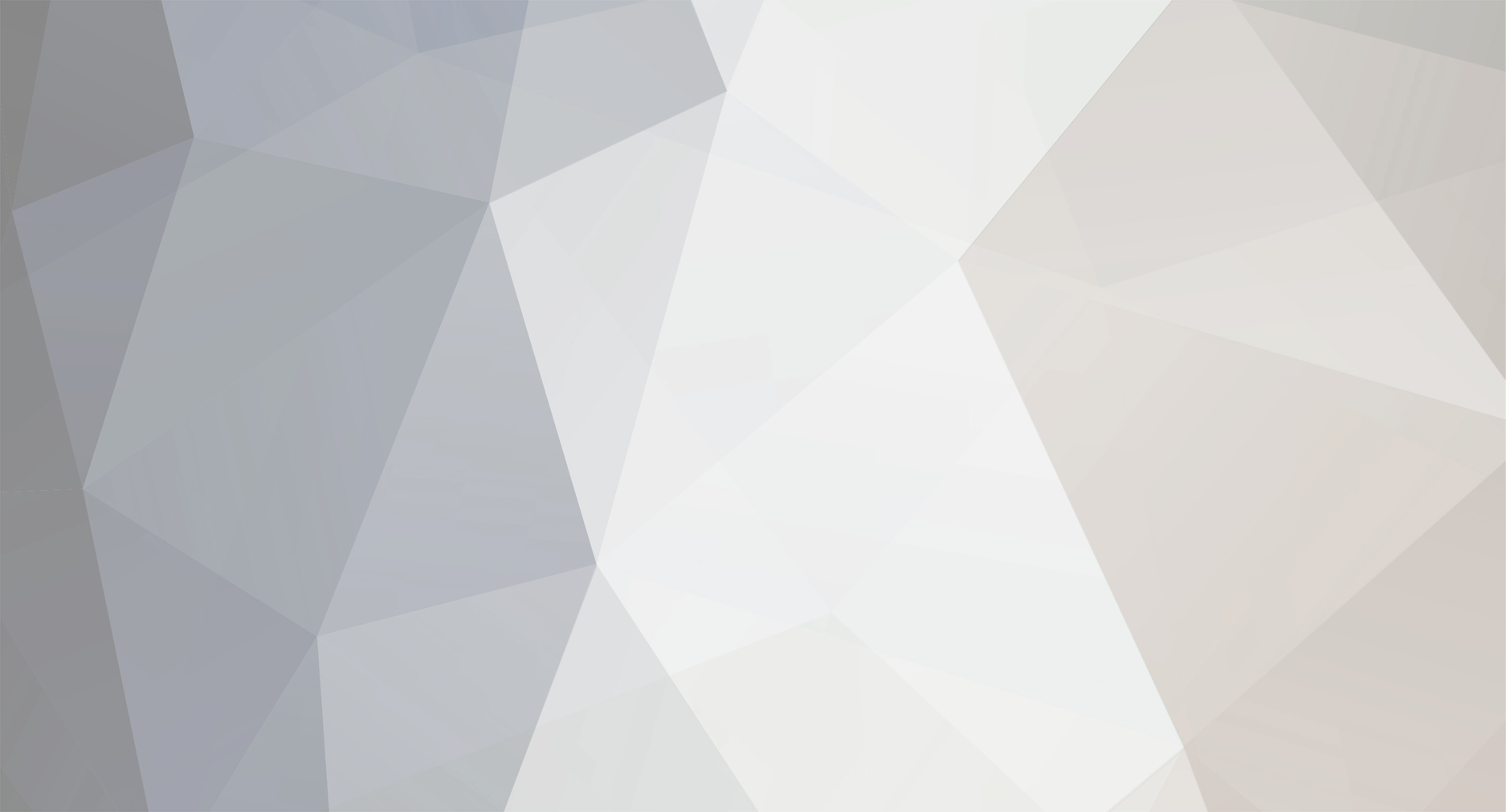
LeeG
Members-
Posts
12943 -
Joined
-
Last visited
Everything posted by LeeG
-
Were any games played with neutrals associated with any of the switches or loads. Like sharing neutrals from other circuits, using the green wire ground for neutral, stuff like that. The GFI is tripping because the current flowing on the line and neutral do not match or something is flowing on the green wire ground.
-
If Control is monitoring the commands coming from the Motion Sensor. An If Control xxxxx On triggers the Program anytime a Motion On message is received. If the next Motion On is received before the Wait completes the Program starts over from the beginning of the Then clause without executing the statements after the Wait. Only when no Motion On messages are received for the full Wait duration will the Wait complete and execute the statements after the Wait. Status is what the ISY considers the current state of the device. "If Status" triggers a Program only when Status changes, from Off to On or On to Off for example. When Status changes and the Program is triggered, the Then or Else clause runs depending on the True/False evaluation of the If statements. In a scenario where all motion needs to be detected (no Timeout delay) the Motion Sensor very often sends Motion On followed by Motion On followed by Motion On. Since the Status changes from Off to On only for the first Motion On message, the Program is not triggered for subsequent Motion On messages. Normally when running Occupancy mode the On Only mode is also used so Off commands are never sent. The UDI Wiki has a good description of If Control versus If Status and the effect Wait/Repeat statements have on Program execution.
-
If Status cannot be used for this scenario. If Status triggers a Program only when Status changes. The Motion Sensor is sending On command followed by On command which is not a "change" in Status. Use If Control to trigger on each Motion On message.
-
Run Tools | Diagnostics | Event Viewer with Level 3 selected. Run New INSTEON Device with Auto Discover and post the event trace.
-
Which option is in effect, erase existing links or keep existing links? Check Help | About to be sure both Firmware and UI lines indicate 3.2.6.
-
Not a Program issue. The Motion Sensor will not send another Motion On until the Timeout delay has expired. The exception is to put the Motion Sensor into Occupancy mode where it sends an On command for every motion detected. For the ISY Occupancy mode is set using the Sensing Mode option check box under Set Options.
-
Try New INSTEON Device with Auto Discover. I think the lack of a v.xx number when selecting a Device Type may make it think this is a V1 adaptor (not sure about that). Something Michel posted a few days ago makes me think that but I could not find the post to be sure.
-
This is an I2CS device. Is the ISY at 3.2.6? Does Help | About show 3.2.6 for Firmware and UI? Was Device Type set to Auto Discover when using New INSTEON Device? Was the tstat Off?
-
Note the timestamp on the last 02 62 outbound message and the ERR 1 message. This is the ISY timing out after not getting a response from the On command. Fri 05/25/2012 08:23:37 AM : [iNST-TX-I1 ] 02 62 1C C2 15 0F 11 FF Fri 05/25/2012 08:23:37 AM : [iNST-ACK ] 02 62 1C.C2.15 0F 11 FF 06 LTONRR (FF) Fri 05/25/2012 08:23:41 AM : [ 1C C2 15 1] ERR 1 There is likely a red ! to the left of the device node when this happens. Right click the node and select Query for the ISY to attempt to communicate with the device again. When the ISY is able to Query the device the red ! will go away and commands should work until the powerline issue comes back. If the powerline issue remains the Query will fail and the ISY will hold communcations until the condition is cleared and the next Query works. Otherwise the ISY would continue to be held up waiting for responses to come back.
-
I went back over this topic from the beginning. There is one aspect that does not fit into this being a device problem. To confirm, when you click the On button in the Admin Console the Admin Console does not show the device turning On but MobiLinc does show the device as turning On when the On button in the Admin Console is clicked? Also confirm that other devices do show correct state change when their respective On/Off buttons are clicked in the Admin Console.
-
I am not familiar with that companies policies on replacements but I would assume so.
-
You could try factory resetting the SwitchLinc Dimmer followed by a Restore Device to rebuild the link database.
-
Thanks for the trace data. That is the expected command for updating the SwitchLinc Dimmer Local Ramp Rate. Unless using a Scene to turn the SwitchLinc On/Off which would involve a different Ramp Rate setting, I have to conclude the SwitchLinc is not working correctly. That command sequence correctly sets my SwitchLinc Dimmer Local Ramp Rate with firmware v.38
-
Run Tools | Diagnostics | Event Viewer with Level 3 selected. Set the Ramp Rate to something fast such as 0.2. Post the event trace. What is the ISY firmware level?
-
Unless the switch is malfunctioning I suspect there is something else that is interfering with communication. When it worked the Hops Left counts were indicating good communication between the switch and the PLM. The second small trace (duplicate of first small trace) indicates nothing from the switch. Some other lighting or appliance is cycling On and Off. When On it is blocking communication. When Off Hops Left are good indicating clean communication. Could be a coupling issue. If a 240v appliance is cycling On and Off it could be coupling when On and lose coupling when Off.
-
Disconnect and cap the red load wire. New INSTEON Device can also be tried. Enter the Insteon address, Name, leaving the Device Type set to Auto Discover. Have the Event Viewer active as before so the command responses can be analyzed if it does not work. The message resulting from the Set button press reached the PLM. The commands sent from the PLM got no response. Impossible to tell from the trace if the commands failed to reach the device or the responses failed to come back. After the single Set button message was received (0253) there were no other 025X (inbound) messages from the device.
-
That indicates the dimmer has been set with a long ramp rate. The Fast xxx commands ignore the ramp rate setting in the dimmer.
-
The Start Linking process generates the referenced message. The PLM is coming out of linking mode. It is not indicating an actual error. The problem is device 1C BF 16 failed to respond to the Insteon commands issued by the ISY. It issued the command three times, failed to get any response from the device. Something is interfering with communication between the device and the ISY PLM.
-
An issue with Anti Virus (Kaspersky, Avast, two examples) or firewall can block updates from the ISY to the Admin Console but it would affect all devices, not a single device. Check to see if other devices have the same issue.
-
The link records would not have been written correctly if not added under 3.2.6. After adding under 3.2.6, If the Scene Test continues to fail with the device plugged into the same outlet as the working LampLinc, please run Tools | Diagnostics | Event Viewer with Level 3 selected. Once added under 3.2.6 and the Scene created under 3.2.6 the LampLincs in the Scene would be expected to pass the Scene Test.
-
Were the devices that do not work added to the ISY under 3.2.6?
-
ertyu Move the LampLinc that does not respond to the same plug point as the LampLinc that does work. It could be a phase coupling problem or it could be one the LampLinc that does not work is a new I2CS device which requires 3.2.6. If it works plugged into the plug point of the working LampLinc then there is a coupling or noise problem on the original circuit. If it does not work at the alternate plug point it could be an I2CS device.
-
The Program looks okay. When a device will turn On but not turn Off the next thing to consider is the interference the load is causing. What does the chlorinator consist of? Could try a different load, such as a simple light bulb and see if it turns Off okay. It may be necessary to isolated the chlorinator with a FilterLinc.
-
Post the Program. Right click on Program name and select Copy to Clipboard. Then paste into post. A common problem is not to put Next Day on the To time so the To time is before the From Time and never triggers.
-
If you are using a single KeypadLinc and will limit fan control to a single KeypadLinc in the future there is an easier method. SceneFanOff KeypadLinc A – Controller (I made the A button Off – could use any of the Secondary buttons) KeypadLinc B – Responder (On Level slider set to 0%) KeypadLinc C – Responder ( On Level slider set to 0%) KeypadLinc D – Responder (On Level slider set to 0%) FanLinc Fan – On Level = Off SceneFanLow KeypadLinc B – Controller (I made the B button Low – could use any of the Secondary buttons) KeypadLinc A – Responder (On Level slider set to 0%) KeypadLinc C – Responder ( On Level slider set to 0%) KeypadLinc D – Responder (On Level slider set to 0%) FanLinc Fan – On Level = Low SceneFanMed KeypadLinc C – Controller (I made the C button Med – could use any of the Secondary buttons) KeypadLinc A – Responder (On Level slider set to 0%) KeypadLinc B – Responder ( On Level slider set to 0%) KeypadLinc D – Responder (On Level slider set to 0%) FanLinc Fan – On Level = Med SceneFanHigh KeypadLinc D – Controller (I made the D button Low – could use any of the Secondary buttons) KeypadLinc A – Responder (On Level slider set to 0%) KeypadLinc B – Responder ( On Level slider set to 0%) KeypadLinc C – Responder (On Leveol slider set to 0%) FanLinc Fan – On Level = High No ISY Programs or special Scenes for button LED control are needed If multiple KeypadLincs are/will be used then ISY Programs and Scenes are needed. The Scenes used for button LED control do not have the FanLinc Fan as a Responder to prevent the Fan from being turned Off.