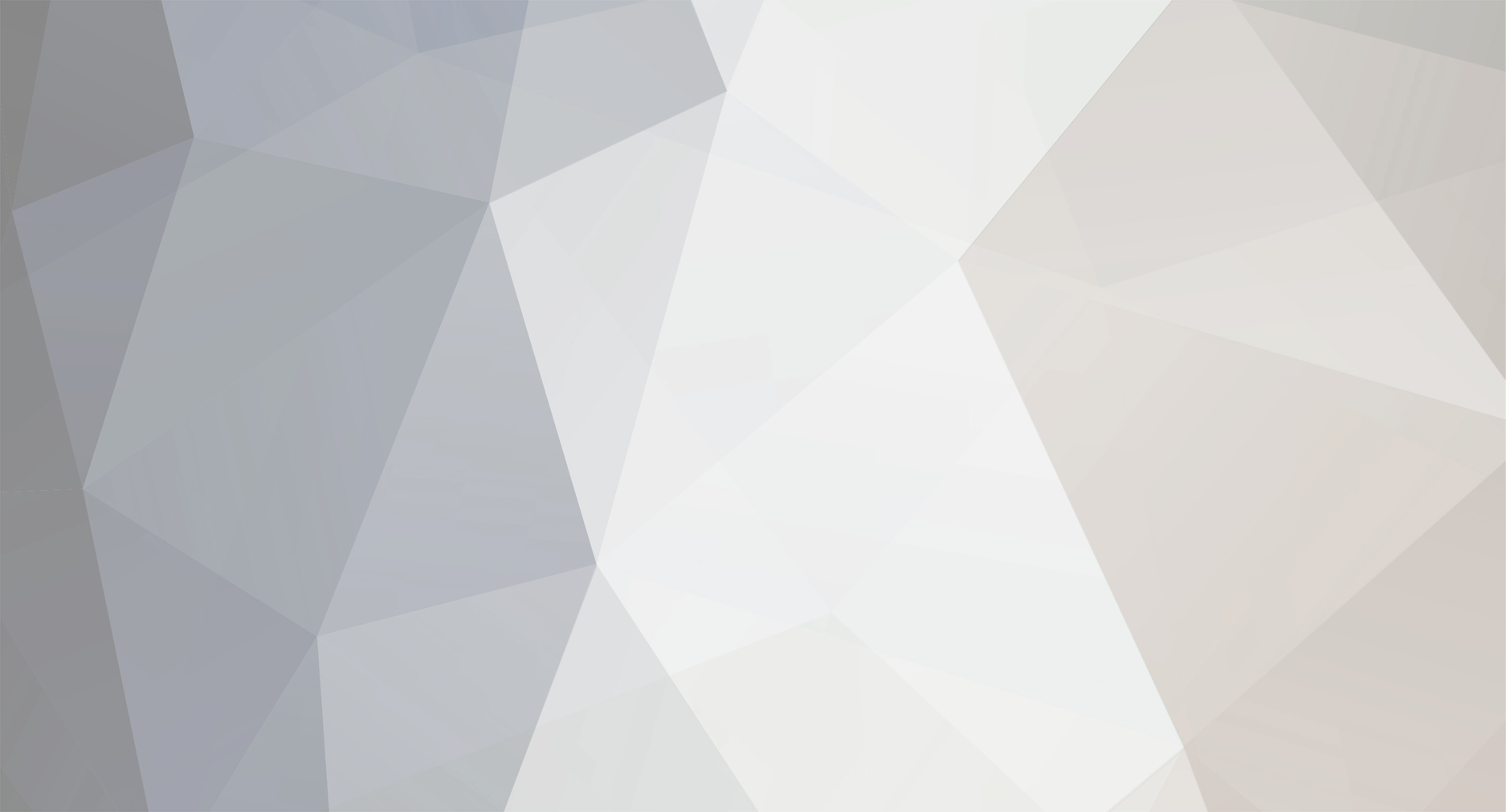
LeeG
Members-
Posts
12943 -
Joined
-
Last visited
Everything posted by LeeG
-
Define a single ISY Scene. Add the two switches as Controllers in the single ISY Scene. This will cross link the two switches such that either switch controls the load and the status LEDs of both switches stay in sync. To operate both devices from the ISY or MobiLinc turn the ISY Scene On/Off. Turning an individual device On/Off has no affect on other devices that may be linked to the individual device. Update: devices should only be linked with the ISY. Linking with the Set button creates links the ISY is not aware of. The links can eventually be deleted or overlaid by ISY activity.
-
There is no option to reduce the LED brightness. UDI responded to this question in the past. See the following link … viewtopic.php?f=27&t=7725&hilit=ISY+LED+brightness
-
Are you referring to adding a device to a Scene as a Controller or Responder? The ISY starts out with the device as a Responder as that is what most devices are in a Scene. It can be toggled to a Controller if not already a Controller in a Scene. A device can be a Controller in only one Scene. If not a Scene question please expand.
-
Number of Repeaters Needed with multiple electric panels
LeeG replied to mjohnson007's topic in ISY994
The PLM is not at a central location electrically and the hardwired SignaLinc coupler is a passive device (not a repeater). I would try a pair of Access Points at the main power panel first. Or move the PLM to the main power panel circuit so the PLM signal has no chance to degrade before being coupled passively to the other 120v leg. I have several power panels and only one pair of Access Points. Although I do not have the sq footage you have. The power panel in the garage some 300’ away has no additional coupling nor does the power panel at the other end of the house which supplies power to that end of the house. Also look at other devices powered from the PLM plug point. Computer equipment, UPS, etc can absorb some of the PLM signal right from the start. A FilterLinc is useful to isolate other devices at the PLM plug point to avoid signal degradation. I'm sure others will have additional ideas. -
I suggest moving to 3.2.6, Delete the InLineLinc w/sense and add it back with Auto Discover under 3.2.6. It is a Relay device and SmartLabs has been updating Relay based devices to I2CS first. You can try a Show Device Links Table for the InLineLinc which will not be correct if it is an I2CS device.
-
Applying EZIO8SA 12V to I1+ and EZIO8SA GND to I1- should turn the Input On. By connecting an removing EZIO8SA GND to/from I1- should cycle Input number one On/Off which is node 9 Note that EZIO8SA Input 5 & 6 (AN1 AN2 should be connected to EZIO8SA GND to insure they do not cycle from electrical noise. Those Inputs have no built-in pullup resister because they can also handle analog input.
-
Delete the KeypadLinc from ISY. Convert to 8 button including setting the KeypadLinc to 8 button mode. The sequence is described in the KeypadLinc user Guide. Add it back to the ISY. The number of nodes will go from 5 to 8 when the KeypadLinc is noted as being an 8 button KeypadLinc. It will be necessary to add the KeypadLinc nodes back to the Scenes and Programs. It is not necessary to delete the Scenes or Programs.
-
The EZIO8SA 12v cannot be used with a pullup resister on Inputs 5 & 6. A 5v power supply can be powered from the 12V to feed +5v through a pullup resister to Inputs 5 & 6.
-
It was Tim that offered that solution. It is what he used with an EZIO6I which also has opto-isolated Inputs. Let us know how it works once actually implemented.
-
Thank you both. Great information. starmanj Connect security panel Com to I1- and the specific Zone connection for the motion sensor to I1+. No connections to the EZIO8SA GND or +12v.
-
TJF1960 Thanks for that data. I believe the opto-isolated Inputs are the same across the EZIOxx line. Is the MS Zone connection a single input and a common ground or two connections specific to the MS Zone?
-
I’ve connected many NO and NC dry contacts to various EZIOxx devices. The issue here is the security panel must be applying a potential to the motion sensor motion wires. Otherwise it cannot detect motion. If the motion sensor was being used standalone (not being shared as a functional motion sensor with the security panel) connection to an EZIOxx Input is pretty standard. The unknown is how to have the motion sensor functional as a motion sensor to both the security panel and an EZIOxx Input at the same time.
-
starmanj Do not connect the EZIO8SA GND and 12V to the -I1/+I1 Inputs if leaving the motion sensor connected to the security panel. The security panel is not expecting an outside power supply to feed into the Zone connections. Try connecting the security panel connections to which the motion sensor is connected to -I1/+I1 as though they are providing an independent voltage to the opto-isolated input. Have no idea what that will do to the operation of the motion sensor function as far as the security panel is concerned. Also do not know if there will be enough voltage swing to operate the EZIO8SA Input.
-
There is no issue with EZIO8SA Inputs being On versus Off. There should be no issue with the resister in the motion sensor and current draw. The opto-isolated inputs are looking for voltage not significant current flow. I assume the resistance allows the security panel to know something is connected by the expected resistance across the motion sensor connection. Something similar to an End Of Line resister on a security zone. I have no experience with security motion sensors. If there is any doubt about the pair of wires being isolated from the DSC power going to the motion sensor that answer will have to come from the motion sensor company. Confirm that the motion sensors are not being used functionally on both the security panel and the EZIO8SA. I have no idea the implications of connecting the motion sensing pair to the security panel and the EZIO8SA.
-
If that approach does not work reverse it. Connect EZIO8SA GND to –I1, connect +I1 to one of the motion sensor wires and EZIO8SA +12V to the other motion sensor wire. That will create a voltage drop across the 90 ohm resister but may work okay since +I1 needs something over +3V to turn the Input On. When motion is sensed the Input turns Off.
-
If the two wires with 90 ohm resistance are truly isolated from the DSC power than the approach is EZIO8SA 12V to the I1+, EZIO8SA GND to one wire on the motion sensor. -I1 to the other motion sensor wire. I do not know if that will work but it will not cause any damage so long as those two motion sensor wires are completely isolated from DSC power. This arrangement was meant for a true dry contact closure with 0 ohms controlling GND to -I1. not through a 90 ohm resistance. If the EZIO8SA Input turns On with -I1 connected to GND through the 90 ohm resistance the Input will turn Off when Motion is sensed. A test will have to be done to see if this works.
-
Getting a false high or low link count is normal if any Insteon traffic reaches the PLM during the Show PLM processing. The PLM maintains an internal NEXT pointer which keeps track of the next link record to retrieve during the Show PLM Get Next command sequence. The NEXT pointer is altered by inbound Insteon traffic reaching the PLM. This causes duplicate link records to be read (false high count) or records skipped (false low count). Regarding all the devices responding, that sounds like an All On or All Off could be issued to the 'My Lighting' Scene.
-
That is a good result if not a strange way to achieve it. All my linking tests have been done without anything connected to the Light or Motor wires. Were either LED on the FanLinc Green during the linking? I do all my linking with both LEDs Red.
-
One more thing to try before the RMA. Use Link Management | Start Linking which will put the PLM into linking mode (PLM LED blinking), then press the Set button on the FanLinc Light for 3-5 seconds. If that does not work and the RMA replacement does the same thing consider moving to a later PLM. Whatever does resolve this please post back the solution so others can benefit. Thanks
-
There were some issues with the v.98 level but nothing related to I2CS that I remember. The v.99 PLM I am running with came out before the influx of I2CS devices. I have done a Set button link between a v.92 PLM and an I2CS FanLinc with no problem. The I2CS devices have not been out long enough to develop a comprehensive symptom/cause list. Some things to consider trying .... Power cycle the PLM Move the FanLinc to an appliance cord and plug it into the same circuit as the PLM Reset the PLM and restore with Restore Modem (PLM) Except that the message exchange between the PLM and the FanLinc did not produce the expected 02 53 response I see no difference between the trace on my system and the posted trace. I Deleted the FanLinc and added it back under 3.2.6 after a FanLinc Factory reset. My trace is identical except I get the expected 02 53 response and the FanLinc adds successfully.
-
Try a factory reset of the FanLinc. It failed to send the expected response to the begin linking command. Note the 02 53 inbound message from my I2CS FanLinc add did not come back in your trace. Fri 03/16/2012 06:55:48 PM : [iNST-TX-I2CS] 02 62 14 9E F5 1F 09 01 00 00 00 00 00 00 00 00 00 00 00 00 00 F6 Fri 03/16/2012 06:55:49 PM : [iNST-ACK ] 02 62 14.9E.F5 1F 09 01 00 00 00 00 00 00 00 00 00 00 00 00 00 F6 06 LNK-ON (01) Fri 03/16/2012 06:55:49 PM : [iNST-SRX ] 02 50 14.9E.F5 19.70.06 2B 09 01 LNK-ON (01) Fri 03/16/2012 06:55:49 PM : [standard-Direct Ack][14.9E.F5-->ISY/PLM Group=0] Max Hops=3, Hops Left=2 Fri 03/16/2012 06:55:49 PM : [LNK-BGN ] 02 64 01 00 06 Fri 03/16/2012 06:55:50 PM : [LNK-STAT ] 02 53 M(01) gid=00 14.9E.F5 012E 41 Also, what type of PLM is being used with the ISY and what PLM firmware?
-
RichTJ99 You have a production version. UDI had a beta device when they implemented support for the 2441TH. They now have a production version which they are evaluating. Not uncommon for a beta device to have some differences.
-
Thanks for the link record display. The User Guide does indicate updates are part of the 2441TH tstat. "Reports changes in thermostat modes, temperature, humidity, setpoints and fan to compatible automation controllers or software" The User Guide (being that it is a User guide) has little about what it takes for the tstat to send those updates. How does it know the device address of the PLM to send the updates to. It does say Group EF is used for broadcasting all changes. Don't know if that is required to get async change messages. The 2441V says the last linked device gets the status updates. The 2441TH makes no such reference. Also think there is a command to Enable/Disable those broadcast updates, although that comes from a 5 year old command reference which may have nothing to do with the 2441TH. I think we have to wait for UDI to evaluate the non-beta 2441TH. My guess is the function is there on the production versions.
-
andyf0 If you have the capability to add link records outside of the ISY (not a good practice) add Controller link records for Group 1,2,3,4 (ISY may have added a Controller link for Group 1). According to the 2441TH User Guide these additional Groups are used for sending indications for heat/cool/humidify/dehumidify, etc. It will take additional nodes the other tstats have for these to be functional under the ISY but Insteon messages should flow once the tstat knows what device to send the messages to.