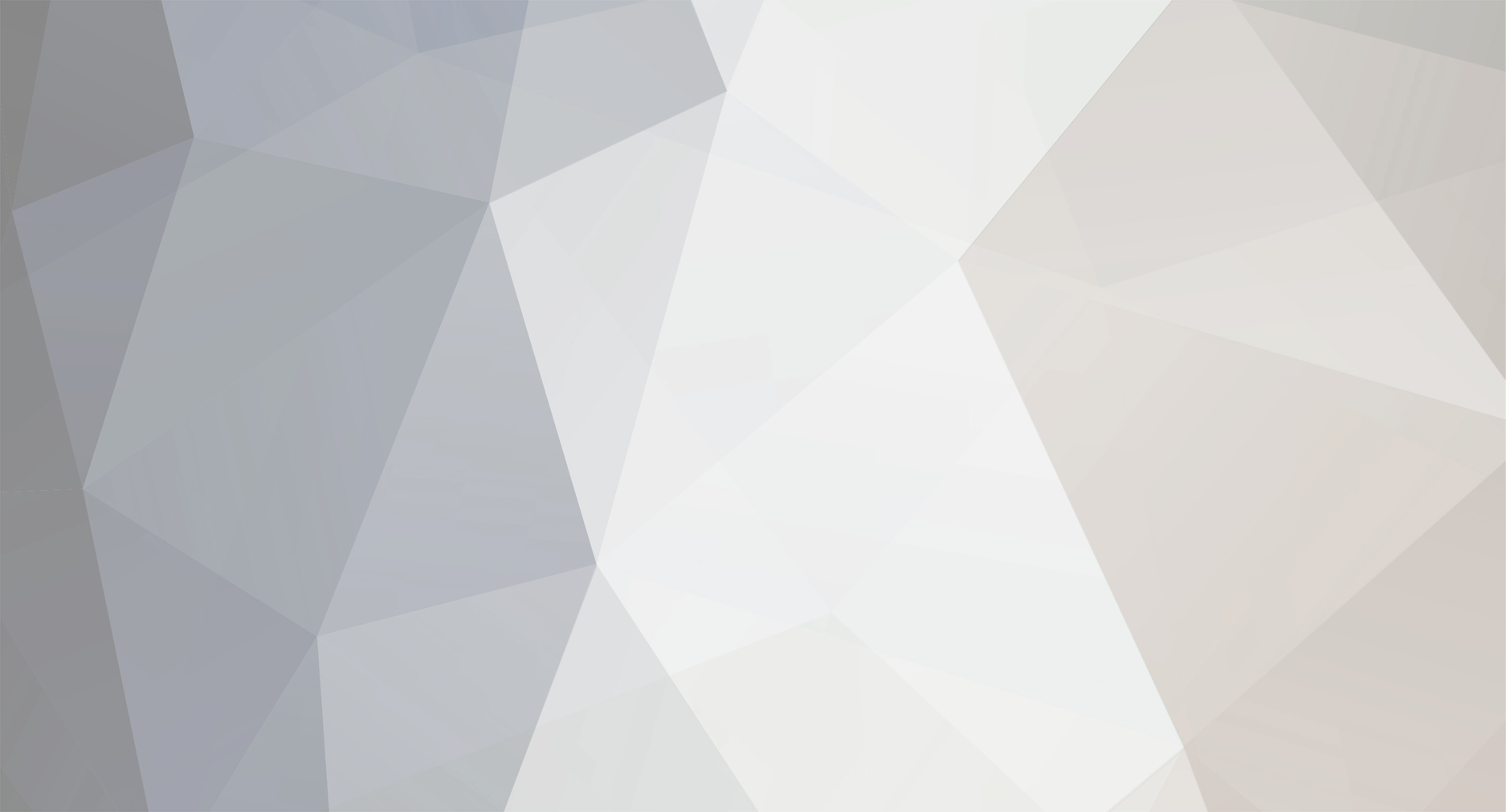
LeeG
Members-
Posts
12943 -
Joined
-
Last visited
Everything posted by LeeG
-
Glad to hear the devices are defined. Unfortunately since the RF issue was not identified it will likely appear again.
-
The ISY is updating something, not the LED Brightness, with the command traced. With the popup still displayed the ISY has not completed whatever updates it thinks it needs with that KPL. I am concerned the movement back and forth between 3.2.6 and 3.3.x may have done something to that KPL definition. The 3.3.x images made changes to the ISY configuration that were not backward compatible with 3.2.6. It may be necessary to Delete that KPL device and add it back from scratch.
-
Run the Event Viewer at LEVEL 3. Click the Clear button on the event viewer and then change the KPL LED Brightness with the Admin Console. Post the event trace and I will analyze.
-
foxcob Using I1 for link management and I2 for device configuration is normal. ISY uses I2 (or I2CS) for link management only for those devices that cannot support I1 (motion sensor, triggerlinc, and others). The values posted for the different LED Brightness values are not valid for the KPL but I don't think that is the issue. The KPL hardware/firmware requires a minimum separation of the low/high numbers by 8. For example 7/15 or 1/9. The device enforces this to maintain a consistent visual difference in LED level between Off and On even though the KPL accepts other combinations of numbers. I do not see the command to change LED Brightness level but it could be under the progress popup or off the screen altogether. There are also several other commands being issued. Was this LED Brightness test/change done with the Admin Console LED Brightness button?
-
I can't think of anything to test. RF is not under control of the application (ISY in this case). RF should be automatic when the Dual Band devices have power. If the PLM is a 2413 try placing the RL2 or Motion Sensor a few feet from the PLM which would eliminate the other aspects of the Insteon network. Not that it matters to RF but HouseLinc will not run with a standard 2413 PLM. It has to be a 2413SH or 2413UH. Also note that the Group 1 message sequence from the devices is not complete and there is no outbound traffic to the devices. For HL PLM to accept these messages there must be a link in the PLM for the device addresses. That PLM should not be powered while trying to link those devices to the ISY
-
arw01 As Brian has already indicated nothing is linked to Access Points. All RF aspects of the Insteon mesh network are automatic. Once a Dual Band device has power the RF side is functional. The Motion Sensor symptom is consistent. There is some problem with RF where the devices are being tested. Could be interfering with RF activity or the powerline signal is not reaching the PLM location. Are there Venstar thermostats with the Insteon dongle. Some of the older units have been known to create RF issues but I thought SH had replaced as those dongles.
-
I would recommend two Access Points. That way they can be moved around to different outlets until they are on opposite 120v legs and in RF range of each other. It can be done with the PLM and one Access Point but the Access Point may have to be positioned in a location that is not the best for other RF devices in the future.
-
There is no response from the device with Insteon address 1C 3D 83. There will be trace entries that start with 02 50 or 02 51 when the device is communicating. Sitting on an Access Point may not be the best thing compared to a few feet away. Set the RL2 vertically rather than laying flat. Be sure the RemoteLinc2 LED is blinking showing it in linking mode before starting the device add process. Double check the device address. Sometimes 8s and Bs look the same.
-
Either put all the Insteon devices, PLM and all other Insteon devices on the same 120v leg or get two Access Points to couple the 120v legs (phases). Insteon signals have a hard time getting from one 120v leg to the other as the signal has to travel out to the power company transformer and back if no coupling is done. Not realistic to have Insteon devices on both 120v legs without coupling.
-
foxcob I am able to set my v.36 KeypadLinc LED Brightness level on 3.3.6. i don't remember if an event trace was run on the previous ISY levels. These are trace entries from 3.3.6, setting to 0/15, 4/15, 7/15. Sat 12/15/2012 07:55:49 PM : [iNST-TX-I2 ] 02 62 15 9A F9 1F 2E 00 01 07 0F 00 00 00 00 00 00 00 00 00 00 BB Sat 12/15/2012 07:55:49 PM : [iNST-ACK ] 02 62 15.9A.F9 1F 2E 00 01 07 0F 00 00 00 00 00 00 00 00 00 00 BB 06 (00) Sat 12/15/2012 07:55:50 PM : [iNST-SRX ] 02 50 15.9A.F9 19.70.06 2B 2E 00 (00) Sat 12/15/2012 07:55:50 PM : [std-Direct Ack] 15.9A.F9-->ISY/PLM Group=0, Max Hops=3, Hops Left=2 Sat 12/15/2012 07:56:04 PM : [iNST-TX-I2 ] 02 62 15 9A F9 1F 2E 00 01 07 4F 00 00 00 00 00 00 00 00 00 00 7B Sat 12/15/2012 07:56:04 PM : [iNST-ACK ] 02 62 15.9A.F9 1F 2E 00 01 07 4F 00 00 00 00 00 00 00 00 00 00 7B 06 (00) Sat 12/15/2012 07:56:04 PM : [iNST-SRX ] 02 50 15.9A.F9 19.70.06 2B 2E 00 (00) Sat 12/15/2012 07:56:04 PM : [std-Direct Ack] 15.9A.F9-->ISY/PLM Group=0, Max Hops=3, Hops Left=2 Sat 12/15/2012 07:56:24 PM : [iNST-TX-I2 ] 02 62 15 9A F9 1F 2E 00 01 07 7F 00 00 00 00 00 00 00 00 00 00 4B Sat 12/15/2012 07:56:24 PM : [iNST-ACK ] 02 62 15.9A.F9 1F 2E 00 01 07 7F 00 00 00 00 00 00 00 00 00 00 4B 06 (00) Sat 12/15/2012 07:56:25 PM : [iNST-SRX ] 02 50 15.9A.F9 19.70.06 2B 2E 00 (00) Sat 12/15/2012 07:56:25 PM : [std-Direct Ack] 15.9A.F9-->ISY/PLM Group=0, Max Hops=3, Hops Left=2
-
Regarding communication with the SwitchLinc, although the PLM and SwitchLinc are Dual Band devices, with the PLM at the power panel it may not be in RF range of the SwitchLinc. If the 4 tap Set button test is done using the PLM does the SwitchLinc show it is receiving the PLM RF?
-
The PLM LED is normally On unless in Start Linking operation which would have the LED blinking or when there is Insteon traffic. Is the ISY and PLM near each other. Although done with an Ethernet cable the PLM to ISY connection is a Serial interface that has a relatively short cable restriction compared to an Ethernet connection. If it is a short cable, fully snapped on both ends and connected to Port A, it sounds like an issue with the PLM. Also the PLM should be powered before the ISY is booted up.
-
The 4 tap Set button test is described in the Access Point User Guide. There is a link to the User Guide on the Smarthome sales page for the Access Point. The 4 tap Set button test does not create any links or do any configuration. It simply puts one of the Access Points into a test mode where it sends a repeated RF message. By looking at the LED on the other Access Point(s) the blinking and color pattern indicates if it is in RF range and if it is on the opposite 129v leg (phase).
-
sbuckler Thanks for checking that information and it is NOT correct. The UI and Firmware should both indicate 3.3.6. Either the Java cache was not cleared and/or the URL used to invoke the Admin Console (UI) has not been updated to pull the 3.3.6 Admin Console.
-
'If Status' triggers a Program when Status changes. In Non-Toggle Off mode only Off commands are sent so the Status never changes from Off. Working on the Program is not the answer. When a Program does not reliably trigger on an 'If Control' which is looking at the commands/messages coming from the device, it means comm from that device is not reliable.
-
Plug in the PLM first. Give it a few seconds to boot up. Then connect the external power supply to the ISY. See if that provides communication with the PLM.
-
db2ace2 Before going back to an earlier image check the EZFlora actually has power. I have two EZFlora devices , both pre and post I2CS which are fine on 3.3.6. EDIT: depending on what the previous ISY firmware was, the later 3.3.x images fixed a bug where communications problems with the EZFlora did not result in the nodes being marked with a Red !. This meant that Program function Is Responding/Is Not Responding did not work for the EZFlora. This was corrected in the later 3.3.x images. Likely the EZFlora was having comm problems that went unnoticed because the nodes were not being marked with the Red ! as they are now.
-
The Local Ramp Rate and Responder Ramp Rate (Scene) are different things. The Responder Ramp Rate for each Controller of the Scene can be different as that information is stored in the link records in the OutletLinc link database, where the Local Ramp Rate is normally stored in the device configuration area of memory. I have found HouseLinc to be current with what can and cannot be done at each firmware level as HouseLinc maintains that information by firmware level. I expected to find some unique command sequence to set the Local Ramp Rate using HouseLinc. Instead HouseLinc has no option for setting the Local information, On Level or Ramp Rate, for this OutletLinc. See my EDIT in a previous post for how to set the Local Ramp Rate manually using the Set button. The process is documented in the OutletLinc User Guide.
-
I added the OutletLinc to HouseLinc which does not present an option for setting the Local Ramp Rate for this particular device type and firmware level. This OutletLinc has v.40 firmware and is not I2CS. I have to conclude this version of the OutletLinc does not support setting the Local Ramp Rate programmatically. Perhaps it has to be the new I2CS version to have this capability. EDIT: The OutletLinc User Guide indicates the Local Ramp Rate can be set by adjusting the Bright/Dim level and tapping the Set button twice (quickly). The OutletLinc beeps when done correctly and does adjust the Local Ramp Rate. Does not appear to have the range of ramp rate values normally available when doing it this way. EDIT2: the OutletLinc User Guide has a chart that lists the Local Ramp Rate values that can be set. It shows a maximum of 8.5 seconds which explains why I was not able to set the Local Ramp Rate to long ramp values.
-
Watch that Id for future advertisement
-
I cannot set the Ramp Rate (applied locally) on my OutletLinc Dimmer. This will take some investigation.
-
Move the slider to some other position. When the Progress Bar is finished (that update is complete) move the slider to where you want it. The ISY does not write a value to a device it thinks has already been written. If the ramp rate is not achieved run Tools | Diagnostics | Event Viewer at LEVEL 3. Move the slider to some other position and back to the desired ramp rate once the first progress bar completes. Post the trace. What ISY firmware is being used? What is being controlled from the Admin Console, the specific device node or the Scene?
-
There are multiple On Level and Ramp Rate values in a device. The On Level (applied locally) and Ramp Rate (applied locally) have an effect when the OutletLinc is controlled locally or with an Insteon Direct command. When an ISY Scene is used each Controller of the Scene has a unique set of Responder On Level and Responder Ramp Rate values unique to that Controller. All this information is stored in the Responder (OutletLinc in this case) and keyed to the Controller Insteon address. When the Sensor turns the OutletLinc On/Off the Responder On Level and Responder Ramp Rate in effect are displayed when the Red Controller node below the Scene name is selected. When the Scene name itself is selected the ISY PLM is the Controller which will have its own set of unique Responder On Level and Responder Ramp Rate values for the OutletLinc. These values are in effect when the ISY Scene name is controlled from the Admin Console or with an ISY Program. EDIT: note that the 9 minute ramp rate is actually something like 0.2 seconds. SmartLabs made that change some years back to avoid a 00 Ramp Rate (the 9 minute value) from looking like the device was not responding at all.
-
Are there Access Points on all three phases? I don't think Smarthome will support 3 phase questions so things are pretty much left to the customer to resolve. Run Tools | Diagnostics | Event Viewer at LEVEL 3. Do whatever is necessary to trigger the Inputs and Outputs, watching the time stamps on the respective Insteon traffic as well as the Hops Max=x and Hops Left=y counts. Might be well to post an event trace showing a representation of the variours Inputs and Outputs being turned On and Off.
-
Are the Harmony buttons actually assigned specific IR codes. The last time I loaded my Harmony 300 with the ISY codes all the codes were added but not assigned to the actual buttons. It was necessary to use the Harmony utility to assign specific codes to specific buttons. No idea if the Harmony 1100 load is the same way.