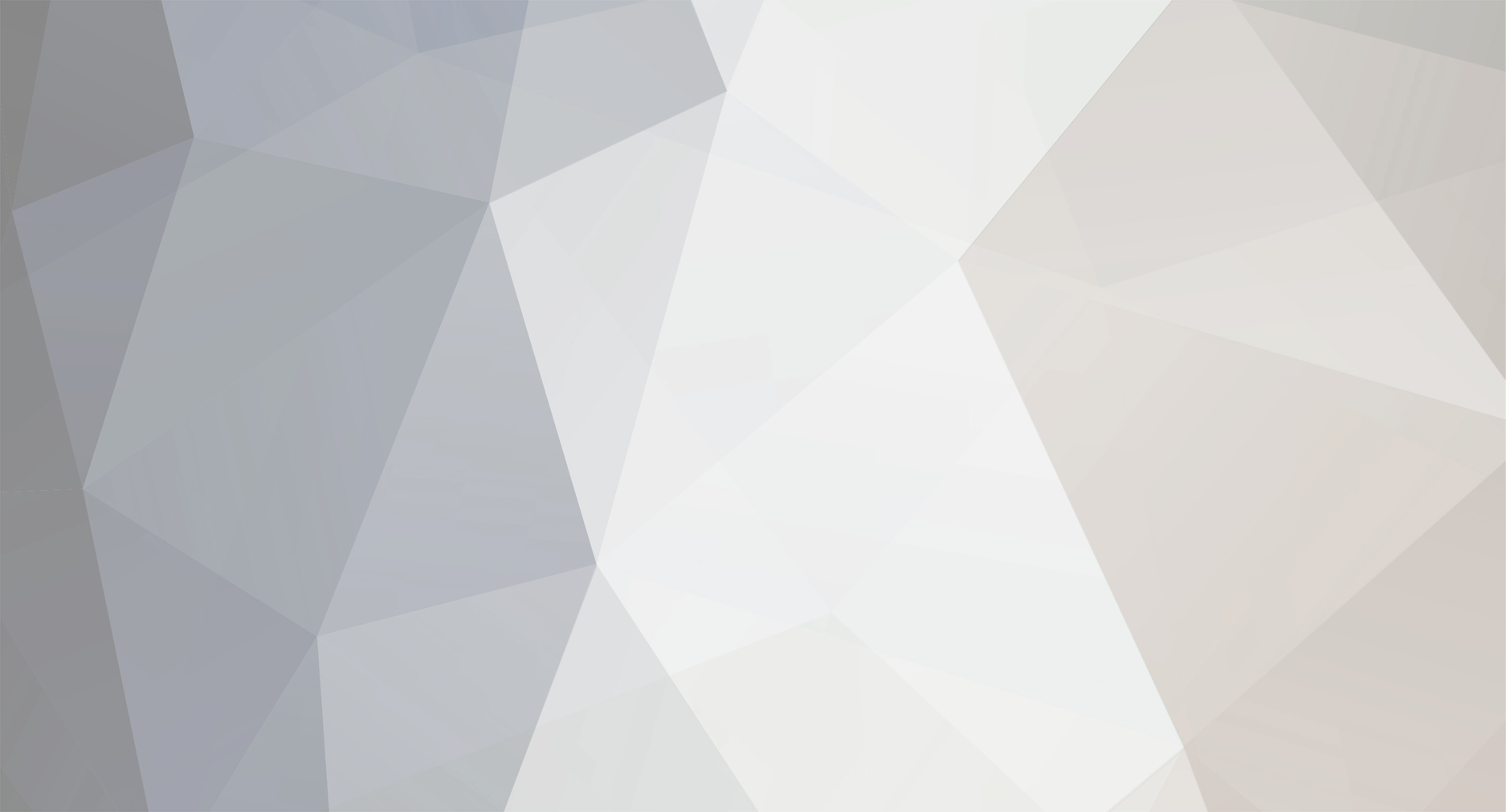
LeeG
Members-
Posts
12943 -
Joined
-
Last visited
Everything posted by LeeG
-
Michel, from the SH web site for Motion Sensor (no reference to HL2) ... "Automatically turns off after motion stops (adjustable anywhere between 30 seconds and 2 hours)" Looks like the specs have changed for a V2 motion sensor from the API document.
-
Remove the KeypadLinc and add it back specifying the device address and device type as an 8 button KeypadLinc using New Insteon Device. Likely the KPL has a firmware revision not known to ISY. You cannot turn KPL secondary buttons On/Off like the load control buttons. To turn a KPL secondary button On/Off define a Scene with the secondary KPL button as a Responder and turn the Scene On/Off.
-
My motion sensor does not send additional On commands during the timeout period. The timeout period is reset to a new full timeout value for each motion detected but no additional On commands. The Off command comes only after no motion detected for the full timeout interval. I believe you are correct. An If Control is looking at commands that are flowing and If Status is checking what the ISY thinks is the current device status. I can add an If Status for a RemoteLinc button to a Program.
-
The following IF works as a Condition with a RemoteLinc If Control 'REMOTELINC-2 - 2' is switched On I see after my post was complete you had updated your post and got it to work. Great Job! Each success leads to more fun.
-
A common cause of both Programs not triggering from devices and the ISY not seeing device changes would be something amiss with the links in the PLM. Try rebuilding the PLM with the File/Restore Modem (PLM) option. With the ISY Programs controlling devices based on time the PLM sounds like it is working, just lost the link database somehow.
-
A loss of power of a few seconds will cause the PLM and the ISY to restart/reboot. With the time based trigger Condition already past I would not expect the Program to run at power on. Suggest two separate Programs. The first Program turns the light On as the only action. The second Program Condition specifies a run time 6 hours later which turns the light Off. That way the Off Program runs even if there is an intervening power outage.
-
atmit: most of my KPLs are older revisions. With that in mind none of the KPLs I just tested will turn Off a Secondary KPL button with an On command to 0% Bright level. That technique works with the Primary KPL button (ON in 6 button mode, Main in 8 button mode) and various single output unit devices such as a SwitchLinc and ICON switch. KPL Secondary buttons do not respond in the same way, at least on several KPLs I tested here. The solution is what Sub-Routine suggested, using a Program to issue an Off command to the Secondary buttons you want to turn Off.
-
Is it that you cannot define a percentage in the Program or the percentage defined does not work?
-
Not sure if this applies to the 2411T but for devices such as the EZSnsRF and EZX10RF which also have options under Link Management and I have defined to ISY, I added the devices to the ISY first using New Insteon Device. Then used the Link Management functions to add buttons/sensors/X10 codes to the respective devices which are displayed as additional Nodes. Adding the device first may be an unnecessary step but I did it for both the EZSnsRF and the EZX10RF devices. Also all codes do not have to be added at once. Being new to the ISY device, I added one Dakota Alert Sensor code and tested that. Then went back and added another Sensor code and tested that, and so on.
-
Smarthome makes the IRLinc transmitter 2411T which takes Insteon messages and transmits IR signals in response. There are many IR protocols so you have to know what IR protocol the drapery opener is expecting and be sure the IRLinc transmitter sends that protocol. SimpleHomeNet also has an IR device. Their web site appears to be down so I cannot give you the item number for that device. The same IR protocol question exists with this device as well. Neither device will control the drapery opener if the IR protocols are not compatible.
-
ketchup318: Creating a new Scene with KPL button C as the Responder will work. I defined a new Scene and turned the Scene On then Off with two Programs which did turn the KPL button C LED On then Off. I did this on 2.7.15 before posting my previous response. I like to make sure something actually works before suggesting an approach. Good Luck. Post back it you have any difficulties.
-
If you want the Motion Sensor to turn On Keypadlinc button C include KPL button C as a Responder to the Scene where the Motion Sensor is the Controller and the garage lights are the Responder. What device are you using to physically control the actual garage lights. Linking the garage lights device as a Controller with KPL button C as a Responder does not automatically cause KPL button C to turn On when the Motion Sensor turns on the garage lights device. That scenario would require Controller A (Motion Sensor) turning On Responder B (garage lights) which would cause Responder B (garage lights) to turn into a Controller to then turn On KPL button C as a Responder. Insteon architecture does not work that way. There is one Controller with one or more Responders. The Responders DO NOT then become Controllers and turn On their Responders. All devices that should turn On in response to the Motion Sensor must be Responders to the Motion Sensor. EDIT: if in the end you want to control the KPL secondary button LED with a Program define a Scene with the KPL button C as a Responder and have the Program turn On or Off the Scene. A Program is issuing Insteon Direct commands when individual devices are selected. To turn On or Off a KPL secondary button LED you need to use a Group command and that requires the use of a Scene.
-
I have the SimpleHomeNet EZSwitch30 which switches 240V. It requires 120V to run the Insteon circuitry so a neutral is required. Sounds like you would have a neutral if the fan runs on other than 220. Smarthome just recently announced a 240V relay (even Dual Band) that does not require a neutral. A truly total 240V device. It is a new device so I doubt there is much experience with the device but SH has a good warranty.
-
When determining whether multiple circuit breakers are on the same 120V leg keep in mind that breaker panels are NOT laid out with leg A on the left side and leg B on the right side. Leg A and Leg B circuits alternate vertically, Leg A, Leg B, Leg A, Leg B, Leg A etc vertically. Also do not depend on circuit breakers at the same level but on different sides (left and right) to be on the same 120V leg. Panels often start with a different leg at the very top position. The top left side breaker will be leg A while the top right side breaker can be leg B. The electrician should be able to tell you which leg each breaker is on. Be sure the electrician has access to the Quick Start guides for the KPLs and InLineLincs. They are written for the DIYer so an electrician should have no problem determining the wiring requirements.
-
If they are all on the same 120V leg coupling is not required. There is nothing that can be done until the devices are wired correctly. Assuming the KPLs were not installed to physically control some other load (other lights) all the KPLs and all the InLineLincs must be wired to unswitched 120V neutral/line connections. They are basically electronic devices which require power at all times to function. All Insteon device control, that is, the KPLs controlling the InLineLinc are done with links (Scenes) between the devices established by the ISY device. This includes the KPLs LEDs being in sync with each other. KPLs are NOT 3-way switches despite having white/black/red wires which likely confused the electrician. Insteon devices in a Virtual 3/4 way configuration operate that way with links between the devices, not with traveler wires used by standard non-Insteon 3/4 way switches.
-
The electrician wired the KPLs as though there were physically controlling the power to the InLineLincs. The InLineLincs, as with all wired Insteon devices, require unswitched 120V AC. It is also likely that the KPLs are wired as those they are conventional 3-way switches, which they are not. You can verify that by checking the Red wires on the KPLs. They should not be connected to anything unless the KPLs are physically controlling some other load. If the KPLs and the InLineLincs are on the same 120V leg you do not need coupling for these devices to control each other. Turn the circuit breaker(s) Off supplying the KPL and the Inlinelincs. If there are two breakers and they are on the same leg than coupling is not required. The ISY PLM has the same requirement. It must be on the same 120V leg as the KPLs and the InLineLincs for coupling not to be required. The same technique of turning off the circuit breakers supplying the PLM, KPLs and InLineLincs and determining if they are all on the same 120V leg. It is likely that having invested in an ISY you plan on a much larger Insteon usage where coupling is required. It is true that some houses using Insteon run without coupling but they are so rare as to make the need for Access Points (or equivalent) an assumed requirement. Electric appliances such as electric hot water heaters and electric clothes dryers that operate on 240V AC can provide coupling on an intermittent basis. Things work for a time and then become unreliable. Plan on needing Access Point function. They do make a hardwired coupler that is attached near the power panel. This approach does not allow the use of RF based Insteon devices which themselves require an Access Point (or equivalent) so starting with Access Points is a more logical approach.
-
The lights are controlled by 6 individual InLineLincs so there is not the usual manual control by a paddle press without accessing the InLineLincs which are likely not in an easily accessed place. However, trying manual control is a good diagnostic approach if that is an option. If they manually turn On with the KPLs Off turn the KPLs On and see if that changes the symptom. How do you attribute the following incandescent light symptom to a coupling problem. 1. When the lights are turned on, they blink repeatedly (I'd say between 100% and 80% on levels)
-
Generally houses are supplied with 240V AC which is comprised of 2 120V Legs which I will call leg A and leg B for this discussion. If the ISY PLM is plugged into 120V leg A and the KPLs and InlineLincs are connected to 120V leg B, the Insteon signals between the PLM and the KPL and InlineLincs will likely be unreliable. The Insteon signals have to travel out to the power company transformer on one leg, through the transformer back on the other leg. This is an unreliable path. A pair of Access Points are plugged into leg A and leg B such that the RF capability of the Access Points move the Insteon signals (couple) between the two 120V legs. Independent of the solution to the flashing lights, most Insteon installations require the two 120V legs to be coupled together. However, that would not explain the pulsing incandescent lights. I assume at this point that the devices (KPL and InLineLincs) are not being supplied from an unswitched 120V AC source that all wired Insteon devices require. Unless the electrician was familiar with Insteon devices in a Virtual 3-way circuit it is likely that either or both KPLs are not wired correctly for a Virtual 3-way circuit with the additional possibility that the InLineLincs controlling the lights are being supplied from the KPL Load connection rather than unswitched 120V AC. Without actually checking the wiring and measuring the 120V supply to each device I cannot be absolutely sure but that is where I would start looking. Do you have the capability to measure the AC voltage going to each KPL and InLineLinc? If the KPLs are not physically controlling some other load a simple check would be to look at the Red wires on each KPL. They should not be connected to anything unless the KPLs are also physically controlling some other load not mentioned in your previous post.
-
Sounds like the devices are not wired correctly. Was the original configuration a 3-way circuit controlling the 6 lights? All the InLineLincs must be powered by unswitched 120V AC connected to the White (neutral) and Black (line) InLineLinc wires. The Red Load wire goes to the respective fixture. The KPLs must be powered by unswitched 120V AC with the same White (neutral) Black (line) connections. If the KPLs replaced standard 3-way switches the KPL Red load wire is capped (not connected to anything). You did not mention Access Points. Do you have two RF based devices such as Access Points for Dual Band LampLincs etc coupling the two 120V legs.
-
The Smartlabs specification for Thermostat commands Get/Set Setpoint values is x 2. 0x00 ⇒ 0xFF Temperature Setpoint x 2 (unsigned byte) EDIT: to determine if the adaptor is returning an incorrect value, run the Event Log at Level 3 so the SetPoint values returned by the adaptor can be viewed.
-
A RemoteLinc (and other Insteon RF devices) send 2 Group Broadcast messages for a single button press. Not sure if that is contributing to the difficulty as the messages from the first button press have not completed before the second button press messages start. Thu 06/24/2010 05:56:41 AM : [iNST-SRX ] 02 50 11.C8.44 00.00.03 C7 11 00 LTONRR (00) 1st press 1st Group Broadcast Thu 06/24/2010 05:56:41 AM : [ 11 C8 44 3] DON 0 Thu 06/24/2010 05:56:41 AM : [iNST-SRX ] 02 50 11.C8.44 00.00.03 C7 11 00 LTONRR (00) 1st press 2nd Group Broadcast Thu 06/24/2010 05:56:41 AM : [iNST-SRX ] 02 50 11.C8.44 00.00.03 C7 11 00 LTONRR (00): Process Message: failed 2nd press 1st Group Broadcast Thu 06/24/2010 05:56:41 AM : [iNST-SRX ] 02 50 11.C8.44 12.9F.46 41 11 03 LTONRR (03) 1st press Group Cleanup Direct Thu 06/24/2010 05:56:42 AM : [ Time] 05:56:44 2(0) Thu 06/24/2010 05:56:42 AM : [ Time] 05:56:44 2(0) Thu 06/24/2010 05:56:42 AM : [iNST-SRX ] 02 50 11.C8.44 00.00.03 C7 11 00 LTONRR (00) 2nd press 2nd Group Broadcast Thu 06/24/2010 05:56:42 AM : [iNST-ACK ] 02 62 0A.9D.32 0F 11 BF 06 LTONRR (BF) other Insteon traffic to device 0A.9D.32 to turn On to Bright Level 0xBF (not full bright) Thu 06/24/2010 05:56:42 AM : [iNST-ACK ] 02 62 0A.9D.32 0F 11 BF 06 LTONRR (BF): Process ACK: duplicate ignored Thu 06/24/2010 05:56:42 AM : [ 11 C8 44 3] DON 0 Thu 06/24/2010 05:56:42 AM : [iNST-SRX ] 02 50 0A.9D.32 12.9F.46 2B 11 BF LTONRR (BF) Thu 06/24/2010 05:56:43 AM : [ Time] 05:56:45 2(0) Thu 06/24/2010 05:56:43 AM : [iNST-SRX ] 02 50 11.C8.44 12.9F.46 42 11 03 LTONRR (03) 2nd press Group Cleanup Direct Thu 06/24/2010 05:56:43 AM : [iNST-ACK ] 02 62 0A.9D.32 0F 11 BF 06 LTONRR (BF) other Insteon traffic to device 0A.9D.32 to turn On to Bright Level 0xBF (not full bright) Thu 06/24/2010 05:56:43 AM : [iNST-ACK ] 02 62 0A.9D.32 0F 11 BF 06 LTONRR (BF): Process ACK: duplicate ignored There is other Insteon traffic in the Event Log. Thu 06/24/2010 05:56:42 AM : [iNST-ACK ] 02 62 0A.9D.32 0F 11 BF 06 LTONRR (BF) is turning on device 0A.9D.32 On to a bright level of 0xBF (not full bright). First thing is to get rid of the device 0A.9D.32 traffic to keep traffic simple. Second would be to wait a few seconds between the first and second button press on the RemoteLinc to allow the first button press traffic to complete before starting the 2nd button press traffic