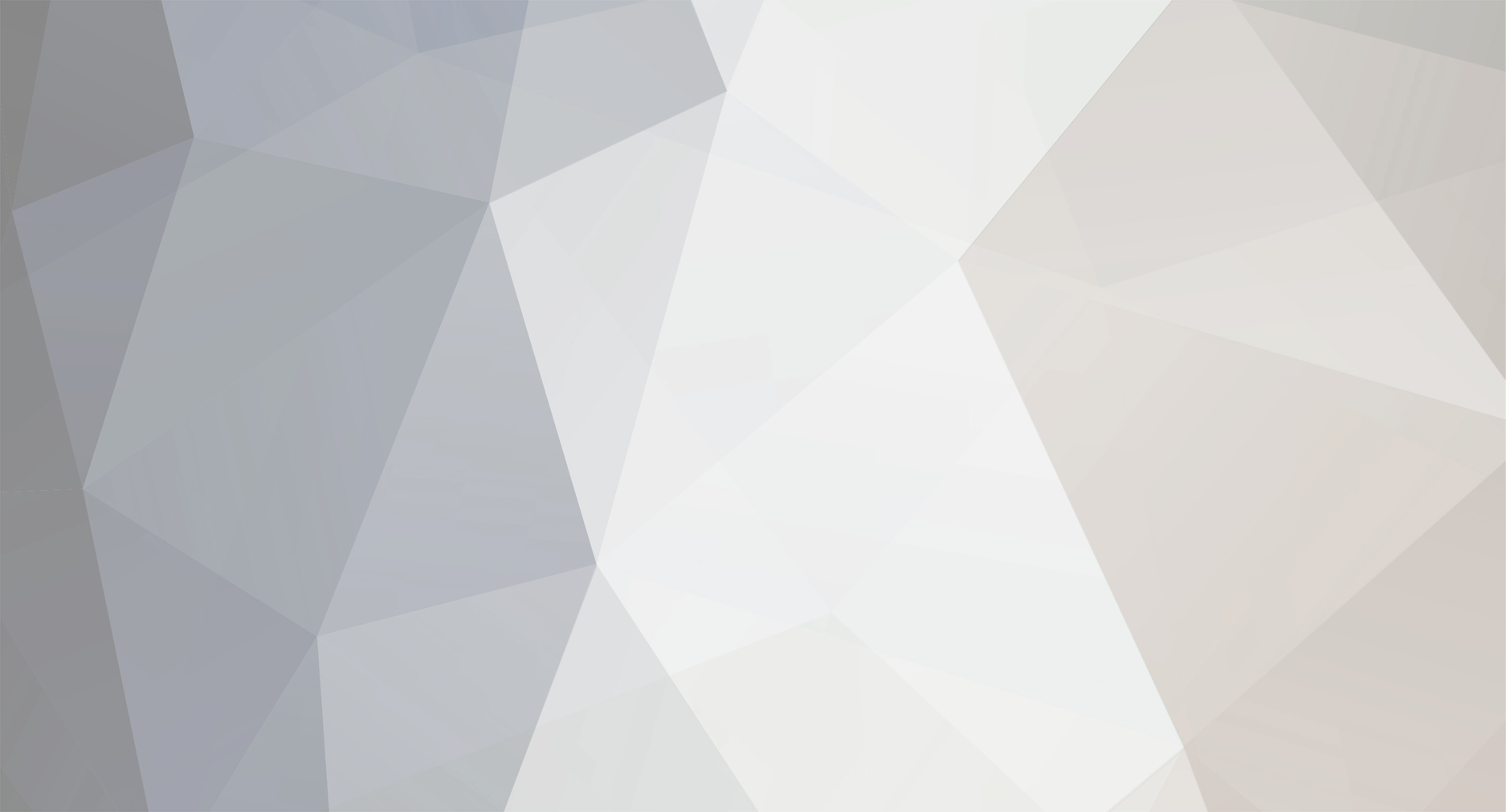
LeeG
Members-
Posts
12943 -
Joined
-
Last visited
Everything posted by LeeG
-
Since the Leak Sensor is sending a Wet On the Program should be working. Look for a False folder or some other situation that is interfering with Program function. Did not mention if Leak Sensor is located in leak detection location. If in a different location for testing comm could be a factor.
-
Comm is fine and the event trace is showing a Wet On. cccccccccccccccMon 02/08/2016 02:20:25 PM : [iNST-SRX ] 02 50 36.AE.14 00.00.02 C7 11 02 LTONRR (02)
-
What is the Hops Left=x number when Set button on Leak Sensor is pressed? Mon 02/08/2016 02:49:20 PM : [iNST-SRX ] 02 50 21.7A.CC 00.00.01 CB 11 01 LTONRR (01) Mon 02/08/2016 02:49:20 PM : [std-Group ] 21.7A.CC-->Group=1, Max Hops=3, Hops Left=2 Mon 02/08/2016 02:49:20 PM : [D2D EVENT ] Event [21 7A CC 1] [DON] [1] uom=0 prec=-1 Mon 02/08/2016 02:49:20 PM : [ 21 7A CC 1] DON 1 Is the Leak Sensor near the 2413S PLM or in its normal leak detection location? Unless comm is poor the issue is the combination of the Leak Sensor and the water. Run Tools | Diagnostics Event Viewer at LEVEL 3. Insure Leak Sensor is physically Dry, all water removed from Leak Sensor. While Dry tap Set button. Then place in water no deeper than 1/8 ". Post the event trace. Icon on bottom right side of event viewer copies to clipboard. Paste clipboard into post.
-
" What is strange is this behavior is only observed when executing the scene from the program. Execution of the scene via Smart Phone, Admin Console, etc all respond and report status information correctly." The same Insteon command is issued whether invoked from Admin Console or an ISY Program. That would indicate some other Insteon traffic when run from an ISY Program is causing interference. Suggest running Tools | Diagnostics | Event Viewer at LEVEL 3. Run the activity before and during ISY Program activity. Post the event trace.
-
QueryAll - [iD 0072][Parent 0001] If Time is 3:00:00AM Then Set Scene 'My Lighting' Query Else - No Actions - (To add one, press 'Action')
-
Try right click on EZFlora node and select Group Devices. You may have all,eight nodes but they are not listed together without being 'grouped' together.
-
bilsk Apologies for poor sample. Seven second Wait replaced the 1 second Wait rather than being added where it should have been. OpenDoor - [iD 002F][Parent 0001] If Control '2C.71.C2.1 - Door Sensor' is switched On Or Control '2C.71.C2.1 - Door Sensor' is not switched Off Then Wait 7 seconds Set 'ApplianceLinc' On Wait 1 second Set 'ApplianceLinc' Off Else Set 'ApplianceLinc' Off Thanks Larry for the heads up.
-
Looks like the magnet and magnetic switch are not correctly positioned. Thirteen seconds after door starts to move the Sensor turns On. However, the Sensor immediately turns Off. It looks like the magnet is 'sliding' to/past the magnetic switch rather than meeting side by side. I have a switch that operates when the door is fully closed and a separate switch that operates when door is fully open. I had to put fully open switch on a flexible metal strip because of slight variations in fully open position. Also the magnet and switch should not 'slide' past each other. That can cause the switch to read On then Off then On. When a single switch is used it should operate when door reaches fully closed rather than fully open. Sat 02/06/2016 08:44:33 : [iNST-SRX ] 02 50 3D.51.45 2A.1C.D7 2B 11 02 LTONRR (02) - door starts to move Sat 02/06/2016 08:44:33 : [std-Direct Ack] 3D.51.45-->ISY/PLM Group=0, Max Hops=3, Hops Left=2 Sat 02/06/2016 08:44:33 : [D2D EVENT ] Event [3D 51 45 2] [sT] [255] uom=0 prec=-1 Sat 02/06/2016 08:44:33 : [ 3D 51 45 2] ST 255 Sat 02/06/2016 08:44:46 : [iNST-SRX ] 02 50 3D.51.45 00.00.01 CB 11 00 LTONRR (00) - Sensor turns On Sat 02/06/2016 08:44:46 : [std-Group ] 3D.51.45-->Group=1, Max Hops=3, Hops Left=2 Sat 02/06/2016 08:44:46 : [D2D EVENT ] Event [3D 51 45 1] [DON] [0] uom=0 prec=-1 Sat 02/06/2016 08:44:46 : [ 3D 51 45 1] DON 0 Sat 02/06/2016 08:44:46 : [D2D EVENT ] Event [3D 51 45 1] [sT] [255] uom=0 prec=-1 Sat 02/06/2016 08:44:46 : [ 3D 51 45 1] ST 255 Sat 02/06/2016 08:44:46 : [D2D-CMP 0002] STS [3D 51 45 1] ST op=1 Event(val=255 uom=0 prec=-1) is Condition(val=255 uom=0 prec=-1) --> true Sat 02/06/2016 08:44:47 : [iNST-SRX ] 02 50 3D.51.45 2A.1C.D7 41 11 01 LTONRR (01) Sat 02/06/2016 08:44:47 : [std-Cleanup ] 3D.51.45-->ISY/PLM Group=1, Max Hops=1, Hops Left=0 Sat 02/06/2016 08:44:47 : [iNST-DUP ] Previous message ignored. Sat 02/06/2016 08:44:47 : [iNST-SRX ] 02 50 3D.51.45 11.01.01 CB 06 00 (00) Sat 02/06/2016 08:44:47 : [std-Group ] 3D.51.45-->11.01.01, Max Hops=3, Hops Left=2 Sat 02/06/2016 08:44:47 : [iNST-INFO ] Previous message ignored. Sat 02/06/2016 08:44:47 : [iNST-SRX ] 02 50 3D.51.45 00.00.01 CB 13 00 LTOFFRR(00) - Sensor turns Off Sat 02/06/2016 08:44:47 : [std-Group ] 3D.51.45-->Group=1, Max Hops=3, Hops Left=2 Sat 02/06/2016 08:44:47 : [D2D EVENT ] Event [3D 51 45 1] [DOF] [0] uom=0 prec=-1 Sat 02/06/2016 08:44:47 : [ 3D 51 45 1] DOF 0 Sat 02/06/2016 08:44:47 : [D2D EVENT ] Event [3D 51 45 1] [sT] [0] uom=0 prec=-1 Sat 02/06/2016 08:44:47 : [ 3D 51 45 1] ST 0 Sat 02/06/2016 08:44:47 : [D2D-CMP 0002] STS [3D 51 45 1] ST op=1 Event(val=0 uom=0 prec=-1) is Condition(val=255 uom=0 prec=-1) --> false Sat 02/06/2016 08:44:47 : [D2D EVENT ] Event [3D 51 45 2] [sT] [0] uom=0 prec=-1 Sat 02/06/2016 08:44:47 : [ 3D 51 45 2] ST 0 Sat 02/06/2016 08:44:47 : [iNST-SRX ] 02 50 3D.51.45 2A.1C.D7 41 13 01 LTOFFRR(01) Sat 02/06/2016 08:44:47 : [std-Cleanup ] 3D.51.45-->ISY/PLM Group=1, Max Hops=1, Hops Left=0 Sat 02/06/2016 08:44:47 : [iNST-DUP ] Previous message ignored. Sat 02/06/2016 08:44:47 : [iNST-SRX ] 02 50 3D.51.45 13.01.01 CB 06 00 (00) Sat 02/06/2016 08:44:47 : [std-Group ] 3D.51.45-->13.01.01, Max Hops=3, Hops Left=2 Sat 02/06/2016 08:44:47 : [iNST-INFO ] Previous message ignored. Could also be the "relay follows input" as Paul has already posted.
-
This may provide a single Program approach OpenDoor - [iD 002F][Parent 0001] If Control '2C.71.C2.1 - Door Sensor' is switched On Or Control '2C.71.C2.1 - Door Sensor' is not switched Off Then Set 'ApplianceLinc' On Wait 7 seconds Set 'ApplianceLinc' Off Else Set 'ApplianceLinc' Off
-
"I reinstalled the mini-8 picking the Delete all Links option but the ISY Links Table was NOT changed " Not sure what this activity was. Neither the ISY Links Table nor the Device Links Table was affected (image 18 shows device links and ISY links still exist)
-
That is correct. Would be good to understand the problem with the ISY Links Table as that should reflect the Scene activity established by the ISY. Can you provide additional data .... ISY Firmware, ISY UI, both from Help | About Type of ISY, 99i, 994i Were any Mini-Remote links done manually, outside of ISY Detail of problems with ISY Links Table
-
Factory Reset of Mini-Remote made the device useless to the ISY. Insteon requires the Mini-Remote to have the link records to be able to communicate with the PLM and whatever other devices the Mini-Remote is linked to. The next step,is to Restore Device to Mini-Remote. If you want to start from scratch remove the Mini-Remote from its Scene(s) and Delete device. Add the Mini-Remote to the ISY to reestablish the required links to the PLM. Then add Mini-Remote buttons to any desired Scenes.
-
I'm not suggesting the objective is not valid. However, do you folks understand how Insteon sets each Scene Responder device On Level to a unique and separate value? That there is no Insteon command that would accept x number of new override On Levels, one new value for each Scene Responder device? I have a Scene xxxx with 6 Responders. Responder device 1 has an On Level of 100% Responder device 2 has an On Level of 100% Responder device 3 has an On Level of 60% Responder device 4 has an On Level of 40% Responder device 5 has an On Level of 10% Responder device 6 has an On Level of Off How would you adjust each of the 6 devices as the On Level for each Responder is stored in the Responder device.
-
Insteon messages start with "02 6x" for messages outbound from ISY/PLM and "02 5x" for inbound messages. The ISY adds messages that interpret what the Insteon message contains. Tue 02/02/2016 10:21:51 AM : [iNST-SRX ] 02 50 3C.75.CD 00.00.01 CB 11 00 LTONRR (00) - 02 50 from device Tue 02/02/2016 10:21:51 AM : [std-Group ] 3C.75.CD-->Group=1, Max Hops=3, Hops Left=2 - generated by ISY - has Insteon address, Group (scene) of node, Hops counts, Max Hops permitted, Hops Left available The basic Event viewer data is covered in this Wiki section http://wiki.universal-devices.com/index.php?title=ISY-99i/ISY-26_INSTEON:Using_the_Event_Viewer The web site www.insteon.com has links to other Insteon documents that cover many other 02 5x, 02 6x, and 02 7x Insteon messages. The PLM User Guide has much detail, too much detail for 99% of users but some data is helpful. Scan the documents and pick the data that seems interesting. Of course any specific question(s) about actual messages in a trace can be posted. Several of the ISY and Insteon experts are happy to post answers.
-
"So this means that the dimmer never sends out it's current state?" Within the bounds of the examples discussed here, correct. Outbound Direct messages to the SwitchLinc do provide an On Level in the ACK from the SwitchLinc so "never" does not apply everything.
-
That is the result of a Stop Manual Change being issued by the device when paddle is released. The ISY estimates the current device On Level based on the time between the Start Manual Change and the Stop Manual Change. That process has the same exposure to being wrong when the Local On Level is defined at 50% for example and the On paddle is pressed a second time to bring SwitchLinc to 100% On. Holding the Off paddle to Start Manual Change (down) long enough to bring device to 50% On will show device as Off by the ISY. This is the result of the ISY thinking the device was at 50% (defined Local On Level) to start with even though device really at 100%. The estimated On Level when the Stop Manual Change message is received.is Off but the device is physically at 50% because it started from 100% On, not the 50% the ISY thinks the device started at.
-
Those are messages are generated by the ISY. The ISY found the device Off so marks the device to the Local On Level. Those ISY messages to not get generated by the second On paddle press because device is not Off. Tue 02/02/2016 10:21:51 AM : [iNST-SRX ] 02 50 3C.75.CD 00.00.01 CB 11 00 LTONRR (00) Tue 02/02/2016 10:21:51 AM : [std-Group ] 3C.75.CD-->Group=1, Max Hops=3, Hops Left=2 Tue 02/02/2016 10:21:51 AM : [D2D EVENT ] Event [3C 75 CD 1] [DON] [0] uom=0 prec=-1 Tue 02/02/2016 10:21:51 AM : [ 3C 75 CD 1] DON 0 Tue 02/02/2016 10:21:51 AM : [D2D EVENT ] Event [3C 75 CD 1] [sT] [127] uom=0 prec=-1 Tue 02/02/2016 10:21:51 AM : [ 3C 75 CD 1] ST 127
-
Are the A-D buttons Responders (or Controllers) in those Scenes?
-
Unfortunately that is expected of the SwitchLinc. Does not apply to all Insteon devices. Also when the SwitchLinc is a Controller of a Scene, the SwitchLinc Controller goes to 100% with second press but the Responder SwitchLinc remains at the Responder defined On Level. The Responder SwitchLinc does not go to 100% with second On message. Tue 02/02/2016 10:21:51 AM : [iNST-SRX ] 02 50 3C.75.CD 00.00.01 CB 11 00 LTONRR (00) - the device presents the same message whether going to 50% or going to 100% Tue 02/02/2016 10:21:51 AM : [std-Group ] 3C.75.CD-->Group=1, Max Hops=3, Hops Left=2 Tue 02/02/2016 10:21:51 AM : [D2D EVENT ] Event [3C 75 CD 1] [DON] [0] uom=0 prec=-1 Tue 02/02/2016 10:21:51 AM : [ 3C 75 CD 1] DON 0 Tue 02/02/2016 10:21:51 AM : [D2D EVENT ] Event [3C 75 CD 1] [sT] [127] uom=0 prec=-1 Tue 02/02/2016 10:21:51 AM : [ 3C 75 CD 1] ST 127 Tue 02/02/2016 10:21:51 AM : [iNST-SRX ] 02 50 3C.75.CD 19.6E.0A 40 11 01 LTONRR (01) Tue 02/02/2016 10:21:51 AM : [std-Cleanup ] 3C.75.CD-->ISY/PLM Group=1, Max Hops=0, Hops Left=0 Tue 02/02/2016 10:21:51 AM : [iNST-DUP ] Previous message ignored. Tue 02/02/2016 10:21:51 AM : [iNST-SRX ] 02 50 3C.75.CD 11.01.01 CB 06 00 (00) - second press of On paddle presents the same message sequence even though going to a different Local On value. Tue 02/02/2016 10:21:51 AM : [std-Group ] 3C.75.CD-->11.01.01, Max Hops=3, Hops Left=2 Tue 02/02/2016 10:21:51 AM : [iNST-INFO ] Previous message ignored. Tue 02/02/2016 10:22:13 AM : [iNST-SRX ] 02 50 3C.75.CD 00.00.01 CB 11 00 LTONRR (00) Tue 02/02/2016 10:22:13 AM : [std-Group ] 3C.75.CD-->Group=1, Max Hops=3, Hops Left=2 Tue 02/02/2016 10:22:13 AM : [D2D EVENT ] Event [3C 75 CD 1] [DON] [0] uom=0 prec=-1 Tue 02/02/2016 10:22:13 AM : [ 3C 75 CD 1] DON 0 Tue 02/02/2016 10:22:13 AM : [iNST-SRX ] 02 50 3C.75.CD 19.6E.0A 40 11 01 LTONRR (01) Tue 02/02/2016 10:22:13 AM : [std-Cleanup ] 3C.75.CD-->ISY/PLM Group=1, Max Hops=0, Hops Left=0 Tue 02/02/2016 10:22:13 AM : [iNST-DUP ] Previous message ignored. Tue 02/02/2016 10:22:13 AM : [iNST-SRX ] 02 50 3C.75.CD 11.01.01 CB 06 00 (00) Tue 02/02/2016 10:22:13 AM : [std-Group ] 3C.75.CD-->11.01.01, Max Hops=3, Hops Left=2 Tue 02/02/2016 10:22:13 AM : [iNST-INFO ] Previous message ignored.
-
The Red KPL load wire is not connected to the FanLinc. Just as a LampLinc is always powered by 120v and turned On/Off by Insteon messages from a different Insteon Controller, same with the FanLinc. FanLinc is always powered by 120v with the FanLinc Light and FanLinc Fan controlled by Insteon messages from another Controller, KPL buttons in the case. The KPL Main (8 button) or KPL ON/OFF (6 button) can control the FanLinc Light by having the KPL button a Controller of a Scene with the FanLinc Light the Responder without the KPL Red wire connected to FanLinc.
-
"My question is, can the Query trigger program state changes if it finds things different than the current ISY memory shows and thus run programs?" Yes, the Query on an ISY power up can find a different device Status. The change of Status can trigger a Program. Battery powered devices cannot be queried.
-
"or when you send a command directly to the device from the ISY. All correct?" Very good. Your understanding is correct on all aspects except for the last point. Sending a command to a device, either through the Admin Console buttons or a Set 'devicex' On, is sending an Insteon Direct command (rather than a Scene command) which does not use link records. Insteon is not complex when evaluating the actual Insteon command involved. Feel free to post addition questions as they come up. Also looking at the insteon.com developer information can be helpful. Even if the specific question/answer is not found useful information about Insteon workings is often found.
-
This looks like a File | Delete Modem (PLM) was issued, Garage Door Sensor Device Links: 0 : 0FF8 : A2 00 00.00.00 FF 1F 01 1 : 0FF0 : E2 01 1C.FC.B2 FF 1F 01 2 : 0FE8 : A2 00 1C.FC.B2 00 00 00 3 : 0FE0 : A2 00 34.E6.05 00 00 00 4 : 0FD8 : 00 00 00.00.00 00 00 00 Garage Door Sensor ISY Links: 0 : 0FF8 : 00 00 00.00.00 00 00 00 As Paul has already indicated a Restore of the ISY taken before the PLM was replaced is required. The I/O Linc Sensor must have a Controller link (starts with E2 01 xx.yy.zz ......) pointing to the new PLM address. xx.yy.zz
-
The EZIO8SA/PLM combination is added to the ISY as any other Insteon device. All linking is done under the ISY. The first 4 Inputs are opto isolated which can be operated with 3-30v DC or switch such as a magnetic contact. The 8 Outputs operate 24v DC, 3A loads. I have a few EZIO8SA devices. The only issue has been operating a combination of Outputs at the same time with a Scene. No issues operating individual Outputs. Smartenit offers a free utility (Simplehomenet Utility Suite) for custom control of EZIO8SA features. This requires an additional PLM (or shutdown ISY and use that PLM) for the Utility to communicate with the EZIO8SA/PLM.
-
There actually is no difference from Insteon perspective as an Insteon Scene is specified. In this example ISY Scene xxxx Device1 - Controller Device2 - Controller Device3 - Responder There are three Insteon Scenes. Scene xxxx (PLM is Controller) represents Insteon Scene 1. Device1 is a Controller of Insteon Scene 2 Device2 is a Controller of Insteon Scene 3. The Adjust Scene action requires an Insteon Scene Controller in the first parameter (In Scene). This parameter provides the Insteon address of the Scene Controller. This Insteon address identifies the link record in the Responder device being changed by the Adjust Scene statement. The second parameter identifies the Scene Responder device that contains the link database being adjusted. In Scene 'Device1' Set 'Device3' 50% (On Level) In Scene 'xxxx' Set 'Device3' 20% (On Level) It makes more sense when the Insteon technology is understood and that three Scenes are actually defined.