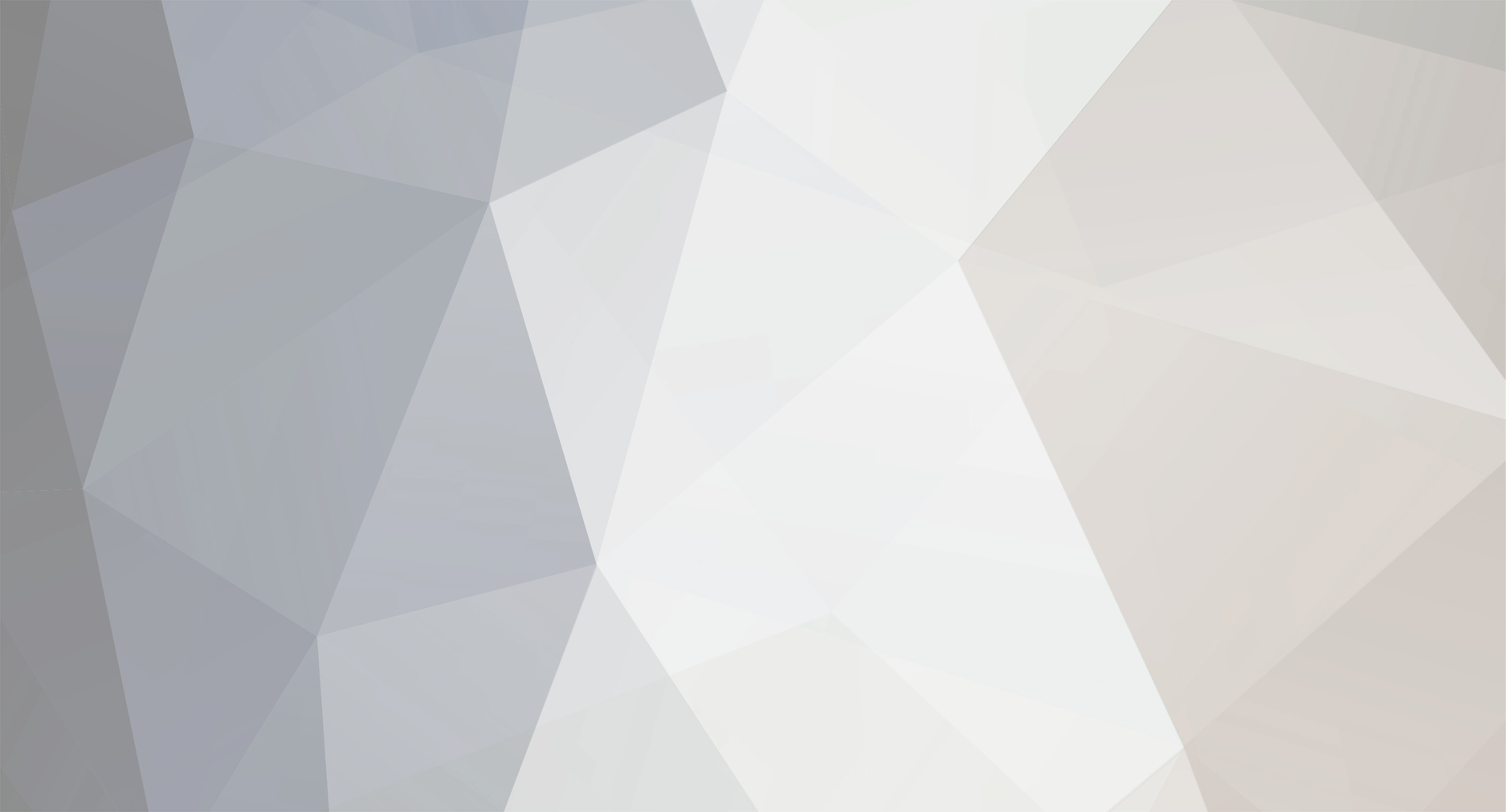
LeeG
Members-
Posts
12943 -
Joined
-
Last visited
Everything posted by LeeG
-
trzebrand Not sure what is meant by a switch activating the Motion Sensor. The Motion Sensor itself cannot be controlled by another Insteon device. An ISY Program If can combine the Status of the Switch being On with a Motion sensed message. Post your Program so we can see what is going on. Lee
-
An Access Point should work with the RL2. Temporarily move an Access Point to the same circuit as the ISY PLM and position the RL2 within a few feet of the relocated Access Point. Repeat the New INSTEON Device process. If that is not successful run Tools | Diagnostics | Event Viewer with Device communications events selected. Run through the New INSTEON Device process and post the event log.
-
awzulich That normally indicates the RL2 is not in range of a Dual Band Device. Try moving it closer to an Access Point or Dual Band PLM. Lee
-
For sure the Admin Console code running is not 3.1.10. For some reason Java is pulling an old version from the cache. There have been some posts that indicate a reboot is sometime required on Mac to clear the cache. You can try pulling the Admin Console from the UDI site with the following URL. http://www.universal-devices.com/99i/3.1.10/admin.jnlp
-
timmay By no dice you meam the RemoteLinc2 device types are not shown in the Device Type pulldown near the top (entries 5,6,7)? Suggest installing 3.1.10 and invoking the Admin Console. Check Help | About to verify it indicates 3.1.10 is the ISY firmware and the Device Types pulldown shows the RemoteLinc2 device types near the top of the list. Only when that has been achieved installed the ISY image only 3.1.11 download. This download does not include the Admin Console, it is only a fix for the ISY code itself. Lee
-
mikeneal There is no Insteon function that will blink the KeypadLinc button LED. The button could be assigned as a Responder to a Scene, with a Program turning the Scene On and Off at 1 or 2 second intervals but I STRONGLY recommend against this approach. This would generate too much sustained powerline traffic that will interfere with other powerline activity. You could turn On an ApplianceLinc that has some sort of beeper device plugged into it so that an audible beep is heard if the door is open for an extended period of time. If skilled in creating low voltage digital circuits an I/O Linc Relay could turn On a digital circuit that beeped at interval or flashed an LED. Lee There are two duplicates of the same post. Suggest logging on and deleting the duplicate posts. There should be an X in the lower right corner of each duplicate post that will delete the post. Note that when an error occurs posting an item simply login again and check the category. In almost all cases the post is actually successful even though an error is displayed.
-
Obviously that is not correct. What ISY firmware are you using? EDIT; appoligies for the wrong direction in diagnosing the problem. When the initial post said the secondary KPL button D would not turn Off I assumed the conditions to make that work had been established and were not working rather than not be able to establish the condition at all. EDIT2: Am I correct in the assumption that KPL button D was NEVER added to the Scene. Is it possible it was added before, is not working now but was added earlier. It would make more sense that it is not working as a defined Responder rather than can never be added as a Responder
-
andrew77 A Scene operates as a result of a link being created between the Controller and the Responders. In this scenario the Controller is the ISY PLM and the Responders are whatever devices have been added to the Scene as other Controllers or Responders. The KeypadLinc will have a Responder link record for the load control button (Main A) and it will have a Responder link record for button D. From the symptom it sounds like the Responder link record for button D is missing or has been corrupted. Without the button D Responder link record the KeypadLinc does not know to turn Off button D when it receives a command to turn Off the Scene. The Responder link record for Main A exists because Main A turns Off. Since button D does not turn Off the existence of a valid Responder link record for button D is in question. The suggestions in my previous post will cause the ISY to rewrite the Responder link record for button D. UPDATE: I defined a Scene with the KPL load button as a Controller and a Secondary button as a Responder and found the link records were incorrectly written. A Show Device Links Table issued for the KeypadLinc with a subsequent Compare shows the ISY Link Record information for button D does not match the actual link record in the KeypadLinc for button D. Suggest running a Show Device Links Table (right click KPL main node Main A, select Diagnostics | Show Device Links Table). When the display is complete click the Compare button. Do any of the link records indicate Mismatch? I see this on 3.1.10. What ISY firmware is being used? Lee
-
andrew77 If the KeypadLinc lost a link record delete the node from the Scene and add it back. If that does not resolve the problem try a Restore Device against the KeypadLinc. If neither resolves the problem the next thing to look at is powerline quality to that KeypadLinc. To turn a Scene Off the ISY issues a single command that is not directed at any specific device. If some devices respond and some do not the ISY has issued the single command. Either a link record problem in the device or the device is not receiving the command. Lee
-
Do not triple stack the devices for long. The heat buildup in the middle device can cook it beyond recovery. Even double stacking can be an issue for devices that generate heat. The 02 AC is an undefined serial command the PLM is echoing back (assumption about echo as it does not conform to any PLM message I've ever seen). The ISY does not trace commands sent to the PLM so this is something the PLM passed out to the application (ISY in this case). That looks like the PLM is not working correctly. It is definitely NOT the powerline communications problem I thought initially. I suggest downloading and installing a new copy of 2.8.16 just in case something happened during the download process. Also check the cable connections between the ISY Port A and the PLM. This is not an issue with 2.8.16. It has been around far too long and used by far too many folks for this to be an ISY image defect.
-
"When does the motion sensor actually send a Low Bat indicator update?" My testing showed the battery voltage had to drop below 4.5v before the Motion Sensor sent an On message for the Low Bat node and it sent the message only once. The Motion Sensor continued to work at that point so it is unknown how far back in time one would have to look to find that one message versus when the Motion Sensor would stop working. Hopefully at least weeks, maybe a month or more. If it sends a Low Bat message a few days before the Motion Sensor stops working it is not much use. I am hoping others will jump in here with observations regarding the number of Low Bat messages generated. My expectation in the beginning was to see a Low Bat message periodically once the voltage level dropped below some point. That may not be possible for the Motion Sensor since it has no means of judging time beyond the small timeout interval window.
-
dennisric Based on past observation 2.8.16 will not be updated. If incremental updates were applied to 2.8.16 code base it would become another Beta. The 2.8.x images evolved through a series of Beta releases until functional stability was reached. At that point the latest 2.8.16 image was designated as an Official release with new function/feature/device support being developed in a new series of Beta releases designated 3.1.xx. At some point 3.1.xx images will have evolved in both function and stability to the point where it is declared the next Official release. At that point new development will start with a new series of Betas, perhaps 3.2.xx. I am not speaking for UDI so the image numbers and possible Official release numbers is simply a guess based on observations over the last 3 years. For RemoteLinc2 support the choices are wait for the next Official release which will be some future 3.1.xx image or move to one of the Beta images. The 3.1.10/3.1.11 combination has been one of the best Beta images I have seen. It is still a Beta and more testing will be done by the users who chose to participate in the Beta program before one of the future images is designated Official. Lee
-
matapan The reason I ask is I think the Motion Sensor sends only 1 Low Battery On message. If the ISY is rebooted the Low Battery node On indication will be lost. I have set up Scenes where two of my Motion Sensor Low Bat nodes are linked to KeypadLinc buttons, I've set the KeypadLinc aside so that it will not be disturbed by any other testing. If the Motion Sensor Low Bat node sends an On message it will turn on a KPL button LED which will survive an ISY reboot. This is also independent of the ISY as the MS will turn the KPL button On through a link, not an ISY event. The batteries in both Motion Sensors are a few months old so it will be a few months at least before I see any results from this test. Lee
-
matapan How frequently is the ISY rebooted? Was the ISY rebooted toward the end of the battery life? Lee
-
Unkfinger Some of the symptoms described indicate powerline communications problems. If I turn the statement around “I can usually turn on and off individual devices†indicates that some times devices cannot be turned On and Off. When this basic capability does not work it means Insteon has retried multiple times and failed to reach the device. When this level of communication is problematic Scenes normally have worse success because there is less automatic retry activity. Note that a "Cannot Communicate With XXXX. Please Check Connections" message will often result in a Red ! displayed to the left of the node in the My Lighting tree. Should only be necessary to right click on the node and select Query rather than restoring a backup which clears all device status. There are some basic things to check. Are the Dual Band devices that are coupling the 120V phases still functional. Run the 4 tap Set button test to verify that the devices can hear the RF signal and they are in fact on opposite 120V legs. If the ISY PLM is on a circuit with a UPS and/or computer equipment they are often sources of either noise or signal attenuation that interfere with PLM to device communication. Other common sources of problems are cell phone chargers, some flat screen TVs, CFLs that are ageing and producing noise over time, etc. One technique for determining the source of interference is to unplug the item. Simply turning it off is usually not enough because most devices today remain powered even when turned off. Lee
-
The support for RemoteLinc 2 devices was added at 3.1.10.
-
LampLincs are Controller/Responders and as such will be Red in the My Lighting tree. The color of the node in a Scene depends on how you added the node to the Scene. A Controller/Responder device (as the LampLinc is) can be added to a Scene as a Responder in which case it will be Blue in the Scene (and function only as a responder as far as the Scene is concerned) or added to the Scene as a Controller in which case it will be Red. Note that when a device is added to a Scene as a Controller it is assumed to also function as a Responder if the device has that capability. This assumption allows the ISY to automatically cross link Controller devices so the status LEDs on all the Controllers stay in sync. Do not know what the Italics means besides perhaps that it has been selected.
-
Melor When a Program does not trigger from a paddle/button press that can mean a different variant of a link record problem. Run Tools | Diagnostics | Event Viewer with Device communication events selected (most important option) and see if the button/paddle press results in Insteon messages being traced. If not either a Controller link record in the device pointing to the PLM is missing or the PLM Responder link record pointing to the Controller is missing. If this is the case something unusual happened during the PLM replacement process that corrupted the link records. A Restore Device normally resolves this but if not the only solution to basic device link records missing/corrupted (not Scene related links) is to Delete the device and add it back to the ISY. These link records were created when the device was originally added to the ISY and if Restore Device does not fix it a device Delete/Add sequence in the next solution. Lee
-
If Controllers were displayed in Blue in the My Lighting tree that was wrong. Most devices are Controllers or Controller/Responder devices so the majority of nodes in the My Lighting tree will be Red. LampLincs are Controller/Responder devices. ApplianceLincs are Responder only.
-
The node name being Red indicates a Controller, a blue node name indicates a Responder. A Controller node can also function as a Responder if the hardware has the capability. A Red ! to the left of the node name indicates the ISY PLM is having problems communicating with the device. Could be a problem with the Dual Band devices that are coupling the 120V phases. Could be something on the circuit where the PLM is now plugged causing interference.
-
Yes, that has been noted by just about everyone who has installed a RemoteLinc 2. The nodes can be renamed if desired.
-
apostolakisl “So, again not owning one of these devices, when it sends an "on" statement, is it equivalent to pushing an "on" on a switchlinc?†Exactly. The basic message flow is identical. There are some redundant Group Broadcast messages because it is an RF only device but other than that a SwitchLinc On and Motion Sensor On look identical. “In other words, would simply replacing "status on" to "control switched on" be recognized? This would avoid needing two programs and would keep resetting the 45 sec timer every time it picks up movement and then finish the 45 sec's once 45 seconds with no motion detected passes.†Yes, I think that will work if the Motion Sensor timeout interval remains at 30 seconds or it is put into On Only mode. If the Motion Sensor timeout expires and sends an Off message it would not retrigger the Program because Control triggers only on the condition specified and If Control On triggers on each On message (if using On Only mode). The combination of either would allow a single Program to work (I think without benefit of an actual test to confirm). Also your original suggestion to use two Programs works. Lee
-
apostolakisl “Excuse my ignorance here, not owning an insteon motion sensor. But how does it only trigger on "on". Do you mean that it only sends out an "on" PLC command and never anything else?†Yes. Known as On Only mode. MS never sends an Off command. Useful when the Motion On turns Responders On directly with a Scene and automation is used to turn the Responders Off based on more than an absolute MS timeout interval if Off commands were allowed to flow. “In ISY, a program with an if clause containing "status", will only trigger when the status changes. So, if the sensor only sends "on" commands, it would never trigger the program since it only receives repeat "on" messages. For the program to trigger, you would need it to be a control statement ("if switched on"). But again, I don't know how ISY motion sensors do their com.†Agree completely. I think the Program was always exposed to the timing issue. If the Motion Sensor was ever in On Only mode the If Status would never trigger the Program (except for the first Motion ON following an ISY boot). “I still would bet your motion sensor is changing state during the 45 seconds and causing the program to terminate prematurely.†Also agree as the posted event trace shows the Motion Off being received Motion On + 30 seconds (default MS timeout interval) which is before the Wait 45 time expired. Lee
-
This line indicates the Motion Sensor turns On Mon 11/07/2011 10:52:50 AM : [ 13 F4 BC 1] ST 255 This line nominally 30 seconds later indicates the Motion Sensor turns Off Mon 11/07/2011 10:53:19 AM : [ 13 F4 BC 1] DOF 1 First, this means the Motion Sensor is NOT operating in On Only mode. Second this means the Program was triggered at On +30 seconds with the Off command, interrupting the Wait 45 seconds, running the Else clause because the IF is now False. The statements after the Wait 45 NEVER run. The variation is if the Motion Sensor “sees†more motion the Motion Off will be delayed because the MS timeout value is reset to a full timeout value for every motion sensed. If enough motion is sensed such that the Motion Off message occurs after the Wait 45 expires the statements after the Wait 45 execute,
-
If the Motion Sensor is configured for On Only, remove that part of the If statement as it only adds confusion to how the Program works. Post all Programs which affect the two state variables. Same basic cause, just variable related rather than Motion Sensor commands.