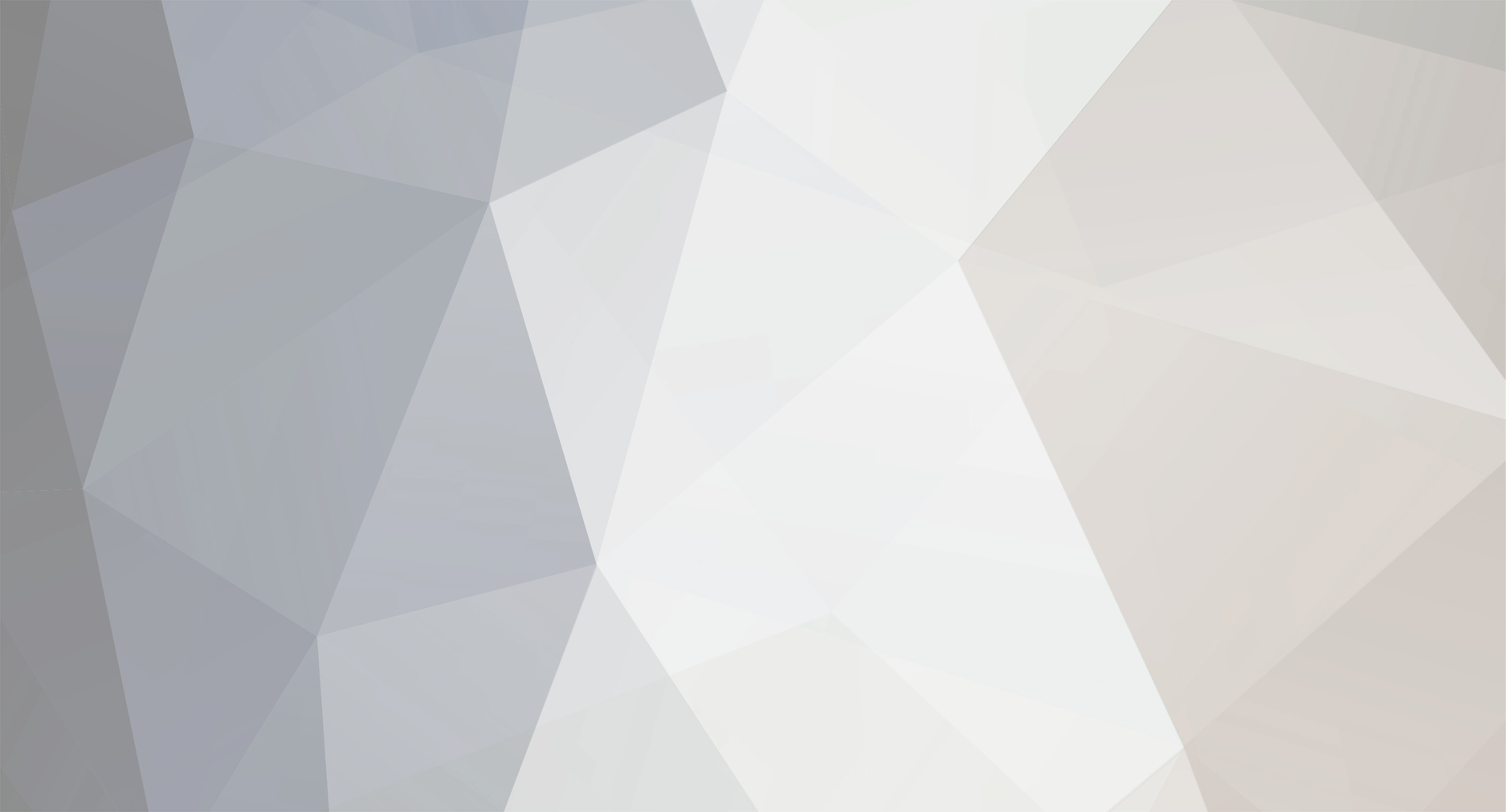
LeeG
Members-
Posts
12943 -
Joined
-
Last visited
Everything posted by LeeG
-
What normally happens is the load is damaged resulting in the load drawing more current than the dimmer is rated for. This results in the dimmer electronics being damaged. There are a some posts in the last few weeks by folks with digital scopes showing the actual sine wave produced by a dimmer at 100% On Level. About 20% of the leading edge of the sine wave is cut off. This can cause some loads to overheat and burn out. If the load opens no problem. The load just stops working If the load shorts out as a result of the damage then the current draw through the Triac in the dimmer exceeds its rating and it burns out. Take a look at this topic viewtopic.php?f=30&t=9110&p=69333&hilit=20%25+sine+wave#p69333
-
A Dimmer chops the AC signal to the load even at 100% On Level. This is fine for incandescent loads. This works with some non incandescent loads, this destroys some non incandescent loads. It can also destroy the Dimmer.
-
The expected sequence of messages looks like this Tue 08/21/2012 08:30:13 PM : [iNST-TX-I1 ] 02 62 1D AA D2 0F 19 00 Tue 08/21/2012 08:30:13 PM : [iNST-ACK ] 02 62 1D.AA.D2 0F 19 00 06 LTSREQ (LIGHT) Tue 08/21/2012 08:30:13 PM : [iNST-SRX ] 02 50 1D.AA.D2 1C.FC.92 2B 00 FF (FF) The first msg 02 62 is the serial command going to the PLM. The second msg 02 62 with an 06 on the end is the PLM echoing the command it just received The third msg 02 50 is the inbound response from the device. The sequence that produced the error annotation follows Tue 08/21/2012 08:32:46 PM : [iNST-TX-I1 ] 02 62 1D AA D2 0F 11 FF Tue 08/21/2012 08:32:46 PM : [iNST-ACK ] 02 62 1D.AA.D2 0F 11 FF 06 LTONRR (FF) Tue 08/21/2012 08:32:46 PM : [iNST-ACK ] 02 62 1D.AA.D2 0F 11 FF 06 LTONRR (FF): Received an ACK for a different device The first msg 02 62 is the serial command going to the PLM The second msg 02 62 with an 06 on the end is the PLM echoing the command is just received The third msg is unexpected. It is another PLM echo. It should have been an inbound 02 50 response from the device. The msg structure does not match what is expected, the inbound device address does not exist so the compare of what should have been an inbound device address does not match the outbound device address, thus the message text. There were two no device response sequences just before this. It may have gotten the PLM out of sync. Only a guess. This error will likely not occur once communication problems with the ApplianceLinc are resolved.
-
Okay, my error. Thought the use of a FilterLinc had been mentioned in a previous post.
-
There is very poor communication with the ApplianceLinc location. Max Hops=3 Hops Left=2 is as good as it gets. Tue 08/21/2012 08:30:13 PM : [standard-Direct Ack][1D.AA.D2-->ISY/PLM Group=0] Max Hops=3, Hops Left=2 Max Hops=3 Hops Left=0 is as bad as it gets and still have a response. The Hops Left is changing between commands which is also an indication of poor communication with the ApplianceLinc location. Tue 08/21/2012 08:30:21 PM : [standard-Direct Ack][1D.AA.D2-->ISY/PLM Group=0] Max Hops=3, Hops Left=0 Tue 08/21/2012 08:30:27 PM : [standard-Direct Ack][1D.AA.D2-->ISY/PLM Group=0] Max Hops=3, Hops Left=0. Tue 08/21/2012 08:30:29 PM : [standard-Direct Ack][1D.AA.D2-->ISY/PLM Group=0] Max Hops=3, Hops Left=2 Tue 08/21/2012 08:31:48 PM : [standard-Direct Ack][1D.AA.D2-->ISY/PLM Group=0] Max Hops=3, Hops Left=1 The following requests got no response from the ApplianceLinc. No 02 50 inbound messages. The error message is the result of the PLM echoing the command twice. Not an actual device response. Tue 08/21/2012 08:32:43 PM : [iNST-TX-I1 ] 02 62 1D AA D2 0F 12 00 Tue 08/21/2012 08:32:43 PM : [iNST-ACK ] 02 62 1D.AA.D2 0F 12 00 06 LTON-F (00) Tue 08/21/2012 08:32:46 PM : [iNST-TX-I1 ] 02 62 1D AA D2 0F 11 FF Tue 08/21/2012 08:32:46 PM : [iNST-ACK ] 02 62 1D.AA.D2 0F 11 FF 06 LTONRR (FF) Tue 08/21/2012 08:32:46 PM : [iNST-ACK ] 02 62 1D.AA.D2 0F 11 FF 06 LTONRR (FF): Received an ACK for a different device Tue 08/21/2012 08:32:50 PM : [iNST-TX-I1 ] 02 62 1D AA D2 0F 13 00 Tue 08/21/2012 08:32:50 PM : [iNST-ACK ] 02 62 1D.AA.D2 0F 13 00 06 LTOFFRR(00) The FilterLinc did not resolve the communications problem with the ApplianceLinc location. If the Admin Console is not showing a change in State that is initiated at the ApplianceLinc, that is normal. The ApplianceLinc is a Responder only device. It has no Controller function so it cannot communicate local changes in state.
-
Midnight is 12 AM, Noon is 12 PM. The Sunday thru Thur part of the If has the To time before the From time. It should be 12 AM (next day)
-
Does it change the Current State column for the device? An ISY Program issues the same Direct command for device control as the Admin Console. Run Tools | Diagnostics | Event Viewer with Level 3 selected. Run the Program in the way it is normally invoked. Is a command sent to the device? If not does the Last Run Time match when the Program should have run? Was the device renamed at some point? Post the Program
-
SURE, have a Program run the Else clause of the X10 On Program. Running the Else clause sets the Program Status to False.
-
Insteon has no concept of Scene Status (is the Scene On or Off). Nor does the ISY. The devices in each Scene should reflect what was last done to the device(s) regardless of whether done by that Scene, a different Scene or Direct commands. "Is there a way to programattically tell ISY that the Movie scene is no longer On?" ISY has nothing that relates to Scene Status. If you are referring to a KPL button LED being On, for example, and want to turn the KPL button Off, yes there are ways to turn the KPL button Off. Define a Scene with the KPL buttons as a Responder and have the Program turn the Scene Off. This will turn the KPL button LED Off. "Is there a way to programmatically tell ISY that a program is no longer running?" Not sure I understand this question. The Admin Console shows whether a Program is running or not in the Activity column. This is accurate information. It should not show a Program running if it is not. You could have Program A run the Else clause of Program B which will set the Status to False. It will also execute any statements in the Else clause.
-
sys.node custom email substitution isn't working for me
LeeG replied to spaterson76's topic in ISY994
I've looked at the iMeter Solo Sales Page, User Guide, the HouseLinc display, the Extended data returned on the HL Refresh and the ISY Query. I do not see a value that I can attribute to a voltage reading. The iMeter Solo does return a current Wattage, and Accumulated Power but nothing that I can attribute to the other items. HouseLinc is normally pretty good at displaying everything a device has to offer. It is not displaying Voltage or Current. Not an absolute though. Maybe MobiLinc will explain where the information comes from. The ISY is tracking current power and accumulated power only. When I do REST call for the iMeter Solo the only properties returned are the two values displayed by the Admin Console. -
sys.node custom email substitution isn't working for me
LeeG replied to spaterson76's topic in ISY994
That information is not available from iMeter Solo. Therefore not available in variables or REST calls. -
Good point. Thanks. If the second Program had conditions in the If section that complemented those is the first Program the second Program should not be marked Enabled so that the ISY cannot independently trigger the second Program based on any of its If condition. In this example it does not matter as the If in the second Program will be null so the ISY will never independently trigger Program two.
-
If the variable is an Integer the problem is the Zone is no longer violated before the Wait completes. Same situation in that the If conditions have changed before the Wait completes. The solution is to split the logic into two Programs as previously described. As an FYI, both the Wait and Repeat functions allow the If to be reevaluated. A change in the If conditions being checked can prevent statements after the Wait from executing. The UDI Wiki has a good explanation of how Wait and Repeat statements operate. They both allow the If to be reevaluated. Without the Wait (or Repeat) the statements are considered atomic. Without a Wait or Repeat all the statements will execute even should the If conditions change before all the statements are executed. This aspect is also well described in the UDI Wiki.
-
The variable is a State variable. When the Program changes the State variable value and then does the Wait the Program is triggered again because the State variable changed value. Because the variable value is no longer <= 1 the If is evaluated as False so the Else clause is run. The statement(s) after the Wait are never executed. If the Program is meant to trigger only on the Zone violation then the variable should be an Integer rather than State. If the Program is meant to trigger both on a Zone violation and a State variable value change the Program should be split into two Programs. The current Then processing is moved to the second Program which has nothing in the IF section. When the State variable value is changed it will not affect the execution of the statements after the Wait. The first (current) Program invokes the second Program from the Then clause.
-
Try this example If Control 'ICON Dimmer 1' is not switched Off Then Set 'ICON Relay 1' On Else Set 'ICON Relay 1' Off Press the device On paddle/button, the Programs | Summary will show the Last Run Time does not change. With If Control the command received has to match the command specified in the If for the Program to be triggered. Now press the device Off paddle/button. The Last Run Time will be updated and the Status will be False indicating the Else clause ran.
-
Okay. Suggest posting the Program with the type of button activity that result in the loop.
-
I have no opinion either way. It took some energy to create the thermal storage. How much affect will reducing that thermal storage have the next time cold air is called for? It seems that some of the gain in reducing the thermal storage could be lost in replenishing the thermal storage the next cooling cycle. Could it cost more running the compressor and fan to replenish the thermal storage than saved by running the fan to siphon off the thermal storage.
-
The Replace xxxx with ..... function can change KeypadLincs with different firmware so long as they are the same basic configuration (6 button or 8 button). Install the new KeypadLinc under a device Name that will be deleted by the Replace with function. Right click the old KeypadLinc Primary node, select Replace xxxxx with .... A list of candidates that can replace the old KeypadLinc should appear. The old KeypadLinc Insteon address is not referenced so the old KeypadLinc can be removed before running the Replace.
-
If Control triggers the Program only on the specific command defined in the If. The If Control 'xxxx' is not switched Off triggers the Program when an Off command is received. Because of the "not" the If is False and drives the Else clause. Add the Bright command with an additional If statement Or’ed with the If Control …. On If Control 'ICON Dimmer 1' is switched On And Control 'ICON Dimmer 1' is not switched Off Then Set 'ICON Relay 1' On Else Set 'ICON Relay 1' Off
-
Duplicate post. See other post.
-
There is no clean resolution with the MS linked to the SwitchLinc as a Controller. To achieve the control you are looking for requires the MS to trigger a Program which turns On the SwitchLinc. That way the physical turning Off of the SwitchLinc can be added to the Program Conditions that turns On the SwitchLinc from a Motion message and suppress that action. Either accept the slight delay in going through a Program to control the SwitchLinc or accept that the direct linking of the MS to the SwitchLinc to achieve instant On from Motion will result in the SwitchLinc turning back On for a few seconds before an ISY Program can turn them back Off by detecting the Off paddle press and repeating the Off a few seconds later. This assumes the MS will no longer see motion a few seconds later.
-
Run Tools | Diagnostics | Event Viewer with Level 3 selected. Put the TriggerLinc into linking mode with Set button Run New INSTEON Device adding the TriggerLinc. Post the event trace. Make sure the TriggerLinc is in range of a Dual Band device when running New INSTEON Device
-
When the Excel option is not chosen the Log will be stored as a .txt file in the directory you are prompted for.