 2 On is Wet, Group 1 On is Dry. As water sensors go this one is a significant improvement over others Smarthome has marketed. Some of the water sensors that connected to I/O Lincs would not trip even when the senor was submerged in water. This one works pretty well compared to others I have tested. I guess most anything would be better than what they had before. It will also depend on how much stuff is in the water. The subdivision is on a community well which has very good water as far as bad chemicals are concerned but it is well water. I run the water through a good charcoal whole house filter. My water may have more mineral content than a municipal water supply. Wed 01/30/2013 10:21:05 PM : [iNST-SRX ] 02 50 21.7A.CC 00.00.02 CB 11 02 LTONRR (02) Wed 01/30/2013 10:21:05 PM : [std-Group ] 21.7A.CC-->Group=2, Max Hops=3, Hops Left=2 Wed 01/30/2013 10:21:05 PM : [ 21 7A CC 2] DON 2 Wed 01/30/2013 10:21:05 PM : [iNST-SRX ] 02 50 21.7A.CC 00.00.02 CB 11 02 LTONRR (02) Wed 01/30/2013 10:21:05 PM : [std-Group ] 21.7A.CC-->Group=2, Max Hops=3, Hops Left=2 Wed 01/30/2013 10:21:05 PM : [iNST-DUP ] Previous message ignored. Wed 01/30/2013 10:21:06 PM : [iNST-SRX ] 02 50 21.7A.CC 00.00.02 CB 11 02 LTONRR (02) Wed 01/30/2013 10:21:06 PM : [std-Group ] 21.7A.CC-->Group=2, Max Hops=3, Hops Left=2 Wed 01/30/2013 10:21:06 PM : [ 21 7A CC 2] DON 2 Wed 01/30/2013 10:21:06 PM : [iNST-SRX ] 02 50 21.7A.CC 00.00.02 CB 11 02 LTONRR (02) Wed 01/30/2013 10:21:06 PM : [std-Group ] 21.7A.CC-->Group=2, Max Hops=3, Hops Left=2 Wed 01/30/2013 10:21:06 PM : [iNST-DUP ] Previous message ignored. Wed 01/30/2013 10:21:06 PM : [iNST-SRX ] 02 50 21.7A.CC 00.00.02 CB 11 02 LTONRR (02) Wed 01/30/2013 10:21:06 PM : [std-Group ] 21.7A.CC-->Group=2, Max Hops=3, Hops Left=2 Wed 01/30/2013 10:21:06 PM : [ 21 7A CC 2] DON 2 Wed 01/30/2013 10:21:06 PM : [iNST-SRX ] 02 50 21.7A.CC 00.00.02 CB 11 02 LTONRR (02) Wed 01/30/2013 10:21:06 PM : [std-Group ] 21.7A.CC-->Group=2, Max Hops=3, Hops Left=2 Wed 01/30/2013 10:21:06 PM : [iNST-DUP ] Previous message ignored. Wed 01/30/2013 10:21:08 PM : [iNST-SRX ] 02 50 21.7A.CC 00.00.02 CB 11 02 LTONRR (02) Wed 01/30/2013 10:21:08 PM : [std-Group ] 21.7A.CC-->Group=2, Max Hops=3, Hops Left=2 Wed 01/30/2013 10:21:08 PM : [ 21 7A CC 2] DON 2 Wed 01/30/2013 10:21:09 PM : [iNST-SRX ] 02 50 21.7A.CC 00.00.02 CB 11 02 LTONRR (02) Wed 01/30/2013 10:21:09 PM : [std-Group ] 21.7A.CC-->Group=2, Max Hops=3, Hops Left=2 Wed 01/30/2013 10:21:09 PM : [iNST-DUP ] Previous message ignored. Wed 01/30/2013 10:31:20 PM : [iNST-SRX ] 02 50 21.7A.CC 00.00.01 CB 11 01 LTONRR (01) Wed 01/30/2013 10:31:20 PM : [std-Group ] 21.7A.CC-->Group=1, Max Hops=3, Hops Left=2 Wed 01/30/2013 10:31:20 PM : [ 21 7A CC 1] DON 1 Wed 01/30/2013 10:31:20 PM : [ 21 7A CC 1] ST 255 Wed 01/30/2013 10:31:20 PM : [ 21 7A CC 2] ST 0 Wed 01/30/2013 10:31:22 PM : [iNST-SRX ] 02 50 21.7A.CC 00.00.01 CB 11 01 LTONRR (01) Wed 01/30/2013 10:31:22 PM : [std-Group ] 21.7A.CC-->Group=1, Max Hops=3, Hops Left=2 Wed 01/30/2013 10:31:22 PM : [iNST-DUP ] Previous message ignored. Wed 01/30/2013 10:31:22 PM : [iNST-SRX ] 02 50 21.7A.CC 11.00.01 CB 06 00 (00) Wed 01/30/2013 10:31:22 PM : [std-Group ] 21.7A.CC-->11.00.01, Max Hops=3, Hops Left=2 Wed 01/30/2013 10:31:23 PM : [iNST-SRX ] 02 50 21.7A.CC 11.00.01 CB 06 00 (00) Wed 01/30/2013 10:31:23 PM : [std-Group ] 21.7A.CC-->11.00.01, Max Hops=3, Hops Left=2 Wed 01/30/2013 10:31:23 PM : [iNST-DUP ] Previous message ignored.
-
Once the Leak Sensor has been tested in water (not a damp towel) the nodes will have this Status In water, Wet node On, Dry node Off Out of water, Wet node Off, Dry node On
-
Glad that was the problem. You mentioned there are multiple Leak Sensors. Only one RF only device can be added at a time. If more than one RF only device is put into linking mode at the same time they cancel each other out making writes to the device impossible.
-
The Leak Sensor Link Database was not created. Are there any Green Icons to the left of either the Dry or Wet nodes? If a Pro ISY are RF device updates turned off? Perhaps the Leak Sensor timed out of manual linking mode before the link records could be created. Put the Leak Sensor into link mode and right click the Dry node, select Restore Device to rebuild the Leak Sensor link database. Run another Show Device Links Table after the Restore Device to verify there are two E2 Controller link records in the device itself.
-
The initial Current State values for both nodes will be blank until some communication is received from the Leak Sensor. What does Help | About show for Firmware and UI levels? With the Leak Sensor in linking mode (Set button press until LED is blinking continuously), right click Dry node and select Diagnostics | Show Device Links Table. Post the results. Unless the forum has been fixed it will not accept an image file. Either the image has to be placed on a hosting site or Save the Show results and post the file. It will be an XML file which must be posted with all the XML tags. EDIT: I changed the above to use Dry node for Show Device Links Table. The Wet node does not have the Diagnostic choice.
-
Need to test in water for actual wet/dry test. A damp towel does not provide enough conductivity between the two metal feet. Not much water needed, about 1/8 inch in a plate. Not deep enough to get inside the device. Just enough to make a water bridge between the two metal feet. However, if Set button tap is not registered by a change in both the Dry and Wet nodes it sounds like it is out of RF range.
-
Did the Program not trigger or it triggered but evaluated False? May have to start with a more basic If. Once confirmed the If Control Kitchen MS will trigger True add additional checks, confirming correct operation of each addition until the condition that prevents the trigger or False evaluation is determined. With the Garage and Kitchen Motion On ORed together it is not obvious why it does not work with the information posted.
-
It is the only way of knowing for sure there are two Dual Band devices in RF range of each other and they are on opposite phases (both conditions needed for phase coupling). Since any Dual Band device in RF range will react it also shows how many RF devices can hear any specific Dual Band device.
-
Thanks. The 4 tap Set button process is for testing RF range and same/opposite phase power. The RF aspect of a Dual Band Insteon device is functional from the time power is applied. It is not dependent on the 4 tap test to be operational. When the Set button on a Dual Band device is tapped 4 times the device transmits a test RF message. Other Dual Band devices that are in range of the RF signal will blink the status LED and indicate whether on the same or opposite electrical phase by color/intensity of status LED. Access Points will blink Red when on the same phase, blink Green when on the opposite phase which indicates these two devices are capable of coupling the phases. The 4 tap Set button test is not required for the RF to function. It does show how many devices are in range of each other and how many are on the opposite phase.
-
"I see there is an option to use the SwitchLinc Dimmer as a phase coupler... is this a good idea? Should I enable it?" Can you post a link or describe where this option is discussed. Normally the RF aspects of a Dual Band are automatic and not under control of the user.
-
Since variables have no knowledge of the device type driving the Program there is a comm problem with the devices tested. Run Tools | Diagnostics | Event Viewer at LEVEL 3 and run the test on some of the devices that are not consistent. I suspect the Hops Left=x count will vary or be at Hops Left=0 for many of the paddle interactions which indicate poor comm.
-
extrakt0r Scenes do not have Status so a Scene name cannot appear in an If statement. The name in the If must be a device name. A Set to a Scene name cannot set to a specific % On level so the Then statement has to be a device. For a Scene the % On Level is maintained in the Responder link record in each Responder device. Nothing in this Program sets it to 100% On. I suspect the Program was meant to use a Time range rather than two specific time values. As coded the Program only runs the Then at Sunrise+20 and at Sunset+20 rather than From Sunrise+20 To Sunset+20. Seems odd that Program would change the On level of a device only twice at specific times rather than a range of times. Checking for 'not Off' covers all the various % On possibilities, including On (100%). Checking for ‘is On’ only tests for a Dimmer being full On (100%)
-
If Control only looks at commands coming from the device being tested. A command must flow from the device and it must match the specified command to trigger the Program. If the device sends two On commands for example because its paddle/button/sensor is turned On twice (tapping On paddle twice - not Fast On) the Program is triggered twice. If Status looks at the ISY Current State column information. Anytime the Current State information changes the Program is triggered. The example above where the device is turned On twice by tapping paddle twice triggers the Program only once. Status has to change to trigger the Program. The second On paddle press does not trigger the Program because it was already On from the first On paddle press. When other Controllers can change the state of the tested device such that the Current State column information changes the Program is triggered. Thus If Status can cause a Program to trigger either when the device itself is turned On/Off with its paddle/button/sensor or is turned On/Off by another Controller. In this specific case the Leak Sensor nodes are Controller Only nodes, they have no Responder capability. They cannot be turned On/Off by another Controller so only changes the Leak Sensor initiates causes Current State column (Status) to change. Which a Program uses, If Control or If Status, depends on what you want to trigger the Program. The Leak Sensor is somewhat unique because it does not normally generate two On commands in a row and it is not a Responder so If Control and If Status come close to working the same. However, all the rules apply from an ISY perspective. If Control is looking at commands flowing from the device, If Status is checking the information in the Current State column of the device. EDIT: in the last posted example the line for 'is not switched Off' serves no purpose.
-
The Repeat goes BEFORE the statement(s) to repeat. If Status 'Main: Basement Water-Wet' is On Then Repeat Every 1 minute Send Notification to 'Entire House Email' content 'Main Basement: Water Sensor wet' Else - No Actions - (To add one, press 'Action')
-
Glad the Factory Reset cleared it up. This was a difficult one because the device was reacting inconsistent with other SwitchLinc Dimmers at lower firmware levels. Once MikeD reported his v.41 was working as the other SwitchLinc firmware it was either a defective device or something got scrambled requiring a factory reset to clear. Thank you MikeD!
-
Unless you are paying an additional fee for it you do not have a static public IP address. Some ISPs change the public IP address frequently, others keep the same public IP for longer periods of time. My ISP wants $5 a month for a static public IP.
-
A Factory Reset will not change that. It is called Resume Dim. Look at the SwitchLinc User Guide under Local On Level. It covers that reaction under Resume Dim.
-
I think that is a question for the MobiLinc category. Not sure he monitors other topics.
-
In MobiLinc the Scene is turned On and MobiLinc shows the Scene as On but when the Scene is turned Off in MobiLinc the Scene still shows On?
-
This is the command that was traced for the Adjust Scene Local On Level adjustment Tue 01/29/2013 06:18:39 AM : [iNST-TX-I2CS] 02 62 20 AD 6D 1F 2E 00 01 06 7F 00 00 00 00 00 00 00 00 00 00 4C This is the command that was traced when using the On Level (applied locally) slider. Tue 01/29/2013 06:20:05 PM : [iNST-TX-I2CS] 02 62 20 AD 6D 1F 2E 00 01 06 72 00 00 00 00 00 00 00 00 00 00 59 They are the same (except for slightly different On %), yet MikeD sees results on his v.41 different from yours. I would Factory Reset the SwitchLinc followed by a Restore Device to get the link database back. Then try either the Admin Console test with the On Level (applied locally) slider or click the Program name and run the Then Clause. As before, the ISY will not write Local On Level values it thinks it already wrote so it will be necessary to change the value. The slider test is the easier of the two since all that is necessary to set it up is move the slider a little. Trying to keep relevant information together. This is what MikeD reported Started with the my SwitchLinc (2477D v.41) in the Off condition 1) Paddle press Fast On - the lights come on 100% 2) Paddle press Off - the lights go completely off 3) Paddle press On - the lights go to my "On Level [Applied Locally]" setting His step 3 result and your step 9 result do not track.