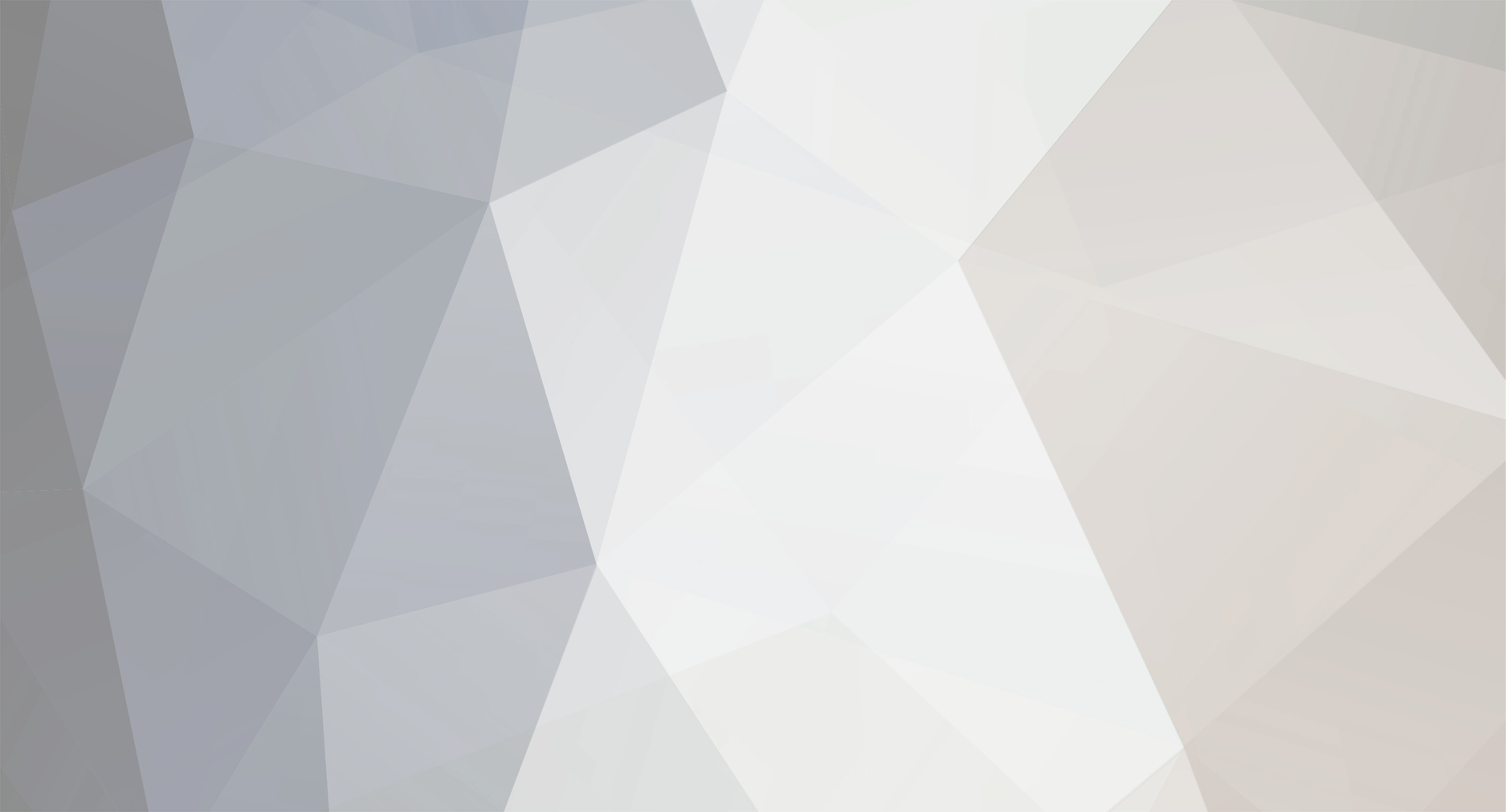
LeeG
Members-
Posts
12943 -
Joined
-
Last visited
Everything posted by LeeG
-
You will define an ISY Scene with a KeypadLinc button as a Controller and one or more devices as Responders. When the KPL button is pressed On/Off the Responders will follow. To add the RemoteLinc2 simply add the appropriate RemoteLinc2 button as an additional Controller to the same ISY Scene.
-
No one has reported a problem with the NC variant of the Load Controller but I suspect they are not used as much as the NO. if you do switch to the NC keep in mind if something fails and the Load Controller reverts to its default NC state the load will be powered. Not a problem if that is not critical but I switched from an older NC Load Controller to a NO Load Controller because it was controlling a pump. I did not want the pump to accidently run dry because the Load Controller came up in the NC state.
-
Do a Show Device Links Table and post the results. If screen/window capture is not available post the saved XML file. Run Tools | Diagnostics | Event Viewer with Level 3. Turn the Load Controller On and Off through the Admin Console and post the event trace. This does not look like a problem the ISY can code around. The commands being issued are correct and the link record commands earlier in the trace worked. For some reason the Load Controller firmware decides to reject a valid command, reason unknown. Another user did RMA the Load Controller and the new one had the same behavior. Presumably at the same firmware level so the results would be expected to be the same.
-
I believe another user went back to 3.3.1. Be sure you have a backup taken at whatever level you go back to. 3.3.2 changed some things in the configuration that is not backwards compatible. The next beta (3.3.3) is due out in a week or two. Maybe sooner
-
beachfront71 This was just reported under the 3.3.2 topic as well. Looks like a glitch in the 3.3.2 code. Turning the Relay On also marks the Sensor On even though the Sensor did not actually turn On. (no Green LED). A Query restores the Sensor to the correct Status although that may not be useful in your case. EDIT: the event trace confirms the Sensor being marked On even though only the Relay was sent an On. UDI tech support has been notified. Sun 09/23/2012 11:52:28 AM : [iNST-TX-I1 ] 02 62 1C FD D5 0F 11 02 Sun 09/23/2012 11:52:28 AM : [iNST-ACK ] 02 62 1C.FD.D5 0F 11 02 06 LTONRR (02) Sun 09/23/2012 11:52:28 AM : [ 1C FD D5 2] ST 255 Sun 09/23/2012 11:52:28 AM : [iNST-ACK ] 02 62 1C.FD.D5 0F 11 02 06 LTONRR (02): Duplicate or ACK for a different device Sun 09/23/2012 11:52:28 AM : [iNST-SRX ] 02 50 1C.FD.D5 19.70.06 2B 11 02 LTONRR (02) Sun 09/23/2012 11:52:28 AM : [standard-Direct Ack][1C.FD.D5-->ISY/PLM Group=0] Max Hops=3, Hops Left=2 Sun 09/23/2012 11:52:28 AM : [ 1C FD D5 1] ST 255
-
I can confirm that result. Looks like a glitch in the 3.3.2 drop. The actual I/O Linc Sensor is not being turned On (no Green LED On) and a Query returns the I/O Linc Status to Off.
-
Thanks for the trace. That is the issue that is being attributed to the firmware in the latest Load Controller. The initial link record was written successfully so I think the Load Controller can be turned On and Off with the Admin Console or a Program.
-
Delete the Load Controller from the ISY. Factory reset the Load Controller. Run Tools | Diagnostics | Event Viewer at Level 3. Add the Load Controller to the ISY using New INSTEON Device. Enter the Insteon address, Name of your choice, and leave Device Type at default Auto Discover. Post the event trace. There is a problem with the Load Controller that has occurred with multiple users. It is falsely NAKing commands. The event viewer will show if it is this problem or an actual communications problem.
-
Where is the magnetic switch mounted? Is the magnet next to the reed switch when the door is fully open or when the door is fully closed? Is the Sensor status being viewed from the Admin Console or MobiLinc? If MobiLinc what does the Admin Console show?
-
Some of the results are expected and some are not. The first trace using Automatic issues I2CS Extended commands to read the link database which is correct. The unexpected aspect is there are link records being read successfully which also explains why the device can be controlled On/Off. These link records could not have been written using the I1 Advanced option. The second trace using I1 Peek commands fail as expected because the internal I2CS PLM does not implement Peek/Poke. Note that Poke cannot work without a functional Peek. To write data the sequence is Peek to establish the memory low order address byte followed by a Poke with the data to be written. Despite the earlier trace that shows a NAK using extended commands in automatic mode, at some point these commands did work. There are two link records in the Load Controller and the only possible way to get those link records is with I2CS Extended commands. At some point a device add in Automatic mode did work which leaves as an open question why does the Load Controller NAK those commands some of the time. Once the link records were created successfully they will remain unless a factory reset is done. The first page of this topic covers a user who had the same symptom, getting NAKs. The replacement Load Controller worked. At some point your Load Controller worked as the existence of the two link records indicates. Again, these two link records could not have been created using the I1 option. The Peek/Poke commands were “depreciated†commands as far back as the 2007 Insteon command spec. It took the conversion to the I2CS Insteon spec for the Peek/Poke commands to actually be discontinued. To summarize A. the Query Insteon Engine in the last Automatic trace does indicate an I2CS device B. two link records were successfully read using I2CS extended commands C. the two link records could not have been written using the I1 Advanced option D. the Load Controller On/Off functions because the required link records exist E. at some point a device add worked successfully creating the needed link records F. why the Load Controller NAKs otherwise correct commands some of the time is an unknown
-
Yes. In 6 button mode the ON and OFF buttons are complementary. They represent the physical load (if Red wire connected) On/Off status. The ON button LEDs are bright when the load is On and the OFF button LEDs are bright when the load is Off. If a Dimmer the ON and OFF buttons can dim and brighten the load. They can also dim and brighten a Scene regardless of whether the KPL is a Relay or a Dimmer. Of course the ON/OFF buttons can function as a Controller of one Scene, turning the Scene On and Off independent of whether a load is attached to the Red wire. Some folks have configured a 6 button KPL in 8 button mode (or used an 8 button KPL) using the large double buttons in the top and bottom positions (sometimes in all four positions). In 8 button mode the A/B buttons function independently of the G/H buttons so the A/B buttons can be used to control Scene X and G/H buttons can be used to control Scene Y. Normally custom labels are used in this situation as ON and OFF no longer have any meaning when in 8 button mode.
-
brookbphx If you do decide to run the event trace of a Show Device Links Table issue the Query Insteon Engine as the first thing after starting the Event Viewer at Level 3. The earlier trace shows the device did respond as an I2CS device. This Query Insteon Engine will show if the device continues to show an I2CS device.
-
That is a function of the SwitchLinc firmware. Toggles between the Local On Level and 100% On. I don't know of any way to change the way the SwitchLinc firmware works. A Program could be triggered from the On paddle press and issue an On to 80%. Depending on the Ramp Rate it may not get much brighter before the Program request sets it back to 80%.
-
The first statement in the Then clause turns the ON button LEDs On. The second statement in the Then clause turns the OFF button LEDs On If Then Set 'KPL Floor Dimmer 6' On Set 'KPL Floor Dimmer 6' Off Else - No Actions - (To add one, press 'Action') If there was something connected to the Red load wire these statements would also turn the load On and Off
-
The KPL load control button is controlled in the same as any other Insteon device. It can be turned On/Off with Direct commands as would be used with a SwitchLinc, LampLinc, ApplianceLinc, etc. Of course it can be a Responder or Controller of a Scene. Turning the Scene On/Off turns the KPL load On/Off just as a Direct command would. The exception with a KPL is a Secondary button cannot be controlled with Direct commands. The KPL has one Insteon address. The Insteon Direct On/Off commands have no means of specifying which KPL button to apply the command to. An Insteon Direct On/Off command sent to a KPL controls the KPL load and load button(s).
-
If you want to do additional diagnostic work, run Tools | Diagnostics | Event Viewer at Level 3. Go back to the I1 Advanced option and run a Show Device Links Table followed by a Compare. Post the event trace and what is the result of the Compare. Be sure to put the Advance option back to Automatic when finished.
-
Sure, assign the KPL button as a Responder to an ISY Scene. Turning the Scene On and Off turns the KPL button LED On and Off. I am assuming you are asking about a KPL Secondary button (not the load control button). Secondary KPL buttons cannot be turned On/Off with Direct commands. Has to be with a Scene.
-
I2CS devices have dropped the Peek/Poke commands that the I1 option uses. The commands do not fail with a NAK, they just do not function so no errors but no links. The Load Controller may have turned On/Off which is strange for an I2CS device without links but I don't think the Load Controller would respond to a Scene. It gives the appearance of a device that identifies itself as an I2CS device but does not follow the rules of other I2CS devices. The Restore Device would go back to the command sequence that New INSTEON Device uses when the default Advanced option was restored. I have no explanation.
-
Confirmed. There is +5v and the pulse water meter connection does count pulses. The shell has to provide power for the daughter card. Do not have a rain sensor to test. No reason to think that would not work with the pulse counter working. EDIT: confirmed with a pullup resister, the rain sensor also works. All of this is relative to the EZFlora with an I2CS internal PLM. It can be identified by the lack of a passthru outlet
-
There is forum category dedicated to Variables. Perhaps that is a place to start. viewforum.php?f=68
-
The lack of passthru outlet is the result of using the 2413 Dual Band shell (rather than the 2412 shell now discontinued). The RJ45 jack is located behind the green connector. The ISY does not support the pulse meter or the rain sensor.
-
The LED Backlight level controls the button LED brightness level. Regardless of the numbers set for On and Off level the KPL firmware keeps the equivalent value of 8 difference between the On and Off level so that an On button can be differentiated from an Off button. For example, both On and Off levels can be set to 8 but that does not mean the On and Off LED levels are the same. The KPL firmware internally always keeps the equivalent of 8 difference between On and Off levels. An Off level of 0 and On level of 0 is as dim as the LED gets. Incrementing the On level by 1 increases the LED level with an On level of 15 being the highest On level value. From there the Off level can be incremented by 1 until a value of 7 is reached. The Off level of 7 and On Level of 15 is the brightest level. The Backlight level applies to all buttons on the KPL. The Backlight level of individual buttons cannot be set to different levels. There are three button modes. Toggle mode where each button press alternates between On and Off. Non-toggle On mode where each button press sends an On command and non-toggle Off mode where each button press sends an Off command. Each KPL button (except ON/OFF in 6 button mode) can be set to a different toggle mode.
-
Same thing with the buttons on the left side (Remove, Move Up, Move Down) come and go as to whether they serve any function based on the clause content.
-
UDI Wiki has a good section on order of precedence. Rather than trying to remember which takes precedence just include parentheses. If Time is Sunrise - 1 hour And ( Status 'ICON Dimmer 1' is Off Or Status 'ICON Relay 2' is Off ) Then - No Actions - (To add one, press 'Action') Else - No Actions - (To add one, press 'Action') - No Actions - (To add one, press 'Action') The first Program that has only a specific time trigger should work. The Wait could be a problem if something could trigger the Program again driving the Else clause before the Wait completes but that is not the case. It is suggestive of a communication problem, perhaps caused by the specific lights in the Scene generating noise or some other appliance that is On around the time the Set Scene Off should work. The other examples where Status is checked could cause the If to be reevaluated before the Wait completes preventing the Set Scene Off from executing.
-
Assuming ICON Dimmer is controlling the Light and ICON Relay is controlling the Fan If Control 'ICON Dimmer 1' is switched Off And Status 'ICON Relay 2' is On Then Wait 10 minutes Set 'ICON Relay 2' Off Else - No Actions - (To add one, press 'Action')