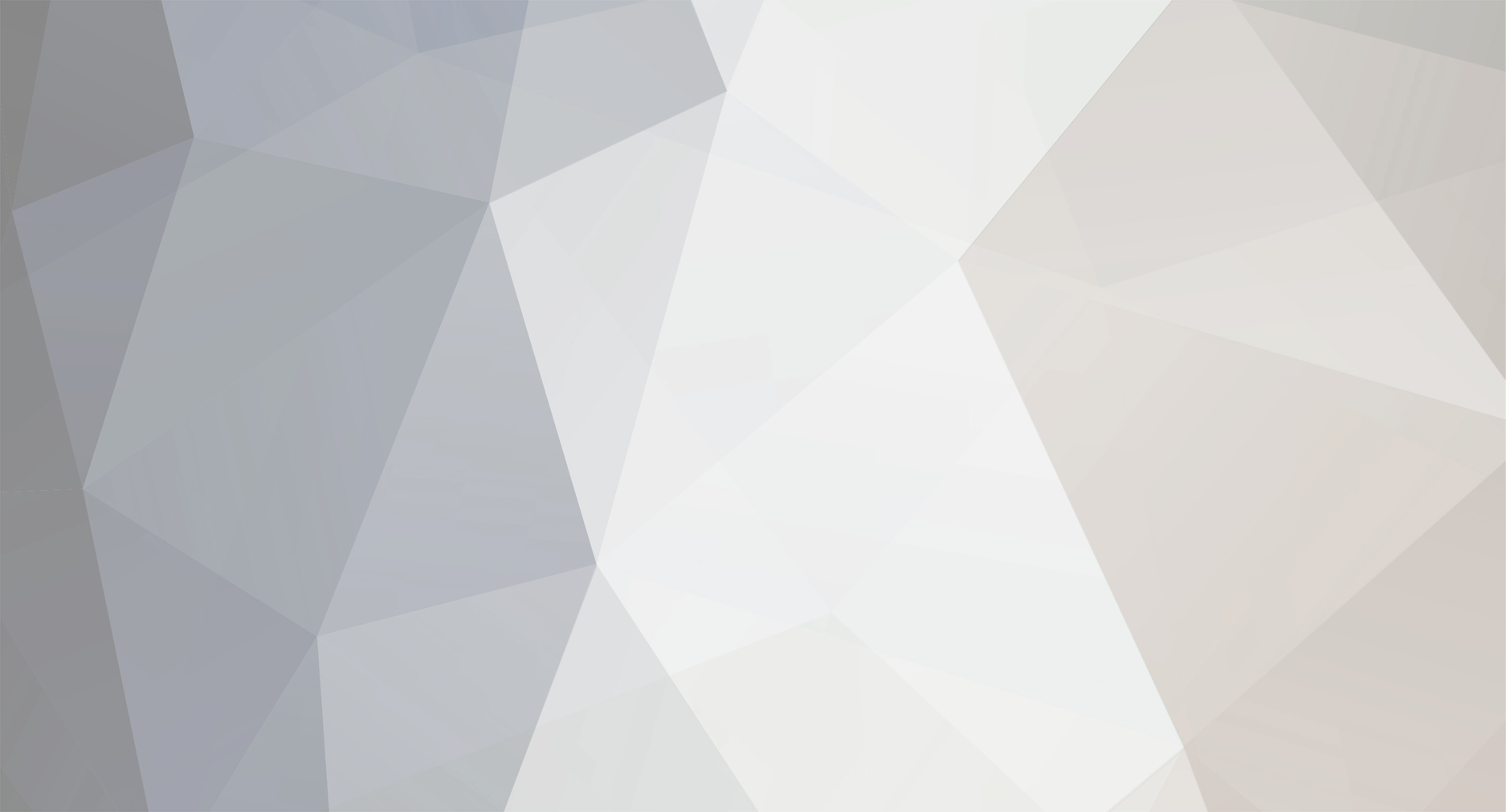
LeeG
Members-
Posts
12943 -
Joined
-
Last visited
Everything posted by LeeG
-
I don't know the answer to any of your questions. Keep in mind the 2413 is powering an RF transmitter and receiver which the 2412 did not. Trying to power an external device such as the ISY along with the additional load to power RF might overload the 2413 power supply.
-
The EZIO2X4 indicated it has an I2 engine which means the internal PLM was reflashed back to a pre I2CS level. It identified itself as an EZIO2X4. The EZIO2X4 was not factory reset before adding it back to the ISY. Both relays were On, Input 2 was On, and the link database was not cleared. There were no errors in the event trace, the 4 Input link records were written starting at 1FF8 which is expected for a 2413 shell (no passthru outlet), and the Inputs were assigned the expected Group numbers of 09-0C. The only issue is the EZIO2X4 was in an unknown configuration because it was not factory reset. Are Inputs 3 & 4 locked to Gnd or connected to pull-up resisters to keep these Inputs from cycling falsely? Because these Inputs can function in Analog mode they have no built-in pull-up resisters so it is necessary to connect these Inputs to either Gnd or to +5V through pull-up resisters to keep them from potentially cycling because the Inputs are floating electrically. If the Inputs are not showing state changes (and all the other Insteon devices are) I would perform a factory reset on the EZIO2X4 and add it back to the ISY after the factory reset.
-
Repeating the same steps will not likely product different results. First thing to try is a Restore Modem (PLM) to compress PLM link database in case it is full. If that does not result in the Input state changes appearing (assuming other devices do show state changes), Delete the EZIO2X4, Factory Reset the EZIO2X4, run Tools | Diagnostics | Event Viewer at LEVEL 3, add the EZIO2X4 using New Insteon Device. Enter Insteon address, Name of choice, leave Device Type set to default Auto Discover. Post the event trace.
-
Communication with the EZIO2X4 is excellent. Since a Restore Device did not resolve it could be the location of the link records in the EZIO2X4, other configuration information established when the EZIO2X4 was added to the ISY has gotten scrambled, level of firmware in the internal PLM in the EZIO2X4, the PLM link database is full, maybe some other things that have surfaced along the way that I do not immediately remember. The EZIO2X4 does not need anything updated by the Simplehomenet Utility Suite for the Inputs to report state changes to the ISY. How long ago was the EZIO2X4 purchased and from what company? Does the EZIO2X4 have a passthru outlet on the front of the device? Is the EZIO2X4 added to the 99i at 3.3.10 or the 994i at 4.0.5?
-
unispeed I have 2 EZIO2X4s in the garage where the Inputs monitor two garage doors at four locations (fully closed and fully open on both doors) as well as the control the garage door opener. Working on a 99i with 3.3.10 and various earlier ISY releases over several years. Have several EZIO2X4s in a test bed with an ISY at 4.0.5. They all report Input state changes without a Query. Several product variations have been shipped by Simplehomenet/Smartenit over the years so it is difficult to say why your Inputs are not showing state changes. The analysis can be time consuming and complex but the why can be determined if you want to spend the time.
-
The Program logic does not false unless a change was not saved. The ISY might not see the fan status change if there is a comm problem between the device controlling the fan and the PLM. What is controlling the fan?
-
The program turns the fan Off 30 minutes after sending the text.
-
The KeypadLinc Backlight level applies to the entire KPL, not a specific KPL button. Secondary KPL button LEDs can be turned On and Off with a Program. Define an ISY Scene XXXX with KPL1 button C as Responder. If another KPL should reflect the same information add KPL2 button C as another Responder to the same Scene. The Program turns the Scene XXXX On and Off to turn the Secondary KPL button(s) On and Off. A Secondary KPL button cannot be turned On/Off with a Direct command. The default erase existing links is the best choice. How would the ISY programs run if the ISY is unhooked? What do you mean by unhooked? Unhooked from what, router, PLM, power?
-
Do not delete the old KPL definition, it will be needed. The old KPL can be physically replaced with the new KPL as the Replace With function does not send commands to the old KPL. Add the new KPL to the ISY under a dummy name. Right click the old KPL primary node, select Replace xxxxx with .... A popup is displayed with the KPLs that match the characteristics of the old KPL. Select the new KPL dummy name. The new KPL link database will be built based on the old KPL Scene usage. All other device references to the old KPL Insteon address will be updated with the new KPL Insteon address. The old KPL nodes will have the Insteon address changed to the new KPL address. Scene and Program references will continue to use the original old KPL node names. The new KPL definition using the dummy name will be Deleted automatically and the Admin Console shut down so there will not be two KPL definitions with the same Insteon address. If the Insteon mesh network is unreliable things can get ugly as lots of Insteon message activity is needed to make all the changes. DO NOT put any of the battery RF devices into linking mode. The updates (if any) will fail and the changes will be queued. Once the Admin Console has been restarted put one battery device at a time into linking mode and select Write Updates to Device. As Xathros has already mentioned the old and new KPL must have the same characteristics.
-
The old 2412S supported 2000+ physically but there were issues with the speed of the PLM searching the link database when the number of links approached 1000+. The 2413 resolved the problem by reducing to number of links supported and using a faster processor. Try another Restore Modem (PLM). You may find that some of those link records are compressed out.
-
Was the Motion Sensor manually placed into linking mode with the Set button when the Scene was created? That is necessary to keep the Motion Sensor awake so the appropriate link records can be written into the Motion Sensor. Does the Motion Sensor Red LED blink multiple times when it senses motion? This indicates a motion sensor responder did not ACK messages from the motion sensor.
-
One Scene should cover the requirements. The KeypadLinc button H is added as a Controller, the Micro Relay On/Off as a Responder. The KeypadLinc button H IS NOT added to the Scene as a Responder as the ISY assumes the button is a Responder when the button is added as a Controller. The Program turns the Scene On/Off so the KPL button LED stays in sync with the status of the Micro Relay. I would not do a Replace With until some diagnostic procedures are run. The KeypadLincs must be the same type, Relay for Relay, Dimmer for Dimmer for a Replace With. A Relay cannot Replace a Dimmer for example. The Primary KeypadLinc node has the Replace With option. The first question is what Xathros asked, is the KPL button in non-toggle mode? Does the KPL button LED toggle On and Off as the button is pressed? If in non-toggle mode it will blink twice when pressed. The best test to rule out a KPL issue is to run Tools | Diagnostics | Event Viewer at LEVEL 3. Press button H On, then press button H Off. Does the event trace show the KPL button sent an On command, then sent an Off command. Post the event trace if the results are in question. A Scene cannot be added to a Scene. Insteon does not support that. All the individual devices must added to the Scene. A specific node can be a Controller of only one Scene. Again this is an Insteon requirement.
-
I do not think so. Generating a false X10 message is certainly possible if the noise is substantial. X10 is only a few bytes with no validation. Insteon messages are much more complex. The all have a CRC (cyclic redundancy character) and the new Extended messages also carry a check sum character for additional validation. Noise can certainly destroy an Insteon message but I have never heard of noise forming an Insteon message. All that equipment should be on a FilterLinc but not because it might generate a false Insteon message.
-
The On/Off Outdoor Module 2634-222 (outdoor ApplianceLinc) is a Dual Band device. Much cheaper than an ApplianceLinc plus Access Point. Some folks run the PLM on the filtered side a FilterLinc to force RF only and avoid powerline issues in their environment so I would not expect problems running the Outdoor Module from the filtered side of a FilterLinc.
-
bluzmann Although not mentioned I assume the door and window sensors are Wireless Open/Close Sensors (TriggerLincs). These are battery powered devices which sleep (turn Off RF) when not sending a state change message. They cannot be Queried and have no Responder function (cannot be turned On/Off from the ISY) which is why the Scene Test indicates Ignored. Would be the same for Motion Sensor, Mini Remote, etc.
-
madcodger Thanks for the information on the wireless temp sensor. I am amazed that the unit can be placed inside a refrig and have the RF signal transmit through the metal shell of the refrig. If the deck of cards box is placed inside the freezer how long does the battery last in below freezing temps. Have you got a product number for the device. I would like to look at the product details.
-
The RF transmitter and antenna are inside the refrig? I took the question to be centered around Insteon placing a wireless thermostat inside the refig. There are no Insteon based remote temp sensing solutions I am aware of other than a wireless thermostat that would work with the ISY. There are boards that accept various sensors that can send REST commands over IP to the ISY but that seems more complex than what the OP was asking for.
-
It will not work inside a refrigerator as the RF cannot go through metal shell of the refrigerator. Also temp inside is likely outside the device operating range. There are posts that document how to connect an external temp sensor in place of the internal sensor.
-
What Anti Virus is being used? The lack of the buttons and the lack of File options indicates the ISY is not able to push data out to the Admin Console. This is usually the result of AV blocking the push of data from the ISY.
-
BobH All the conditions have to be True for the Then clause to run as one would want. If any of the conditions are False the Else clause runs. That generally results in the Else clause running when not desired.
-
The 3.2.6 level of firmware is very old. If using a 99i the latest is 3.3.10.
-
With such a long device name the meaningful part of each node name is missing. Sensor is the node that reflects motion sensed. Dusk/Dawn is the node that reflect when the environment is Dark. Low Battery is the node that reflects a low battery condition. Not sure if the full node names are actually truncated or just not displayed. Move the vertical separator between the node names and right side display to the right. If the full names are not there I suggest picking a shorter name for the motion sensor.
-
The link database in the I/O Linc is emply according to the last post. The Sensor cannot report state changes without the necessary links. A Show ISY Links Table for the I/O Linc will display what the ISY thinks should be in the I/O Linc. With the poor comm the ISY might not have been able to rewrite the link database in the I/O Linc. Since a Restore Device did not work, Delete the I/O Linc and add it back to the ISY. It is possible this will not work with the comm the way it is. It the I/O Linc adds successfully run the Show Device Links Table again. What is the ISY firmware level? To see the Sensor state change messages in the event trace it is necessary to connect/disconnect the Gnd/Sensor connection.
-
The 4 tap Set button test is described in the Access Point User Guide. It is the test that is used to verify the Access Points are actually plugged into opposite 120v legs. I have no way of knowing what comm. was like before but at present comm. is very poor. Moving the I/O Linc to the PLM plug point will confirm the link records that support the I/O Linc Sensor are correct.
-
There is poor and changing reliability in communication with the I/O Linc location. The Hops Left=x count should be stabile and Hops Left=0 is as poor as communication can get and still have an effect. Look into what is being used to couple the two 120v legs. Do they pass the 4 tap Set button test? What is on the I/O Linc circuit? Noisy CFL or florescent lighting. Distance from PLM location to I/O Linc location. Tue 09/17/2013 02:35:35 PM : [standard-Direct Ack][19.61.92-->ISY/PLM Group=0] Max Hops=3, Hops Left=2 Tue 09/17/2013 02:35:41 PM : [standard-Direct Ack][19.61.92-->ISY/PLM Group=0] Max Hops=3, Hops Left=1 Tue 09/17/2013 02:35:59 PM : [standard-Direct Ack][19.61.92-->ISY/PLM Group=0] Max Hops=3, Hops Left=0 Tue 09/17/2013 02:36:01 PM : [standard-Direct Ack][19.61.92-->ISY/PLM Group=0] Max Hops=3, Hops Left=0 Tue 09/17/2013 02:36:20 PM : [standard-Direct Ack][19.61.92-->ISY/PLM Group=0] Max Hops=3, Hops Left=1 Tue 09/17/2013 02:36:24 PM : [standard-Direct Ack][19.61.92-->ISY/PLM Group=0] Max Hops=3, Hops Left=0