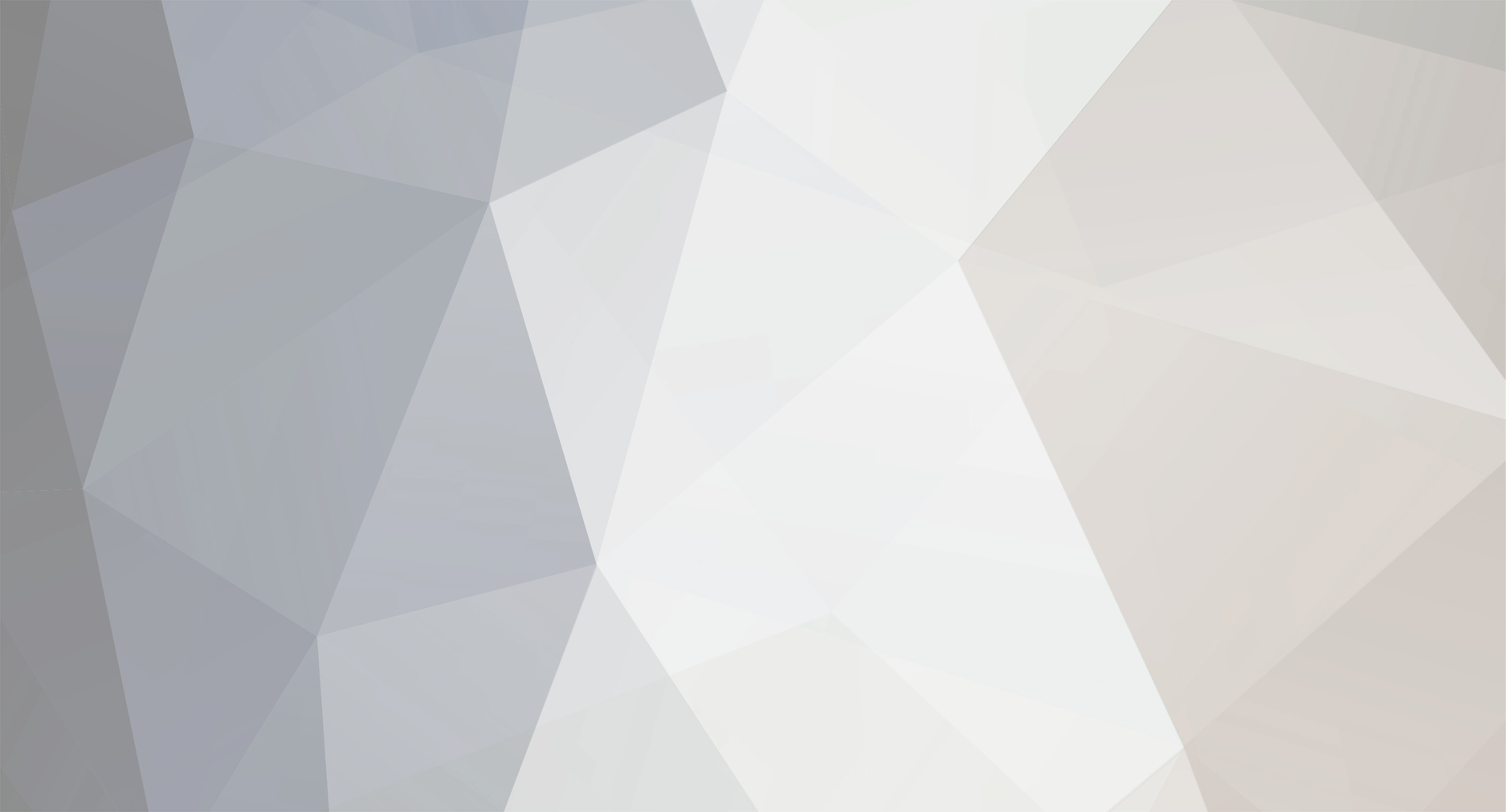
LeeG
Members-
Posts
12943 -
Joined
-
Last visited
Everything posted by LeeG
-
The KPL A button should not be controlling power going to the FanLinc. The Red KPL load wire should be capped. That should have the A button and G button work the same.
-
The Hidden Door Sensor could not be added to the ISY before. That was the point of moving it to the PLM location. Why undo that, delete it from the ISY and try adding it from the garage where it has never worked. I do not understand why it was deleted before moving it back to the garage.
-
The "remove all links" is an option when adding the Hidden Door Sensor to the ISY. No such option when adding the Togglelinc and Hidden Door Sensor to an ISY Scene. Run Tools | Diagnostics | Event Viewer at LEVEL 3. Put the Hidden Door Sensor into linking mode. Add it and one of the switches to an ISY Scene and post the event trace.
-
Linking any RF only device to the PLM, the PLM has no information about what devices the messages went through to get to/from the PLM. Once linked if there are comm issues where the Hidden Door Sensor is moved to it has to do with the environment in the new location. Insteon messages carry no information as to the devices the messages flow through. If the Hidden Door Sensor was linked to a Responder (not just a device that moved the messages) that link remains even if the Sensor is moved. If any comm to the PLM occurs use Tools | Diagnostics | Event Viewer at LEVEL 3 to check the Hops Left count to see how good comm actually is.
-
PLM initiated Scenes are not ACKed so the ISY is marking the Responders as they should react, not knowing how they actually reacted.
-
If the Scene On never works check the Scene responders On Level to be sure not set to 0% On Level.
-
If the first thing is a simple Scene On and that does not turn On the Responders comm is the issue.
-
The HTTP errors should not affect this Program, the Insteon network over the powerline and the IP network are very different. I am not familiar enough to help with the IP side except that some of the HTTP contact involves an application that is using REST commands to work with variables. As far as the motion sensor perhaps having it operate in On only mode and have it use a Scene to turn On the load directly and use the Program to flash the load and turn the load Off
-
Agree with other posts about good comm with Hops Left=2. The trace indicates some Adjust Scene activity is being issued. Device 27.91.81 turns On immediately followed by an Adjust Scene to 24 0A BB. That Scene is then turned On, followed by a repeat of Adjust Scene to 24 0A BB because the update interrupted by the Scene On. This started at 18:04:22. Device 27.91.81 turned On at 18:45:00 with 24.0A.BB turning On with what looks like the result of being linked to 27.91.81. Not sure about the activity to 24.0A.BB. Device 27.91.81 turns On and Off without additional Scene activity. There is additional activity from 27.91.81 turning On with a Scene Off some 10 seconds later. It appears that information as to 27.91.81 and 24.0A.BB is needed along with what Scene activity is being done. Suggest posting the Program(s) involved and the device addresses of the devices involved as there is more going on then a simple motion On.
-
A similar problem was seen by another user. The problem was the result of the motion sensor sending the remainder of the motion On Scene messages at the same time the Program was issuing the Set Scene. Insteon terminates one Scene when two Scenes are running at the same time. The solution was to add a Wait 1 second before the Set Scene statement. The other user Program had been running successfully. It appears that Program execution is running faster allowing a Scene overlap that did not exist before.
-
"How can I count the hops in the log? " Max Hops is the maximum allowed. Hops Left shows how many hops taken. It always takes 1 so Hops Left=2 is best. The event viewer should be run at LEVEL 3. Tue 09/30/2014 04:24:29 PM : [std-Group ] 28.40.E7-->Group=1, Max Hops=3, Hops Left=1
-
Right click on node, select Query to clear Red !. Then select Restore Device. If battery devices each has to be put into linking mode, select Query followed by Restore Device. When that update is complete take that device out of linking mode and put the next battery device into linking mode and repeat Query and Restore Device.
-
At 7:30 PM the On Level and Ramp Rate are changed to 25% and 8.5 seconds. Pressing the KPL button On after 7:30 PM should result in 25% On Level. At 10:30 PM the On Level is changed to 100%. Pressing the KPL button On after 10:30 PM should produce 100% On Level. Would be good to post the Scene definition so that the names in the Program can be checked against the KPL Responders.
-
Thank you Xathros, that is the why the update required Icon is/was Gray.
-
I was able to create a Gray 1011 Icon marking Update required for the Hidden Door Sensor. Don't know why this Icon is Gray and the other 1011 Icons are green. Perhaps UDI can comment about the color of the icon
-
Glad to hear things are operating now. You may have comm problems when the Hidden Door Sensor is moved back to its original location but the device itself is shown to be working.
-
Here is a picture of two Hidden Door Sensors. Can you relate which Icons are Gray on your system. Even better can you post a picture of the icons.
-
builderb The Red ! and the Green 1011 Icon mean different things. The Red ! indicates a command sent to the device did not get a response. The normal way to clear that is issue a Query. The Green 1011 Icon means pending updates which is cleared by a Write Updates to Device. If a battery device it must be in linking mode for both the Query and Write Updates.
-
The Green 1011 Icon indicates updates are pending for that device. For a 120v device right click on the node and select Write Updates to Device. For a battery powered device it must be put into linking mode with its Set button before clicking on Write Updates to Device.
-
PurdueGuy will find the problem. Note that the screen captures are not looking at the right information. The ISY Scene name was select which affects when the Scene name is used in a Program. Click on the Red KPL button to see the responder On Level and Ramp Rate that are used when the KPL button is pressed. These are NOT the values displayed when the Scene name is selected.
-
I am not familiar with "Link Management > New Insteon/A10/X10 Device". I suggest using New INSTEON Device. Enter Insteon address, Name of choice and Auto Discover. Use the default "Remove existing links" What level of ISY are you using that has "Link Management > New Insteon/A10/X10 Device"?
-
Factory Reset the Leak Sensor, right click on -Dry node and select Restore Device to rebuild device. If that does not work then Delete the device and add it back to the ISY. Without any traffic from the Leak Sensor unless the Factory Reset restores function, the device may not respond to the Restore Device.
-
I would move the Leak Sensor near the PLM (if a 2413) and repeat the Set button tap test. At this point the Leak Sensor is either not sending any Wet/Dry message or is not in range of a Dual Band device.
-
dba62 Run Tools | Diagnostics | Event Viewer at LEVEL 3. Tap the Set button on a Leak Sensor. Either a Wet=On or Dry=On message should be traced followed approx 15 seconds later by a Heartbeat message. Post the event trace after waiting at least 30 seconds for Heartbeat.
-
After running my test Program this morning when the temp and humidity values changed overnight, I realized the D2D Event message is displayed on the Program Query when the value is different from the last value. The temp dropped from 27 C to 24 C and I received the D2D Event message. The second time I ran the Program Query I do not get the D2D Event message because the temp is still 24 C. The Admin Console Query displays the D2D Event messages even when the values have not changed.