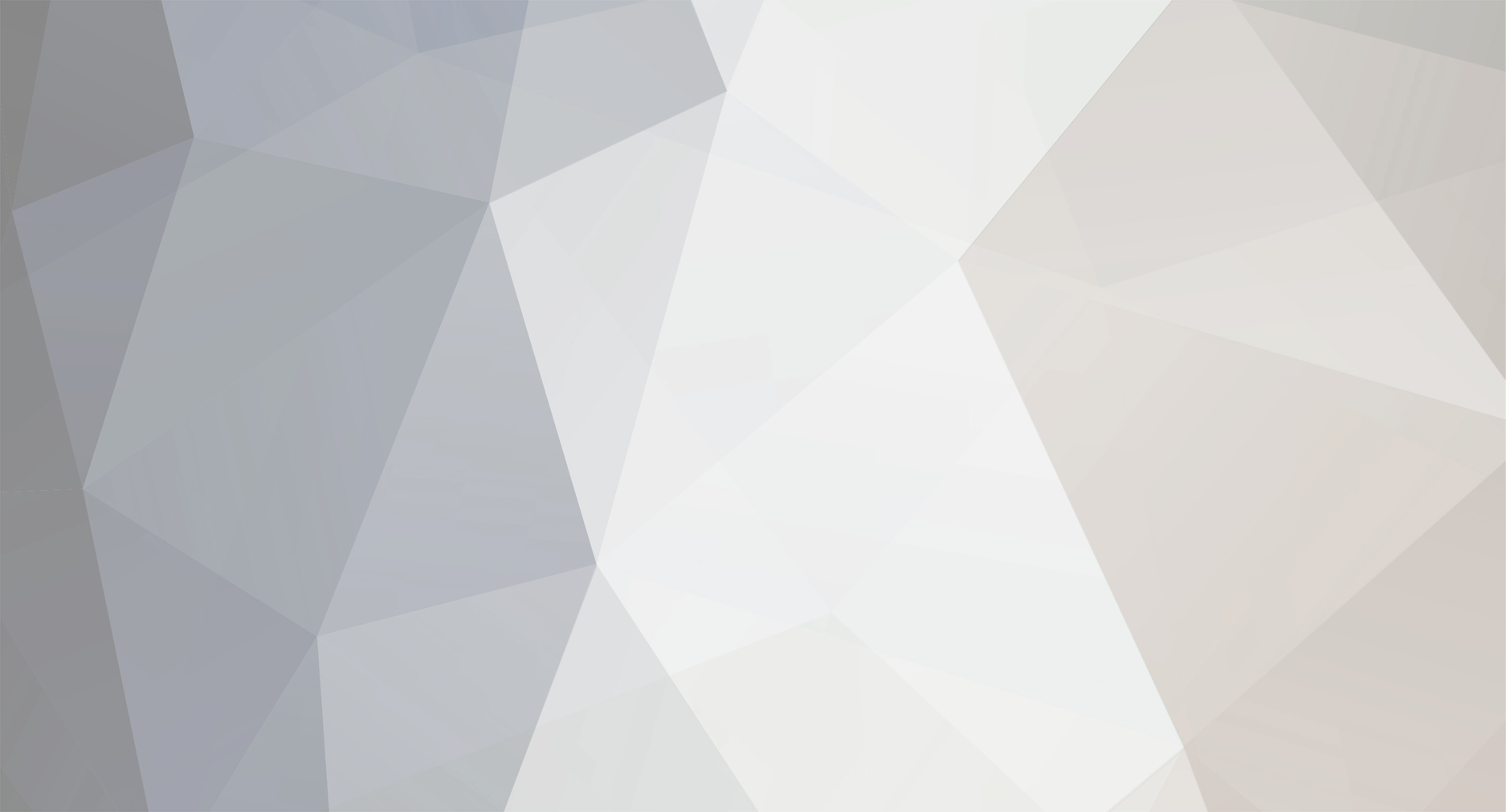
LeeG
Members-
Posts
12943 -
Joined
-
Last visited
Everything posted by LeeG
-
For #1, click on the KeypadLinc button name in Red below the ISY Scene name. Set the Ramp Rate as desired. In Insteon every Controller can have a unique set of On Level/Ramp Rate values for the Responders. For #2, each device times the length of the Start Dim/End Dim sequence. It is possible for the SwitchLinc to physically turn Off before the KeypadLinc has decided enough time has passed between the Start Dim/End Dim, leaving the KeypadLinc button LED On. Hold the SwitchLinc Off paddle longer. As an additional activity an ISY Program can be triggered when the SwitchLinc goes to Off and turn the KeypadLinc button LED Off. EDIT: ISY assumes a Controller is also a Responder.
-
Under the Configuration tab, Change Location button.
-
The suggested switch actually was shipped with the garage kit for years. Smarthome switched to the NC only switch a year or so ago. It works but many folks prefer the Sensor state be what you get when using a NO switch.
-
Just the new one. The currently installed magnetic switch is NC. The NO portion of the new switch would be used. It is wide gap switch so installation should be replacing the current NC with the new NO. No change to I/O Linc nor ISY.
-
This is a combination NO and NC magnetic switch that Smarthome carries. SECO-LARM Enforcer SM-226L-3 Magnetic Garage Door Contact Switch
-
There is a Trigger Reverse option that will reverse the Sensor results but that has issues with the 3AM Query every morning. Trigger Reverse does not reverse the Query results so the KPL button changes at 3AM. The best solution is to use a NO magnetic sensor. This produces the Sensor status you are looking for.
-
Either change the Scene to contain that one device and use Program to turn On/Off the other devices now in the Scene Or Use a Program to adjust the KPL button LED On/Off (assuming a Secondary button) based on the single device.
-
A Disabled Program is not affected by state change. Watch Programs | Summary page. Run the Program manually and follow the Activity column as state changes in Disabled Program. The Else clause does not run when state changed.
-
Yes, the Local On Level can be adjusted on a 6 button KPL just as it was on the 8 button. The 6 button KPL has 5 nodes as the ON/OFF buttons function as a single node, the ON button turns the load On, the OFF button turns the load Off. Instead of changing the Local On Level for button A (Main) set the Local On Level of ONOFF button. It is done with a Program that is time triggered just as with the 8 button KPL.
-
The Smoke Bridge sends state changes to the ISY automatically as other Insteon devices do. No need to query the Smoke Bridge.
-
An Insteon Scene executes as follows .... The application issues a Scene On/Off message The PLM sends a Group Broadcast message which all Responders should see and react to. This message is not ACKed as many devices may react to this message. The PLM sends a Group Cleanup Direct message to the first device in the Scene. The device should ACK this message. If no ACK is received the PLM sends another Group Cleanup Direct message to the same device. This is repeated up to three times. The PLM sends a Group Cleanup Direct message to the second device in the Scene. The same sequence described above is possible. Each device in the Scene is sent a Group Cleanup Direct message by the PLM. How long this process takes depends on the number of devices in the Scene and how many Group Cleanup Direct messages are required for each device., When all Group Cleanup Direct messages have been sent (including retries) the PLM sends a message back to the application indicating the success/failure of the Scene message originally sent by the application. Writing a Program that has to take all this variation into account is very difficult. The ISY has chosen not to expose the Program to this volatility. The ISY issues a Group Broadcast message directly rather than issuing the Scene message. There are some additional capabilities available when the Controller is an I2CS device. EDIT: the PLM cannot receive another application message while the Scene is being processed so either the Program execution is suspended until the Scene completes or additional responsibility is transferred to the Program. Activity such as emails, variable updates, anything that does not lead to PLM activity can still be done but that would require the Program track the progress of the Scene the PLM is working on. I have written applications that work in this environment. They are much more complex even when other activity is not desired.
-
That is the only format for a detail Insteon trace. They get easier to read over time. The comm looks good in this trace. No way to determine from the trace what was wrong before as everything worked as expected this time.
-
Thanks, good to hear it is working.
-
Run Tools | Diagnostics | Event Viewer at LEVEL 3 while adding ToggleLinc using Auto Discover. Post the event trace. That message normally indicates a comm problem with the device. Double check Insteon address to be sure an 8 or B and 5 or 6 have not been read incorrectly.
-
There is another Program that is sending an email. Also normally it is necessary to right click on Low Batt node and select Query to reset the node to Off.
-
The KeypadLinc has two modes of operation regarding the Local On Level. View the KeypadLinc User Guide and search for "Resume Bright". In this mode the KeypadLinc remembers the last On Level (as established by the Scene in this case) and returns to that On Level. The User Guide describes how to change the way the KeypadLinc responds.
-
OP is running a 994i, at 4.0.5.
-
Not using an ISY Scene as a Scene. I guess anything is possible but that seems unlikely. A major aspect of an Insteon Scene is that all responders normally react at the same time. If that was changed to use Direct commands it could take several seconds before the last responder reacted.
-
I had forgotten about load sense. The button on the side of a LampLinc is all but useless. One step forward with the addition of Dual Band and two steps back when load sense dropped.
-
"curious to learn why the ISY doesn't retry scene commands" The Group (Scene) message flow that would enable retry introduces large variations in how long a Scene may take to execute. The delays (waits) that would be required in Programs to insure the Scene was actually complete makes Program logic very difficult to implement. If the Insteon network is generally unreliable the Set Scene can be issued multiple times to achieve a higher degree of success.
-
The I/O Linc Relay responds to Direct commands using the Latch/Momentary mode that has been defined for the relay. The difference with a Direct command is On always turns the Relay On and Direct Off always turns the Relay Off (assuming the relay was On when the Direct Off is issued). The Relay will turn Off automatically if in any of the Momentary modes. With Scenes what happens with a Scene On or Scene Off depends on the Momentary mode. Each Momentary mode has a different set of rules as to what Scene On and Scene Off commands actually do. A Scene Off can actually turn the Relay On when in Momentary C mode based on the Sensor status. That is why I suggested using a Direct On as that always turns the Relay On.
-
Thanks for the Green LED info. The opener looks like a single button which normally works with I/O Linc. Does the manual button still work with the I/O Linc Relay connected in parallel? If the I/O Linc Relay is in Latching mode it would not operate the door and would stop the existing manual button from working.
-
LampLincs do function as a Controller, ApplianceLincs do not. How old is the LampLinc?
-
Sorry, I did not see "At 6:00 am on Wednesday the tstat read set point of 80." in the earlier information. Things to check 1 Time in ISY is accurate 2 Program | Summary display to see when the Program was last triggered and how (True or False) 3 Run Tools | Diagnostics | Event Viewer at LEVEL 3 during time Program should trigger
-
The Else leg of the Program ran to set the 80 value at 8 AM