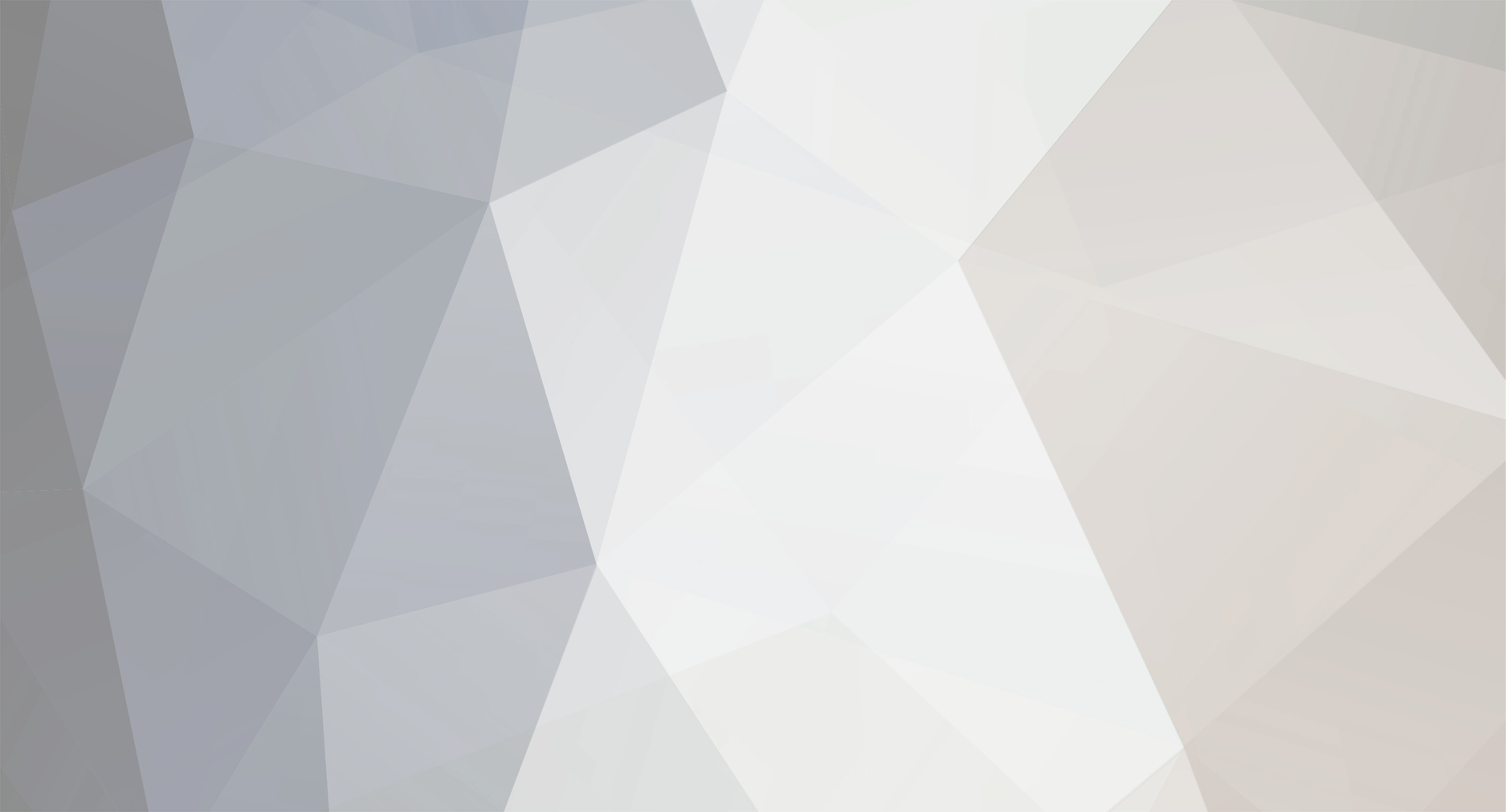
LeeG
Members-
Posts
12943 -
Joined
-
Last visited
Everything posted by LeeG
-
A Factory Reset should be done to remove any configuration that was done before. If a Factory Reset is done after adding to the ISY a Restore Device has to be done to rebuild the link database after the reset. Are you thinking there are four defective devices, they work some of the time, not others. With comm. problems being dismissed there are not too many possibilities left.
-
You need three MorningLincs to control three locksets independently. The lockset is linked to the MorningLinc. These are NOT Insteon type links. The MorningLinc can be Factory Reset and the MorningLinc Set button will still control the lockset(s). The ISY has no knowledge that three locksets have been linked to the MorningLinc and has no way of controlling only one individual lockset.
-
The If Status is checking the Status ISY maintains within itself. Since the Set button is being used to fill the blank Current State column and the Set button tap can cause a Wet state message to be sent, the ISY Current State (Status) could say Wet node On from the Set button tap. Should the Leak Sensor send a Wet node On because a leak is actually detected the Status would not change because the Set button tap had already set the Status to Wet. If Status triggers a Program only when the Status changes. If Control is looking at the command flowing from the Leak Sensor. Therefore If Control will trigger the Program regardless of whether the Status was already Wet from the Set button tap. If Control 'leaksensor - Wet' is switched On will trigger the Program on a leak regardless of what the Set button tap sent.
-
Thanks for information update. 3.3.10 (the latest firmware for a 99i) does not have Heartbeat support. If you move to a 994 at some point the Leak Sensors will have to be Deleted from the ISY and added back to pick up the third node which supports the Heartbeat. The Leak Sensor is completely functional at 3.3.10 as far as detecting Wet conditions and sending the indication to the ISY. The Status will be blank unless/until the Set button is tapped (or an actual Wet condition occurs) which really does not mean much since the Set button sends a test message, not the actual Wet/Dry state of the Leak Sensor. A blank Status does not hurt anything. A Program that is triggering on a If Status change to Wet will work so long as the Set button tap message did not send a Wet message (each Set button tap sends an alternating message). A Set button tap sends a Dry message, the next Set button tap sends a Wet message. A Program written to trigger with If Control is a better option as the Program triggers regardless of the current Status.
-
Going back to the initial post I see you have an ISY 99i (assuming the missing 4 was not a typo). 3.3.10 does not have Heartbeat support. That would explain your situation. Without the Heartbeat the Leak Sensor would not be expected to send any messages for months at a time unless the Set button is tapped to send the test messages. After that the ISY remembers that Status until the next power outage.
-
I missed a specific answer. Yes, the Heartbeat message does carry the current Dry/Wet status of the Leak Sensor. The Heartbeat message will set Status of the three nodes if it is changed by the Heartbeat message.
-
What firmware level ISY is being used? How many nodes are listed for the Leak Sensor? There should be three nodes. The Heartbeat support was added at 4.0.1. The Leak Sensor had to be Deleted and added back after 4.0.x is installed for the Heartbeat to work.
-
"Once I perform the manual activation, the sensors report their status with 100% accuracy." How have you confirmed this? Have you made them Wet then Dry to verify the Status change shows in the Admin Console. Since the Leak Sensor normally does not send anything except the Heartbeat message for months at a time how has the operation of the device been verified? "How do I test for the "heartbeat"? And should the "heartbeat" result in a status reporting?" Run Tools | Diagnostics | Event Viewer at LEVEL 3. Tap the Set button on a Leak Sensor. Approx 10 seconds after sending either a Dry or Wet message the Leak Sensor sends a Heartbeat message. The following is an example of what happens when the Set button is tapped. The first sequence is a Wet message (00.00.02). The Set button tap alternates between Wet and Dry so this could be a Dry message (00.00.01). This is followed by a Heartbeat message (00.00.04). Sun 07/21/2013 02:13:43 PM : [iNST-SRX ] 02 50 21.7A.CC 00.00.02 CB 11 02 LTONRR (02) Sun 07/21/2013 02:13:43 PM : [std-Group ] 21.7A.CC-->Group=2, Max Hops=3, Hops Left=2 Sun 07/21/2013 02:13:43 PM : [ 21 7A CC 2] DON 2 Sun 07/21/2013 02:13:43 PM : [ 21 7A CC 2] ST 255 Sun 07/21/2013 02:13:43 PM : [ 21 7A CC 1] ST 0 Sun 07/21/2013 02:13:44 PM : [iNST-SRX ] 02 50 21.7A.CC 00.00.02 CB 11 02 LTONRR (02) Sun 07/21/2013 02:13:44 PM : [std-Group ] 21.7A.CC-->Group=2, Max Hops=3, Hops Left=2 Sun 07/21/2013 02:13:44 PM : [iNST-DUP ] Previous message ignored. Sun 07/21/2013 02:13:45 PM : [iNST-SRX ] 02 50 21.7A.CC 22.80.0B 41 11 02 LTONRR (02) Sun 07/21/2013 02:13:45 PM : [std-Cleanup ] 21.7A.CC-->ISY/PLM Group=2, Max Hops=1, Hops Left=0 Sun 07/21/2013 02:13:45 PM : [iNST-DUP ] Previous message ignored. Sun 07/21/2013 02:13:45 PM : [iNST-SRX ] 02 50 21.7A.CC 11.01.02 CB 06 00 (00) Sun 07/21/2013 02:13:45 PM : [std-Group ] 21.7A.CC-->11.01.02, Max Hops=3, Hops Left=2 Sun 07/21/2013 02:13:45 PM : [iNST-INFO ] Previous message ignored. Sun 07/21/2013 02:13:46 PM : [iNST-SRX ] 02 50 21.7A.CC 11.01.02 CB 06 00 (00) Sun 07/21/2013 02:13:46 PM : [std-Group ] 21.7A.CC-->11.01.02, Max Hops=3, Hops Left=2 Sun 07/21/2013 02:13:46 PM : [iNST-INFO ] Previous message ignored. Sun 07/21/2013 02:13:59 PM : [iNST-SRX ] 02 50 21.7A.CC 00.00.04 CB 11 04 LTONRR (04) Sun 07/21/2013 02:13:59 PM : [std-Group ] 21.7A.CC-->Group=4, Max Hops=3, Hops Left=2 Sun 07/21/2013 02:13:59 PM : [ 21 7A CC 4] DON 4 Sun 07/21/2013 02:13:59 PM : [ 21 7A CC 1] ST 255 Sun 07/21/2013 02:13:59 PM : [ 21 7A CC 2] ST 0 Sun 07/21/2013 02:14:00 PM : [iNST-SRX ] 02 50 21.7A.CC 00.00.04 CB 11 04 LTONRR (04) Sun 07/21/2013 02:14:00 PM : [std-Group ] 21.7A.CC-->Group=4, Max Hops=3, Hops Left=2 Sun 07/21/2013 02:14:00 PM : [iNST-DUP ] Previous message ignored. Sun 07/21/2013 02:14:02 PM : [iNST-SRX ] 02 50 21.7A.CC 22.80.0B 41 11 04 LTONRR (04) Sun 07/21/2013 02:14:02 PM : [std-Cleanup ] 21.7A.CC-->ISY/PLM Group=4, Max Hops=1, Hops Left=0 Sun 07/21/2013 02:14:02 PM : [iNST-DUP ] Previous message ignored. Sun 07/21/2013 02:14:02 PM : [iNST-SRX ] 02 50 21.7A.CC 11.01.04 CB 06 00 (00) Sun 07/21/2013 02:14:02 PM : [std-Group ] 21.7A.CC-->11.01.04, Max Hops=3, Hops Left=2 Sun 07/21/2013 02:14:02 PM : [iNST-INFO ] Previous message ignored. Sun 07/21/2013 02:14:03 PM : [iNST-SRX ] 02 50 21.7A.CC 11.01.04 CB 06 00 (00) Sun 07/21/2013 02:14:03 PM : [std-Group ] 21.7A.CC-->11.01.04, Max Hops=3, Hops Left=2 Sun 07/21/2013 02:14:03 PM : [iNST-INFO ] Previous message ignored. The Heartbeat can be monitored with an ISY Program. An example follows. The X10 message is a test message that is not issued unless the Heartbeat fails to arrive. A Notify would likely be better for most. If Control 'Leak Sensor-Heartbeat' is switched On Or Control 'Leak Sensor-Heartbeat' is switched Off Then Wait 25 hours Send X10 'A10/All Lights On (5)' Else - No Actions - (To add one, press 'Action')
-
I don't use MobiLinc but I would expect it to have the latest information. Perhaps some refresh is needed. Log in to the Admin Console. If it does not show Leak Sensor status after 24 hours there is an issue. Could be RF communication problem, battery in Leak Sensor although they are supposed to last for some 10 years, or a link record problem. Run Tools | Diagnostics | Event Viewer at LEVEL 3. Tap the Set button on the Leak Sensor. It should send a message either Dry or Wet (the Set test cycles between the two) as well as 10 seconds later a test Heartbeat message. If Leak Sensor messages are not seen perhaps an Access Point or whatever device the Leak Sensor normally communicates with did not come back after the power outage. See if other devices show real time status changes as lights are turned On/Off manually at the device. The PLM could have lost link records from the power outage but that would not be normal for a simple power drop.
-
"1. When power is restored, if a subsequent leak occurs, will the leak sensor send a notice?" Sure. Just like a RemoteLinc2, Motion Sensor, TriggerLinc, etc battery powered RF devices cannot be queried because they sleep to save battery life. The next message from the Leak Sensor will update the Status. Being that these devices are battery powered they know nothing about the power interruption and are not affected by it. "2. Does this sensor send a "heartbeat" every 24 hrs? If yes, will that restore the sensor status to the ISY (and MobiLinc Pro)?" Yes, the Heartbeat message is sent nominally every 24 hours. It carries the current state of the Leak Sensor (Dry or Wet) which will update the Leak Sensor nodes.
-
Is button C as Responder set to 0% On Level when the Red button G node name below the Scene name is selected? Controlling responders of button C with button G should not have any effect on button C unless button C is part of the Scene with button G as a Controller. Insteon does not propagate Scene behavior by turning Responders turn into Controllers. What ISY firmware? Click Help | About, what is displayed for Firmware and UI? What is the firmware level of the KPL? If multiple KPLs participate in a given Scene a minimum KPL firmware of v.40 is required for KPL A button G to turn Off KPL B button C with a 0% On Level. Before v.40 the KPL did not honor a 0% On Level for Secondary KPL buttons.
-
"Is there a way to completely disable/prevent an "ALL ON" event from being broadcast by the PLM?" No, even if it was specifically sent to the PLM as a serial command to send. This sounds like something different from an explicit send of an ALL ON through the PLM.
-
Has to be done with two different Scenes or with two Direct commands. The nature of an Insteon Scene is for all the devices in the Scene to react essentially simultaneously. A single Insteon Scene message is issued with all the Responders of the Scene reacting as the message is received. If the SPA READY device requires some seconds to react insert a Wait between issuing the two Scene or two Direct commands.
-
The Heartbeat message contains an On command when the Leak Sensor is Dry. The Heartbeat message contains an Off command when the Leak Sensor is Wet. That is how the Heartbeat message updates the Wet/Dry state of the Leak Sensor every 24 hours. When checking the Heartbeat node 'If Control' is the correct means of testing as the Heartbeat message will normally contain an On command each 24 hours as the Leak Sensor is normally Dry. If Status does not work because most of the time the Heartbeat node will be On so there is no Status change to trigger a Heartbeat Program. It is necessary to check the Heartbeat node for both 'If Control xxxx is switched On Or If Control xxxx is switched Off' as the command in the Heartbeat message depends on the Dry/Wet state of the Leak Sensor.
-
I'll see if I have an Event trace archived with the Heartbeat message. I turned On the Event Viewer to catch the next one but I don't know the real clock time of the 24 hour cycle of the Leak Sensor. As I remember it the Heartbeat node gets an On command every 24 hours. The ISY does not have a 24 hour clock running for each Leak Sensor so the ISY is not going to alter the Status of the Heartbeat node if it does not hear something in 24 hours. That is what the Program I posted does. If nothing comes from the Leak Sensor node for more than 24 hours the Program does something. I picked 25 hours because I was not sure how accurate a battery powered clock would be keeping a 24 hour elapsed time. Any check of the Heartbeat node needs to be in the 'If Control' format. As I remember the "Status" of the Heartbeat node is not going to change because only On commands come from the Heartbeat Group so 'If Status' is not appropriate. The problem is all my testing of the Leak Sensor was quite some time ago so I am going on memory. The next event trace will help if I did not save a trace file of the Leak Sensor testing.
-
MWareman This is a Program I use to test the Heartbeat. If the Wait ever completes the Leak Sensor has failed to send a Heartbeat. A Notify would be more logical after the Wait. If Control 'Leak Sensor-Heartbeat' is switched On Or Control 'Leak Sensor-Heartbeat' is switched Off Then Wait 25 hours Send X10 'A10/All Lights On (5)' Else - No Actions - (To add one, press 'Action') Regarding the blank Status, if the Leak Sensor went Wet during a power outage and remains Wet the Leak Sensor does not send another Wet. It requires a Heartbeat message which indicates the Wet/Dry state of the Leak Sensor along with the Heartbeat itself. If the Leak Sensor went Wet during the power outage and goes back to Dry before power comes back the Leak Sensor sends another Wet if it goes Wet again. If that happens after power is restored the Status will be set to Wet on the next leak. Having said all that the Leak Sensor is sensitive to the conductivity of water as all Leak Sensors are. I found it common for the Leak Sensor the cycle Wet to Dry to Wet as it is sitting in a Wet situation. Although not an absolute I suspect the Leak Sensor would cycle Dry/Wet/Dry/Wet well before the 24 hour Heartbeat. Also since the Heartbeat is on the Leak Sensors 24 hour clock, not when power is restored, the Heartbeat will likely happen before a full 24 hours when power comes back unless power just happen to be restored a few seconds after the last Heartbeat message
-
"My question is wheter ISY takes control of the "LED BRIGHTNESS" setting in the device," Depends on whether the device hardware/firmware supports changing that programmatically. I do not have a list of feature versus device firmware when something is released. It would be nice if SmartLabs/Smarthome had a central location with that information but it does not exist (or its one of the world’s best kept secrets). The ISY does not have a history of device versus firmware versus feature. The option is presented and it works where the device supports it. "i.e. 10% would set it to 25?" Yes, 25 is 10% of 255 depending on how the result is rounded. Could be 26. “What is the 7 and 12 in my case reference to?†If the device is looking for Off/On numbers the 7 & 12 are the LED Backlight On level. The Off level is always adjusted by the device so there is a consistent visual difference between Off and On LED brightness. “There is a "LED BRIGHTNESS" setting in the GUI window even on the old SWL's, question is whether that is a usable feature?†If the device hardware/firmware support it. The ISY does not have a history of device versus firmware versus feature. “Too old to find any leaflets on them, they are original equipment when Insteon came out.†I have an old KPL user guide which says KPL LED backlight level as two settings. Use A/D buttons on 6 button, C/F on 8 button to toggle between the two levels. An old SwitchLinc user guide does not describe changing LED backlight level. “Where is the trace utility?†Tools | Diagnostics | Event Viewer at LEVEL 3. Sorry for the slow response. Hit Ctrl something and lost the forum session. Had to retype
-
"If that's a problem, why is it only happening intermittently? " Nothing electronic does the same thing in "exactly" the same way each time. I would think if a dual trace scope was used to monitor the Sensor inputs that could occur at the "same time" there would always be some variability as to when the signal reaches two I/O Lincs. Plus the electronics in the I/O Linc has a variation. That does not consider how much variation there is on a powerline circuit. Insteon is sharing wires meant to carry 120/240 volts around a house. Even a cat5 cable has some variation and it is much cleaner than a pair of 120 volt wires. In a race condition there is always a winner and always a loser. Try running the Event Viewer at LEVEL 3 and create the situation where more than one I/O Linc Sensor is activated at the same time. By watching the Group messages that flow in that situation it should be possible to observe the interaction and interrelationship if any.
-
The ISY Query updates all the nodes for the device. Query a KPL and all the buttons are refreshed. Query the FanLinc and both nodes are queried. Otherwise 8 (or 5) queries would be required to sync a KPL. There may some Simplehomenet/Smartenit devices that operate differently because their command set is not standard. It does seem odd that an X10 signal would reach the PLM but the Insteon message would not. Messages coming from a device signaling an On/Off state change are Scene (Group) messages. Insteon supports only one Scene (Group) in progress at a time. Is it possible that more than one I/O Linc would have its Sensor change state at the same time?
-
"The 25 I see in the ISY window is (10% of 255) which is the max brightness of the SWL? (I have 10% set during the day & 1% at night)." What ISY window are you referring to that contains 25? Can you post an screen clip? 10% is certainly not the max, 100% would be max. "My KPL's are set to 0 off (nothing) and 7 on at night (12 Day), what are those numbers?" If the KPL firmware is expecting an Off/On number that is the relative Off/On level of the LEDs. The device maintains a differential of 8 between the values regardless of the individual numbers so that Off and On are always visually distinguishable. What ISY firmware? device firmware? device type (relay/dimmer)? The reason I ask is that by 4.0.5 I thought the references had been changed to either a number from 1-255 or a %. "The older models of SWL's & KPL's in the other house---do they not have any adjustment of the LED or buttons, even though there is an option within ISY? Depends on the device firmware in each device? Not all old devices can be set programmatically. "Can you adjust the brightness outside of ISY?" Probably. Refer to the User Guide that applies to that specific device type at its firmware level. I don't have specific information as to what firmware level the various combinations of Switchlinc Dimmer/ Switchlinc Relay/KPL Dimmer/KPL Relay firmware was updated with that capability. SmartLabs/Smarthome does not provide a list of device type/firmware levels where each feature was added. "I have one SWL I changed out last year (v27) that the LED when off many times is Off completely and sometimes on??? Is it a faulty SWL or is there a program setting the level I don't know about?" I have no way of knowing without some trace information when the change happens. The Find facility may help in locating Programs which affect the device.
-
What ISY firmware are you using. Just about all the UI has been changed to a value of 1-255 or a % Backlight level. Also what is the firmware level of the KPL. Xathros suggestions could resolve the issue. If not keep in mind that if working with an older KPL that expects Off and On Backlight levels they do not operate independently. The KPL hardware/firmware will keep the On to Off ratio the equivalent of 8 increments apart regardless of the numbers entered. This is done so there is always a visible difference between a button that is On versus a button that is Off. The 1/7 values in the initial post are invalid for a KPL looking for separate Off/On values because there is not an 8 increment difference. The KPL will adjust the values internally to insure that separation always exists.
-
The Sense circuit is digital (5V DC), expecting the I/O Linc GND to turn the Sensor on. The I/O Linc could be damaged if 24 AC is applied to the Sense input. Also an AC voltage would cause the Sensor to cycle even if it did not destroy the I/O Linc which I suspect it would.
-
Yes, the ISY queries both nodes when either node is queried. The code I posted effectively issued 4 query commands for each Repeat loop. Below I issued the single Query of the I/O Linc Relay. The event trace has a query of the Sensor followed by a query of the Relay. Set 'IOLinc I2CS-Relay' Query Thu 07/18/2013 09:36:54 AM : [ Time] 09:36:54 1(0) Thu 07/18/2013 09:36:54 AM : [iNST-TX-I1 ] 02 62 1C FD D5 0F 19 01 Thu 07/18/2013 09:36:54 AM : [iNST-ACK ] 02 62 1C.FD.D5 0F 19 01 06 LTSREQ (01) Thu 07/18/2013 09:36:54 AM : [iNST-SRX ] 02 50 1C.FD.D5 22.80.0B 2B 00 00 (00) Thu 07/18/2013 09:36:54 AM : [std-Direct Ack] 1C.FD.D5-->ISY/PLM Group=0, Max Hops=3, Hops Left=2 Thu 07/18/2013 09:36:54 AM : [iNST-TX-I1 ] 02 62 1C FD D5 0F 19 00 Thu 07/18/2013 09:36:54 AM : [iNST-ACK ] 02 62 1C.FD.D5 0F 19 00 06 LTSREQ (LIGHT) Thu 07/18/2013 09:36:55 AM : [iNST-SRX ] 02 50 1C.FD.D5 22.80.0B 2B 00 FF (FF) Thu 07/18/2013 09:36:55 AM : [std-Direct Ack] 1C.FD.D5-->ISY/PLM Group=0, Max Hops=3, Hops Left=2 Not sure I understand the question about the Sensor reporting only when queried. The I/O Linc Sensor reports state changes in real time. If the Sensor node does not show a state change either a link record problem exists or there is a comm problem preventing the state change message from reaching the PLM. These are event entries from turning the Sensor Off and On after I did the query test. Thu 07/18/2013 09:45:01 AM : [iNST-SRX ] 02 50 1C.FD.D5 00.00.01 CB 13 00 LTOFFRR(00) Thu 07/18/2013 09:45:01 AM : [std-Group ] 1C.FD.D5-->Group=1, Max Hops=3, Hops Left=2 Thu 07/18/2013 09:45:01 AM : [ 1C FD D5 1] DOF 0 Thu 07/18/2013 09:45:01 AM : [iNST-SRX ] 02 50 1C.FD.D5 22.80.0B 41 13 01 LTOFFRR(01) Thu 07/18/2013 09:45:01 AM : [std-Cleanup ] 1C.FD.D5-->ISY/PLM Group=1, Max Hops=1, Hops Left=0 Thu 07/18/2013 09:45:01 AM : [iNST-DUP ] Previous message ignored. Thu 07/18/2013 09:45:02 AM : [iNST-SRX ] 02 50 1C.FD.D5 13.02.01 CB 06 00 (00) Thu 07/18/2013 09:45:02 AM : [std-Group ] 1C.FD.D5-->13.02.01, Max Hops=3, Hops Left=2 Thu 07/18/2013 09:45:02 AM : [iNST-INFO ] Previous message ignored. Thu 07/18/2013 09:45:05 AM : [iNST-SRX ] 02 50 1C.FD.D5 00.00.01 CB 11 00 LTONRR (00) Thu 07/18/2013 09:45:05 AM : [std-Group ] 1C.FD.D5-->Group=1, Max Hops=3, Hops Left=2 Thu 07/18/2013 09:45:05 AM : [ 1C FD D5 1] DON 0 Thu 07/18/2013 09:45:05 AM : [ 1C FD D5 1] ST 255 Thu 07/18/2013 09:45:05 AM : [iNST-SRX ] 02 50 1C.FD.D5 22.80.0B 41 11 01 LTONRR (01) Thu 07/18/2013 09:45:05 AM : [std-Cleanup ] 1C.FD.D5-->ISY/PLM Group=1, Max Hops=1, Hops Left=0 Thu 07/18/2013 09:45:05 AM : [iNST-DUP ] Previous message ignored. Thu 07/18/2013 09:45:05 AM : [iNST-SRX ] 02 50 1C.FD.D5 11.02.01 CB 06 00 (00) Thu 07/18/2013 09:45:05 AM : [std-Group ] 1C.FD.D5-->11.02.01, Max Hops=3, Hops Left=2 Thu 07/18/2013 09:45:05 AM : [iNST-INFO ] Previous message ignored.
-
Select 'Insteon', Scene names are listed after device names in the 'Set' pulldown
-
I have 4.0.5 changing the LED Backlight level of a v.38 SwitchLinc Dimmer. The Admin Console presents a number 1 - 256 which adjusts the backlight level. The Program UI selects a % so the numeric values are different between the Admin Console and the Program but both change the Backlight level. I don't think a v.27 supports a programmatic change in backlight level but do not have one to confirm with a direct test.