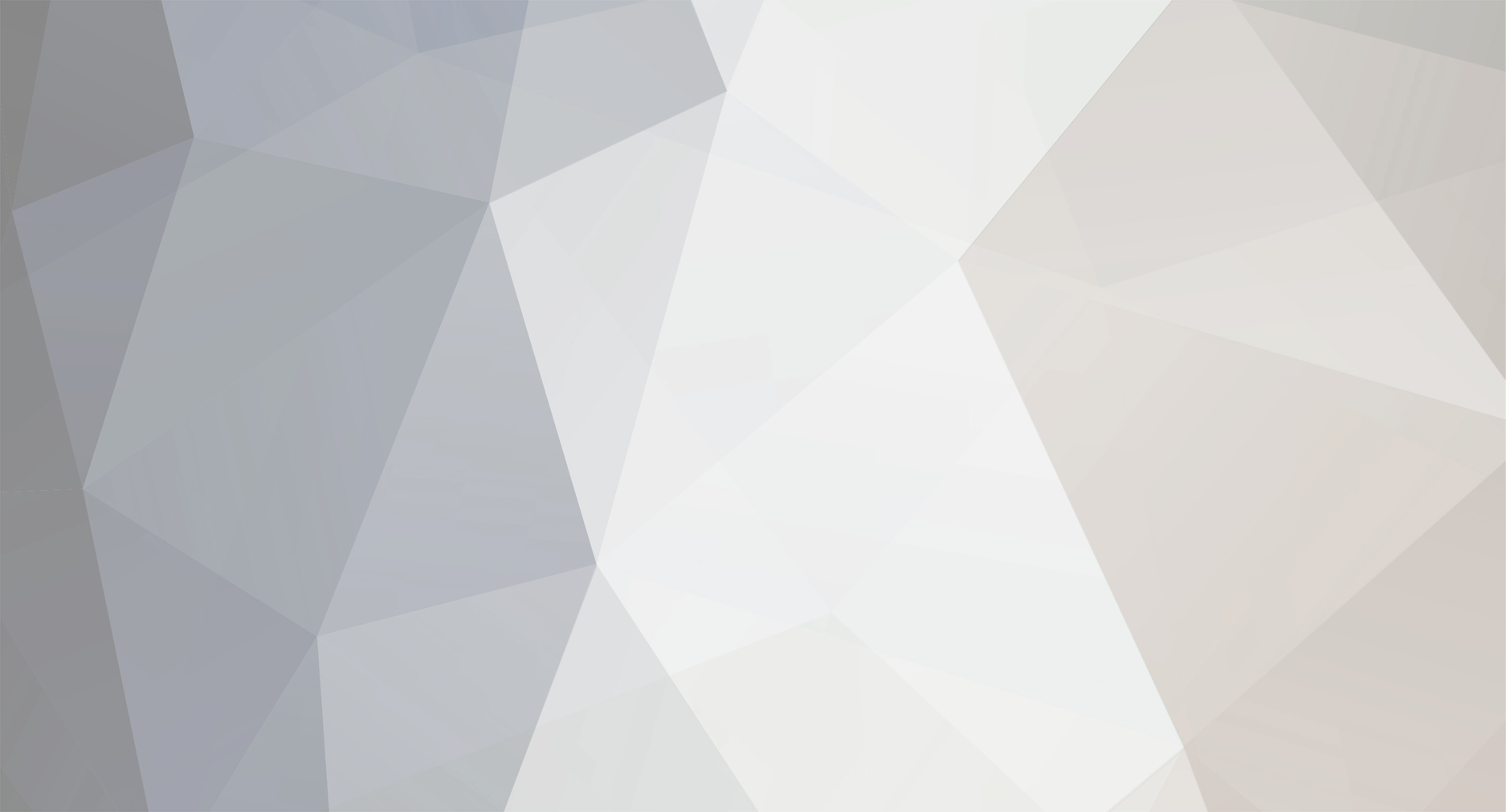
LeeG
Members-
Posts
12943 -
Joined
-
Last visited
Everything posted by LeeG
-
theedudenator What ISY firmware is being used? Help | About will display the ISY Firmware and UI (Admin Console) levels. Note that 3.2.6 does not handle new I2CS I/O Linc options correctly. Need to move to 3.3.7 (RC4) if on 3.2.6. The momentary mode is one of the things that is not set correctly at 3.2.6 when the I/O Linc is I2CS. Note that Set Options is setting the I/O Linc options. Although some apply to the Sensor and some apply to the Relay there is only one set of options in the I/O Linc which are displayed regardless of which I/O Linc node is used for Set Options. Also note that Smarthome has changed the magnetic switch shipped with the Garage Kit. The Wiki was written back when the magnetic switch had both a NO and NC switch built into the one device. Now the
-
The 4 tap Set button test should work from the PLM. If it is not in range of specific Dual Band device there will be no reaction by that device. A Red blinking LED for an Access Point means the AP is on the same 120v leg as the Dual Band device where the Set button was pressed 4 times. The 2477S User Guide indicates a Red blinking LED means the RF signal is being received and the device is on the same 120v leg. Regarding the Event Trace, that indicates the PLM is not working. A Serial command is issued but the PLM did not echo the command back. Does Tools | Diagnostics | PLM Info/Status indicate the PLM is connected. If showing connected suggest doing a factory reset of the PLM and a Restore Modem (PLM). If the Event Trace continues to show no echo messages and the PLM shows Connected the PLM is defective.
-
JCBond Try a right click on the device Primary node, select Diagnostics | Query Insteon Engine. The later levels of the ISY firmware are dependent on this value being correct.
-
Sorry for the frustration. Insteon can do that. There is nothing besides the 4 tap Set button test to check RF communication. Applications (ISY) has no control of the RF aspect of the Insteon Mesh Network. A test that will determine if the SwitchLinc is defective is to connect the SwitchLinc to an Appliance cord (plug on one end, bare wires on the other for connection to the device) and plug the SwitchLinc into the outlet with the PLM. If it does not work there then either the device is defective or the ISY firmware is not late enough to have the support for an I2CS device. After plugging into the PLM outlet run Tools | Diagnostics | Event Viewer at LEVEL 3. Then add the device. Post the event trace. It will show how well the PLM was able to communicate with the SwitchLinc when plugged into the PLM location. The Access Points were not a waste of time. They are generally needed for good phase coupling so their use is good even if they did not resolve this issue. EDIT: is this the only Insteon device available to add to the ISY?
-
Doing a factory reset of the PLM only (do not reset the ISY) will reset the PLM back to factory defaults and clear the link database. A Restore Modem (PLM) is required after that but it should be rather quick with only 5 devices. The ISY and PLM are communicating Ok. When a command is set to the PLM over the Serial interface the PLM echoes the command back to the application. The event trace shows this aspect of the PLM is working fine. It would be the powerline side of the PLM that is not working if it is a PLM issue. There have been cases where a factory reset resolved an issue that a simple power cycle would not.
-
Thanks for the event trace. The 02 6x messages are outbound. Inbound messages are 02 5x. Nether device is responding to commands sent to it. If all the devices are like that the PLM is suspect or something on the powerline is interfering with communication. First thing to try is to power cycle the PLM. It that does not resolve then look for a source of powerline interference. Could be a defective PLM but a device failure is the last thing I consider. I am assuming these are wired devices, not RF only devices such as motion sensors, TriggerLincs, etc as RF devices have to be put into linking mode before they would respond and they must be in range of the Dual Band device. The Access Points can be unplugged for 30 seconds or so to see if a power interruption has hung them up.
-
Need a Tools | Diagnostics | Event Trace at LEVEL 3 to be sure but that error message is normally the result of not getting a response from the device. If the event trace does not show Insteon messages that start with 02 50 or 02 51 the device is not responding. You can post the event trace. DO NOT Delete the PLM. That removes all references to the PLM in all devices. Power cycle the PLM and do a Restore Modem (PLM) which will rewrite the PLM link database. The link database is not necessary to Query a device or turn an individual device On/Off. EDIT: actually my last comment about being able to control the device On/Off is not true with I2CS devices. If the Insteon devices are relatively new they are likely I2CS devices which require a special link record in the device and the PLM.
-
Randallk “establishing a new device it gets to about 10% on the scroll bar and just disappears.†In addition to the things Brian mentioned which should be verified first, check the Insteon address being added. It sounds like the device address is already known to the ISY. Click on My Lighting, then double click the Address column header to sort by Insteon address.
-
That is normal for the RF only devices. They are asleep to save battery life so they cannot be queried when the ISY starts up like wired devices can be. They also do not actually have any real Status like a LampLinc or SwitchLinc for example. Even if they were awake they would not have any status to report. The ISY simply keeps track of the last command received from these devices.
-
Either is expensive when starting from scratch. ISY with PLM and external power supply At least two Access Points (2443) - perhaps more to give coverage to the wireless motion sensors As many motion sensors as needed to cover the areas to be monitored Maybe some FilterLincs depending on whether the powerline needs filtering Also note that the Insteon Motion Sensors (as well as the security motion sensors) sense motion not presence. If someone sits in a chair or naps on the sofa the sensors will not detect that. This also assumes there is a permanent Internet connection available. The ISY has no dial capability. I don't have the background to define a security system to do what is needed. Smarthome carries the ELK M1 which many folks like but they are not cheap.
-
No special SDK programming is necessary. An ISY Program can monitor all the Motion Sensors and if no motion is sensed within whatever time you define, the Program can send an email. If Control 'motion sensor 1' is switched On or Control 'motion sensor 2' is switched On or Control 'motion sensor 3' is switched On Then Wait 1 hour Send Notification to .......... Else Each time a motion On message is received the Wait timing starts over from the beginning. If no motion is sensed within 1 hour is this example an email is sent. As many Motion Sensors as needed can be added to the If section. Note that Insteon is not rated for life monitoring activity. A Security system has battery backup and is rated for the higher protection.
-
Without Jumper 5 On the Motion Sensor uses the other jumpers for configuration. Not sure what the motion sensor is going to do when trying to configure it with software without jumper 5. The Motion Sensor was certainly sending an Off command when it should have been sending an On command. Not sure it that had to do with switching batteries or the MS is not happy getting conflicting directions (software setting configuration without jumper 5).
-
wwat Smarthome changed the Item # to the new scheme now that they are supporting different RF frequencies for different countries. The US model (-222) uses the same cat/subcat (device type) as the 2420M and operates exactly the same. There is no need to override with a specific Device Type setting. Does the Red LED blink when motion is sensed even though it does not send a motion On message? I am running 3.3.7 so cannot verify directly but I tested setting the On Only option on both a non-I2CS and I2CS motion sensor. The On Only option is working on both variations at 3.3.7. The Set button will send a Motion Off regardless of options. If the Red LED does flash when Motion is sensed run Tools | Diagnostics | Event Viewer at LEVEL 3. Post the event trace. The Red LED will blink when Motion is sensed and not send a Motion On if not in Sensing Mode (Occupancy Mode) and the motion sensor is counting down the timeout interval. If not in the timeout interval and no Motion On is sent put the Motion Sensor into linking mode and click the Set Options. What is each of the six options set to and post the event trace generated when doing the Set Options. Except for being in the timeout interval there is no option that stops a motion sensor from sending a Motion On.
-
seallred The ISY will not pull the information from the PLM. However, one device can be added using the "add devices found in links and keep existing links". Depending on how the devices are linked together it may take adding more than one device. Using the KPLs generally gets more devices than a single SwitchLinc. I would recommend against using that method. Devices are defined by Insteon Address, not a meaningful name, and the Scenes defined from the links have numeric names (Scene 10, Scene 11). Also it is common to have broken links even in a working configuration which will be carried forward. Defining each device individually allows a meaningful name to be assigned as the device is added. Also using the "remove existing links" (default option) insures any half/broken links or references to devices that no longer exist are removed.
-
No problem Brian. Better to have multiple responses than none at all. Besides you have some information about using a resister I did not think about. The forum use to show the new post when the Submit button is used requiring a second Submit. Not sure that is working currently. I lost my email alerts when a post is done so there are a few kinks to work out.
-
UDI is migrating the web data to a new ISP which is why the wiki is down. They posted an estimate of a few hours. Are you migrating from a 99i to the 994i using the same PLM? If so restore an ISY backup from the 99i onto the 994i. That should be all that is needed. If that is not scenario please detail the actual circumstances
-
Add an additional load to the ApplianceLinc. The small amount of current used for load sensing is enough to cause what you are seeing. A small wall wart, night light, something like that.
-
ELA Turn On the Event Trace and issue a Scene On or Scene Off through the Admin Console. That will provide an example. It is the standard Group Broadcast message, just sent with 02 62. A Scene Serial command (02 61) issues the Group Broadcast and then follows up with Group Cleanup Directs for each Scene Responder. The individual messages, Group Broadcast and Group Cleanup Direct, can be issued by the application rather than issuing the Serial Scene On/Off to have it done automatically. The ISY is not the only application to issue the individual Scene messages directly. Powerhome has macro (like a Program) commands for issuing either message type directly. Sorry for the slow response. I lost my email alerts to new postings when the forum was moved to the new provider.
-
ELA I think he used the same technique the ISY uses for Scenes. Issues a Group Broadcast directly rather than issuing a Serial Scene command to the PLM. There are no ACks and no Group Cleanup Directs so things go as fast as the PLM will write the messages to the powerline. Did need a good powerline with no ACKs and no Group Cleanup Direct. There was some change, maybe with the PLM firmware (just too long ago to be sure) that was going to reduce the throughput making it impossible to create the more complex lighting sequences
-
I would not expect operating multiple Insteon switches to cause such a result. Only one Scene can be operating at a time as far as Insteon is concerned. A device will terminate the Scene it is working on if another Scene is started from another device. Does the ISY Log (not the error log) show a change in device status of many devices at that time?
-
Is the My Lighting Scene used in any Programs besides the 3AM Query? I have seen problems resulting from trying to use the My Lighting Scene for things other than the daily Query. That would not explain Secondary KPL button LEDs turning On as they are not covered by the My Lighting Scene. Was there any type of power interruption around that time? Something of very short duration that might explain affecting many devices at once.
-
“What I want is to switch on KPL Button 1 - get both lamps on, and KPL 1, KPL 3 and KPL 4 to light up.†“This all works fine EXCEPT when I turn KPL 1, KPL 1 goes on, but immediately goes off†I took the above to mean everything worked which included “get both lamps On†except that the Program was turning KPL1 button Off when not desired. “Also, it doesn't appear to me that turning off the KPL1 button does in fact change the status of either lamp.†That is correct. Turning the KPL 1 Off with a Direct command has no affect on any of the Responders that may be linked to KPL button 1. Insteon does NOT propagate Direct commands sent to a device to any linked Responder(s). Yes, checking the ‘reaction’, that is the OutletLinc Status, would pick up another Controller if added to the mix in the future. “any idea why putting the logic to turn off the KPL1 into a separate program didn't work?†I’d like to see the actual Programs posted to be sure but the issue here is not the Then clause changing the things the If is checking as it is not. Moving to two Programs resolves that situation. The problem is the Scene that is activated when KPL button 1 is pressed On is affecting the status of multiple devices. When one of the OutletLincs changes Status (to On in this case) the Program is triggered. The other OutletLinc is still Off at that point so the Program If is True driving the Then clause. Again, it is not what the Then clause does that causes the problem but what the Scene driven by KPL button 1 turning On. I’ll have to give some thought on how to resolve and still be able to add additional controllers in the future without having to change the Program as well.
-
Red wire of 3 wire cable is connected to the Black bundle which does put hot on that wire. That could be left alone and connected to the Black wire on the Insteon switch in the entry box but that is NOT convention when not connected to a 3-way switch. The Red wire in the 3-wire cable should be disconnected and capped. Then use the Black and White wires in the 3-wire cable to supply unswitched power to the entry Insteon switch. There is a difference between what will physically work and what is expected wiring convention should an electrician work in either of the boxes. An electrician would expect the possibility of power on the Red wire of the 3-wire cable when it is connected to a 3-way circuit. Once converted to Insteon there is no longer a physical 3-way circuit. There is a logical 3 way configuration accomplished by linking the two Insteon switches together. From an electricians point of view he will not be expecting power on that red wire because the 3-way circuit has been dismantled. However, it is your house so do whatever you want with it. .
-
Be sure to turn breaker Off before making changes. Make changes to both the garage and entry locations before power is restored. Cable 1 is 2 wire blk/white (blk goes to dark colored screw on 3 way switch) (white to Neutrals) This should be the cable going to the lighting fixture(s). Black goes to the Red load wire on the Insteon Switch. White is neutral to fixture(s) and remains as currently connected. Cable 2 is 3 wire blk/white/red (blk and white to 3 way switch) (red to wirenut with all blacks) This should be the cable going to the entry box 3-way switch. Remove Red wire from Black bundle and cap. Black wire to Black bundle (where Red wire was) and White wire to White neutral bundle. Be sure to make the entry box changes before returning power to box. The Black/White wires will be supplying unswitched power to the Insteon switch in the entry box. The Red traveler wire is no longer needed or used. Do not cut Red wire off, just cap it in case the normal 3-way is restored when house is sold. The Insteon switch in the garage box, Black wire to Black bundle, White wire to White bundle. This provides unswitched power to the Insteon switch in the garage box. In the entry box, the Red wire on the existing 3-way switch is capped (no longer needed or used). The Black and White wires have been retasked in the garage box to provide unswitched power. The Black wire goes to the Black wire on the Insteon switch. The White wire goes to the White wire on the Insteon switch. The Red load wire on the entry Insteon switch is capped. It will control the garage Insteon switch by linking the 2 switches together.
-
djones1415 Check my previous post just above your last post. Pressing KPL button 1 is changing the Status of the OutletLincs. As soon as the Status of one is turned On the Program triggers. Since the If conditions are ORed together the other OutletLinc is still Off so the Program turns KPL button 1 Off. The Program looks like it was written to react to KPL button 3 or KPL button 4 being turned Off. Works good for that. The problem being it is also triggered when the first OutletLinc is turned On. Any change to Status of tested devices triggers the Program.