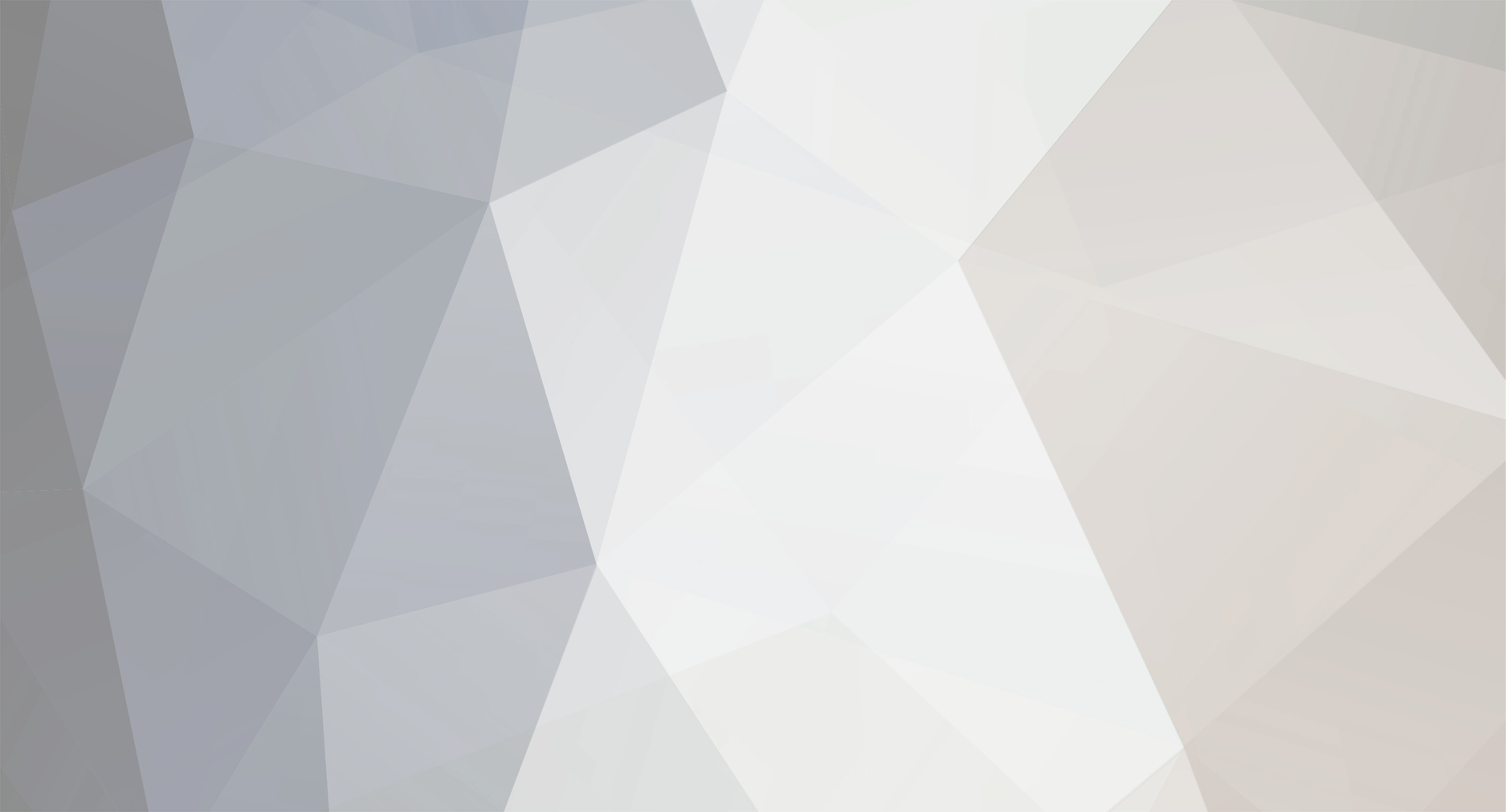
LeeG
Members-
Posts
12943 -
Joined
-
Last visited
Everything posted by LeeG
-
A deleted link record only changes the flag byte to inactive. The Insteon address will remain in the inactive link record.
-
The iMeter Sole is monitoring the power drawn by the PLM? Probably not a good idea. Can't say I have heard of anyone trying that combination. If you are having PLM comm problems that is the first thing to eliminate. A simple test would be to run Tools | Diagnostics | Event Viewer at LEVEL 3. Use the Admin Console to turn On/Off a variety of devices. Check the Hops Left=x counts. Plug the PLM directly into the wall outlet. Repeat the test and see if the Hops Left=x count improves or is more stable.
-
There is one file, Insteon_3.3.10.zip Did the Mac unzip it during the download There is a Java 11 update for windows as well
-
Without seeing the Program what you have planned is guess work. A Program with a Time range triggers once at the From time running the Then clause and once at the To time running the Else clause. A Query in the Then clause executes once. Could put a Repeat every 10 minutes for example and issue the Query every 10 minutes. Adding an If Status xxxxx is not Responding check to the If clause would terminate the Repeat when the device starts responding. Best to post the Program.
-
No means for tracing a single device. I'm looking for the heartbeat as well. Problem is I'm not sure the Insteon message will be traced since it is not from a supported Group number.
-
No. I think the process is to send the UUID of the 99i and the 994 to sales@ UDI and they will activate the modules on the new 994.
-
The heartbeat is not currently supported by the ISY. See the link below. Michel indicates heartbeat support is in plan but difficult to test because they have not seen a heartbeat. viewtopic.php?f=25&t=10572&hilit=heartbeat
-
If a Program is a necessary follow-up to keep two devices in sync (assuming both are controllers of the same ISY Scene) there is an Insteon Mesh Network issue to begin with. No reason to think the network issue would not affect the activity of the Program as well. Has there been activity to fix the Insteon network problem? Until that is resolved device communication involving these devices can be unreliable regardless of whether device or PLM initiated. A simple test is to run Tools | Diagnostics | Event Viewer with LEVEL 3. Use the Admin Console to turn the switch and the KPL load On and Off several times looking at the Hops Left=x count. If the counts move around or is Hops Left=0 it indicates a track-able issue that can be used to show when the problem has been corrected.
-
Like the ISY-26 was a few years ago, the 99i will be functionally stabilized because of memory constraints. That has not happened yet but posts from Michel indicate it will happen. The 994 can accept a ZigBee radio now and a Zwave radio in the future (one or the other, not both). There is a post that has the characteristics of the 994, CPU, speed, etc. I'll see if I can find it and post a link. I had no problem moving from 99i to 994. Installed a current backup from 99i onto 994. Used the same PLM. Link to Hardware Specs topic viewtopic.php?f=27&t=9952&hilit=994+cpu
-
Might show something if some of the entries are garbage but without something to compare it to it is just a link database display.
-
Using Enable Internet Access is the least preferred option versus port forwarding. With port forwarding confirmed working that is all you need. It is permanent across power outages. With Enable Internet Access external access to the ISY can be lost if the router reboots.
-
az1324 Thanks for the post. Your results were different than mine so I ran some tests using actual water for a Wet condition rather than a damp towel. With actual water I get your results. In water - Dry is Off, Wet is On Out of water - Dry is On, Wet is Off The change in node state (Dry to Wet, Wet to Dry) happens without tapping the Set button.
-
Post the XML, before and after if you have it. I can convert to text that can be posted.
-
"Is there supposed to be a low battery node for these?" Not according to the spec's on the sales page.
-
The ELK Zone does not stay violated for the 1 minute+ that is required for the Wait to complete and the light turn Off. As soon as the ELK Zone is no longer violated the If is reevaluated to False and the Else clause runs.
-
Does not matter whether a load is attached to the Red wire. The switch must be a Controller in a Scene for it to appear in the 'In Scene' parameter pulldown list.
-
The Motion Sensor and TriggerLinc (both RF devices) will blink quickly when one of the devices linked to them does not respond. Usually because it is out of RF range so the outbound command or inbound ACK is not received. Have not seen my Leak Sensor do that but it would be consistent with other RF only devices.
-
Check that the Insteon address is not already defined to the ISY.
-
Not that I have seen. The Quick Start guide covers the basic linking mode indication. The RF devices generally react this way. Press the Set button for 3-5 seconds puts it into linking mode with the LED blinking continuously. Press the Set button again puts the device into unlinking mode with the LED double blinking continuously. Press the Set button again takes it out of unlinking mode with the LED no longer blinking.
-
The combination of ISY firmware of 3.2.6 and Admin Console (UI) of 3.3.9 is not a supported combination. Why is the Admin Console so much later than the ISY firmware being used?
-
1. Is all of this normal (from what I read here, I think it is)? I think it is normal. Without having access to the SmartLabs specs the only thing we have to go by is how it reacts. They all are reacting the same way. 2. How should I manage one of these sensors in a program? It is easy enough to trigger an event on Dry = On (the sensor is wet), but how do I detect when the sensor becomes dry again given the behavior I observe above? I have not seen it go back to Dry=Off on its own. A tap of the Set button is what I have been using to bring it back to a Dry state. I think SmartLabs did this on purpose to insure an intermittent leak would not go unnoticed. They design for the non-HA world so if the device automatically reset when the water evaporates an intermittent leak or overflow condition could be missed.
-
I think it is the way the ISY chose to name the nodes for the two Groups/Scenes the Leak Sensor uses. When the Leak Sensor detects moisture it sends a Group 1 On which is the Dry node Group number. When the Set button is tapped a Group 2 On is sent which is the Wet node Group number. As the Leak Sensor Set button is tapped the Leak Sensor alternates between sending a Group 1 On and a Group 2 On which the ISY interprets as Group 1 On means Wet condition (Dry node On) and Group 2 On which the ISY interprets as Dry condition (Dry node Off). The Wet node cycles Off when the Dry node is On and the Wet node cycles On when the Dry node is Off. It would be great if SmartLabs allowed access to the devices specs but they don't. We are left with programming in response to how the device reacts without understanding what the device actually thinks about all of this.
-
Place the Leak Sensor on a dry surface and tap the Set button until the Leak Sensor - Dry node shows Off. Place the Leak Sensor on the wet napkin (I use a wet paper towel to test). The Dry node should turn On and the Wet node turn Off.
-
How many nodes were defined when the Leak Sensor was added? Do the nodes cycle between On and Off as the Set button on the Leak Sensor is pressed (tapped)?
-
This should work assuming "Hardware / Living Room" is the device that should have the Local On Level set. If From 1:00:00PM To 8:00:00AM (next day) Then In Scene 'Hardware / Living Room' Set 'Hardware / Living Room' 30% (On Level) Else In Scene 'Hardware / Living Room' Set 'Hardware / Living Room' 100% (On Level) The ISY does not write a Local On Level it thinks is already set so to see the results in the event viewer it is necessary to change the Program 30% level to something else like 35%. Run Tools | Diagnostics | Event Viewer with LEVEL 3. After changing On Level to 35% and Saving, right click Program and run Then. Post the event trace.