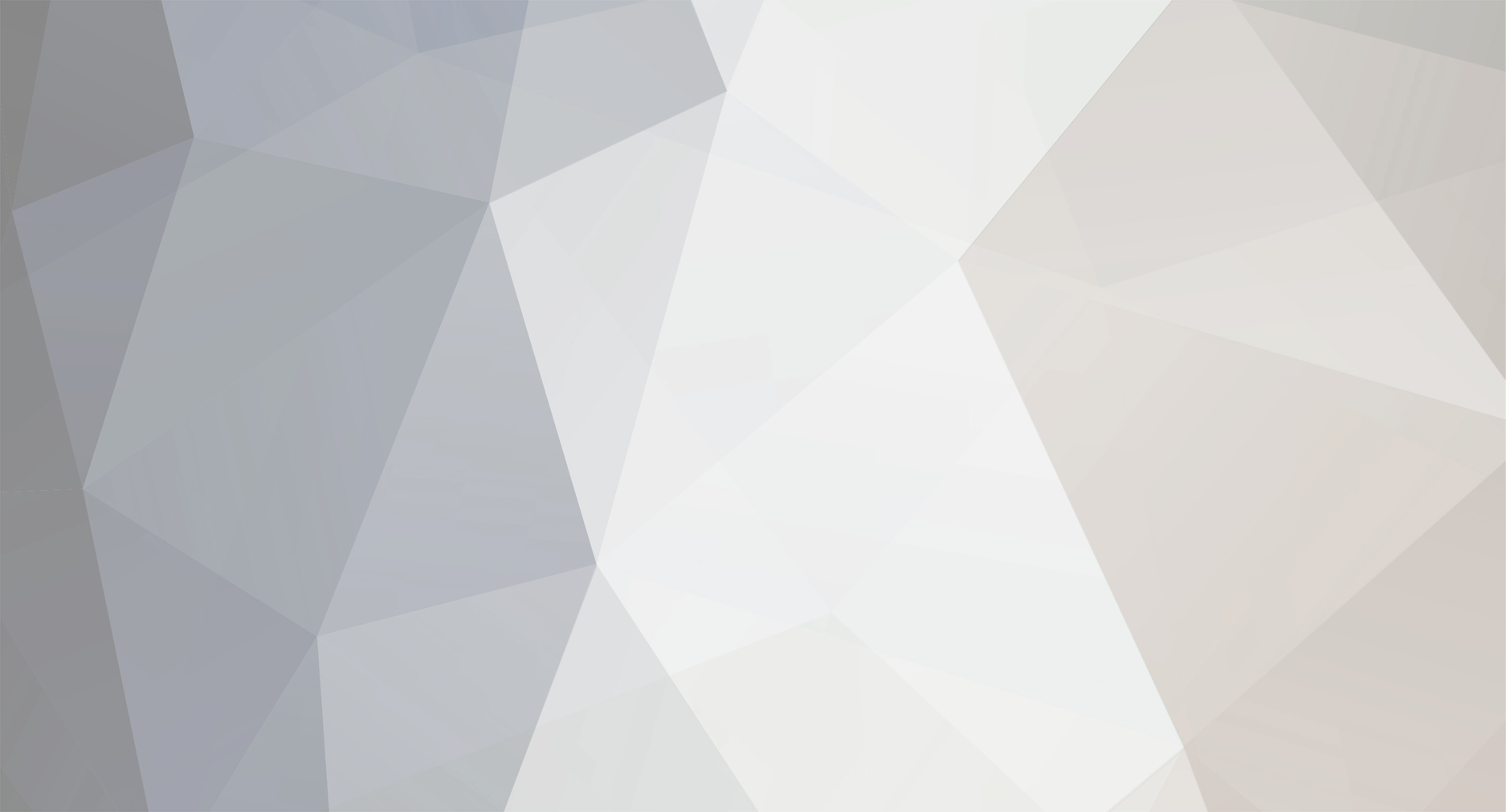
LeeG
Members-
Posts
12943 -
Joined
-
Last visited
Everything posted by LeeG
-
This message (and there are several) with Hops Left=0 indicates comm. with 21 43 23 is operating at the very extreme of reliability. Sat 12/08/2012 12:11:40 PM : [standard-Direct Ack][21.43.23-->ISY/PLM Group=0] Max Hops=3, Hops Left=0
-
The Low Batt Off does not come from the Motion Sensor. The ISY primes that node with Off because the Motion Sensor does not send Off for the Low Batt node. It did not sound like a TriggerLinc issue initially but replacements had already been RMAed. With old and new TriggerLincs and Motion Sensor not working there is an RF issue or powerline issue or perhaps a phase coupling issue. There is no difference in Set button linking and ISY created link records. Manual Set button linking creates issues because the ISY is not aware of the link records. They will eventually be overlaid or deleted with half/broken links the result. With the Access Point reacting to the TriggerLinc either a powerline issue is not allowing the signal to get back to the PLM or perhaps coupling is not working in that area.
-
I have wireless door bell buttons on front and rear doors. Contractor forgot to include conventional door bell 20 years ago. Have been using a simple wireless system from Lowes for nearly that long. One battery powered chime with buttons that have jumpers similar to those in the Motion Sensor. Different chime for front and rear door. No Insteon connection. Chime batteries are D cells which last for many years. Button batteries are outside so they are only good for a year or so. Actually have a chime module on the first floor as well as the basement level using the same buttons. The advantage is obviously no wires to pull in outside walls where insulation might be disturbed. Down side is batteries in the buttons need replacing. I've gotten in the habit of replacing my Dakota Alert transmitter batteries and door bell button batteries around the start of winter. Insures batteries are fresh during the cold weather. Personally I would prefer conventional door bell buttons to eliminate the batteries but the alternative of fishing wires in two outside walls two interior walls made the battery approach attractive and it has worked for a very long time.
-
Check the Green LED on the I/O Linc at the wire connections. It is On when the Sensor is On. If the Green LED is Off when the door is closed the problem is related to the magnetic switch, how close together, wiring, etc. If the Green LED is On and the Admin Console shows the Sensor as Off (assuming Trigger Reverse is not being used) there is a comm problem between the I/O Linc and the PLM. Run the Event Viewer at LEVEL 3, controlling the I/O Linc Relay from the Admin Console. Look at the Hops Left=x counts. Are the counts consistent across may Relay operations? Is it Max Hops=3, Hops Left=0 which is at the edge of reliability. Hops Left=2 is preferred, Hops Left=1 is okay if the number is consistent. If Hops Left count moves around between 2/1/0 it indicates a comm problem.
-
There are Export/Import functions but I don't think they are what you would be looking for. Export a Program to see the format. There is nothing that supports Pasting as Programs are not stored in the Copy to Clipboard format.
-
Now... My previous test results are still the same. 'Hallway has 2 problems when using the node in the ISY 2)The lights do NOT turn on at all... even the though the led moves up and down Please confirm that ‘Hallway’ is the SwitchLinc with the Red wire connected to the lights. ------------------------------------------------------------------------------------------------------------------ "2)but... the lights still do NOT come on when turning on the light from the node in ISY" Turning the 'Hallway main' On/Off (this is the switch with the Red wire capped) will not turn the actual light On. Using Insteon Direct commands affect that specific device only. Since nothing is connected to the Red wire nothing is physically being controlled. Turning 'Hallway' On/Off (the switch with the Red wire connected to the load) with Insteon Direct commands must turn the light On and Off.
-
How many nodes depends on which thermostat. A 2441TH has two additional Red Controller nodes, Heat and Cool. The Venstar thermostats have 3 Red Controller nodes, Heat, Cool and Fan. The Red Controller nodes can be Controllers of an ISY Scene. They can be used to trigger ISY Programs.
-
If the sm120x relay is to control an InLineLinc the sm120x relay is switching 120v AC to the InLineLinc Yellow Sense line. When 120V AC is applied to the Yellow Sense line the InLineLinc turns On. When 120V AC is removed from the Yellow Sense wire the InLineLinc turns Off.
-
I suggest updating to 3.3.5 RC2. The 3 Red nodes are Controller nodes associated with the thermostat. The can be used to control scenes related to the respective activity. The thermostat nodes can be grouped together my doing a right click on the main node and select Group Devices. Once on the latest ISY firmware Delete the other thermostat (single node) and add it back. It will have more than one node. How many nodes depends on the type of thermostat. The only exception would be if the other thermostat is a very old V1 which only supported one node.
-
What ISY firmware level? Right click bathroom switch node, select Diagnostics | Query Insteon Engine. Now set On Level (applied locally) slider to the desired value. If already set at value move it so the ISY sends a different On Level (applied locally) value. Then set it back to the value you want.
-
In addition to the above changes right click on one of the SwitchLinc nodes in the My Lighting tree, select Diagnostics | Query Insteon Engine. Repeat for the other SwitchLinc. Right click on the Program name and select Run Else which will set everything to 100%. After Progress bars complete, right click Program name and select Run Then. This will set everything to 25%. Easy way to test without waiting for or changing If section. Note the results of each test as you did before, looking at both SwitchLinc Status LEDs for each test.
-
Add this to the Then (in addition to the In Scene ‘Hallway’ Set Hallway’ 25% (On Level) which is already there) In Scene ‘Hallway main’ Set Hallway main’ 25% (On Level) and to the Else In Scene ‘Hallway main’ Set Hallway main’ 100% (On Level) That should take care of the situation where the slave SwitchLinc is being pressed and its LEDs go to 100% and the primary SwitchLinc turns the load On to 25%. Still have to find out why when the 'Hallway' paddle is pressed the LEDs go to 100% even though the load actually goes to 25%.
-
The last three Else statements should be 100% On Level Else In Scene ‘After Hours Hallway’ Set ‘Hallway main’ 100% (On Level) In Scene ‘After Hours Hallway’ Set ‘Hallway’ 100% (On Level) In Scene ‘Hallway’ Set ‘Hallway main’ 25% (On Level) In Scene ‘Hallway main’ Set ‘Hallway’ 25% (On Level) In Scene ‘Hallway’ Set Hallway’ 25% (On Level) Something is not as expected/described when the Status LEDS go to 100% but the load is actually 25%. That is all under control of the switch which should be impossible. It is almost like the names are reversed. Use the Admin Console to turn 'Hallway main' node (not Scene) On when in the 25% On Level time frame. What happens to the Status LEDs and what happens to the actual load. The load should not turn On if 'Hallway' Red wire is connected to the load.
-
I agree with the possibility the slider was sitting on something like 1% which would make the load look like it was physically Off and the button LED On because it is On until 0% On or Off with an Off command. The key here is that every Controller of a Scene has a unique set of Responder values for On Level and Ramp Rate. One of the powerful capabilities of Insteon. This aspect of Insteon is not always understood or appreciated for the flexibility it provides. As an FYI if you right click on the slider it displays the value without changing it. Glad to hear things are working.
-
If the KeypadLinc load control button LED is On and the load being controlled is Off there is an issue with the KPL. Because the responder on level values that were posted have nothing to do with what happens when the Secondary KPL button is pressed (making it the Controller) I am assuming Main A is not set to 0% On Level when the Secondary KPL button is acting as Controller. Or perhaps the wrong Insteon Engine information is stored for the KPL resulting in an incorrect configuration. We need to know what the responder values are when the Red Secondary KPL button below the Scene name is selected. Those responder values are independent of the responder values that were posted which apply to when the ISY Scene name is being used. Tim I don't think the OP has described what happens when the ISY Scene name is used. The information thus far has been what happens when the KPL Secondary button is pressed. The mechanism the KPL uses to control Main A when being controlled from a separate Controller (PLM when using Scene name) is very different from when the Controller is a Secondary button on the same KPL. When controlled by the PLM the link record information is controlling. When controlled from a Secondary KPL button in the same KPL, link records are not used. Rather internal configuration information is controlling. Also not all firmware levels of KPL supported turning the load control button Off from a Secondary KPL button.
-
Hi Folks We talk about Group Devices as though this is some new and wonderful addition to the ISY. This is from the ISY User Guide that I downloaded back in 2010. "Group Devices. Some INSTEON devices will create multiple entries within the ISY. For example, KeypadLincs have 6 or 8 nodes in the ISY (one for each button). You can choose to group these nodes together by right-clicking the primary node and choosing “Group Devicesâ€." As much as some products do not document much of their product, folks might be amazed at how much can be learned about the ISY by just reading the User Guide.
-
Right click the KPL Primary node in the My Lighting tree, select Group Devices. That will put a +/- sign to the left of the Primary node with the Secondary nodes indented below.
-
johnstewart The posted image has the Scene name selected with the Responder values when the Scene name is used. Click on the Red KeypadLinc button node name below the Scene name. The Responder values now displayed are those in effect when the Secondary KPL button is pressed. Set the Responder values for when the Secondary KPL button is Controller. If the KPL load does not respond according to the that Responder On Level (assuming it is set to 0% On Level), right click the KPL primary node in the My Llighting tree, select Diagnostics | Query Insteon Engine. Then change the Scene button A Responder On level away from 0% On Level. After the update is complete move the slider back to 0% On Level. If that does not produce the desired result what is the KPL firmware level? Also what ISY firmware is being usedf?
-
Release 3.3.5 (RC2) is now available. The issue being discussed before was not being able to configure the I/O Linc options. What type of Scene creation problem are you having? Manual Set button linking is not a good approach. The ISY does not know about those links and will eventually overlay or delete them. Also now that you are on 3.3.4 (RC1) do a right click on the I/O Linc Sensor node, select Diagnostics | Query Insteon Engine. This will insure the ISY has the correct information about the I/O Linc.
-
Thanks. I corrected the previous post. I guess a new statement could be architected, 'Adjust Device' which would support adjusting the Local On Level and Local Ramp Rate. UDI chose to include that function in the Adjust Scene statement which has the 'Scene' premise.
-
The Adjust Scene statement works on Scenes and devices associated with Scenes. If the node is not in a Scene the Adjust Scene statement does not list it as a selectable item.
-
The LED Bulb should not misbehave but of course it can respond to Insteon commands when power is Off. Best approach is to replace the mechanical switch with an Insteon switch. The wires to the LED Bulb are retasked to provide unswitched power to the LED Bulb and the Insteon switch linked to the LED Bulb for bulb control (Red wire capped on Insteon switch).
-
Define an ISY Scene and add the SwitchLinc as a Controller in the Scene. When that is done the SwitchLinc node name will appear as a selectable item in both the Adjust Scene 'In Scene' and 'Set' parameters. When using the SwitchLinc node name in both parameters the ISY knows to change the Local On Level so the light turns On to 30% when the paddle is pressed On.