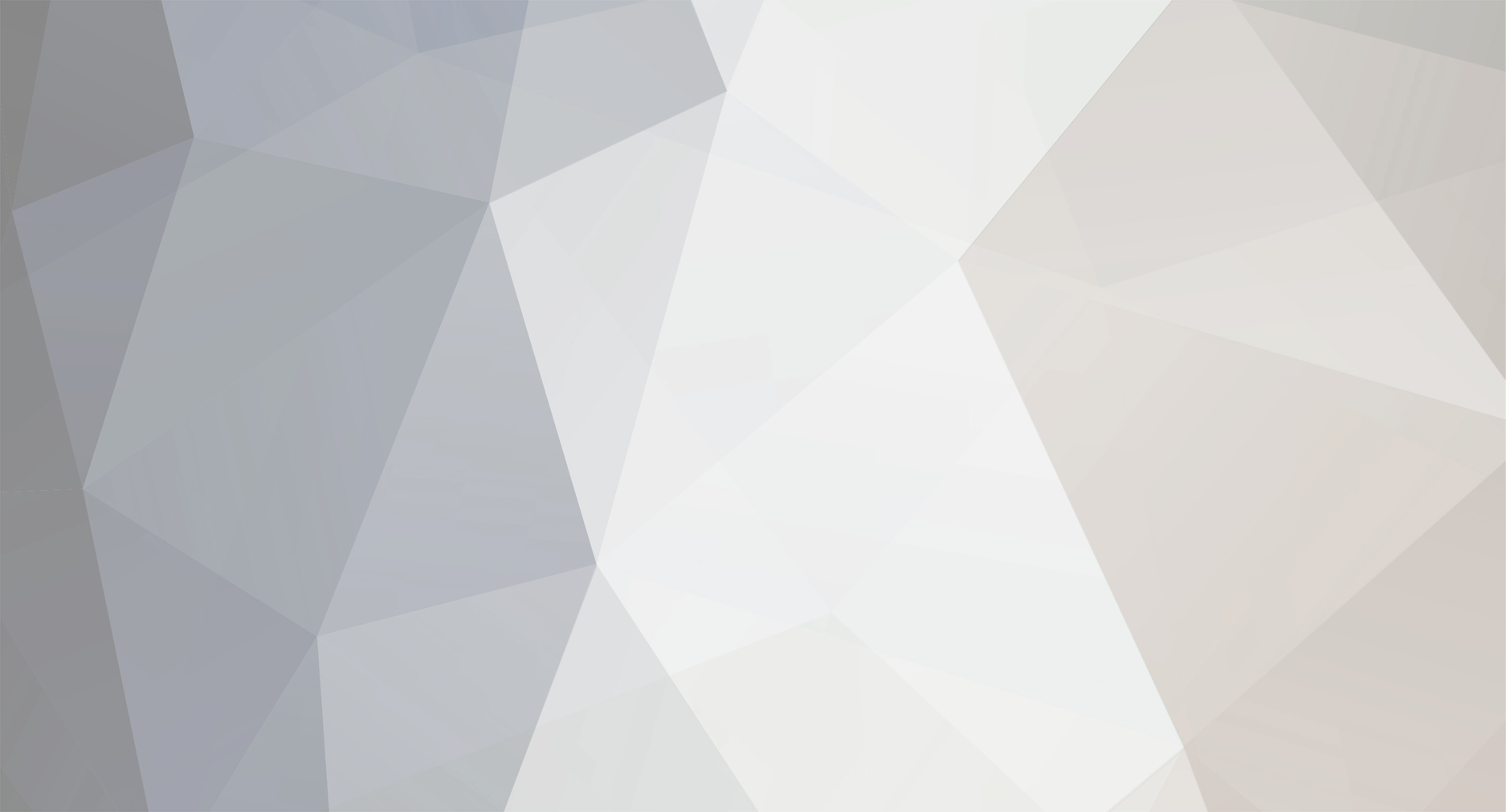
LeeG
Members-
Posts
12943 -
Joined
-
Last visited
Everything posted by LeeG
-
bocarob, What EZIOxx device are you using for hot water heater control. How did you control the EZIOxx, a Program using Insteon Direct commands or was it with a Scene. Do you have any Event Log at level 3 of the activity. There is a known problem at 2.8.1 where manual control through the Admin Console does not reflect the status of an Output node even though the node actually did turn On. A Query of the EZIOxx node corrects the Admin Console display. This should be resolved in 2.8.2. I'd be happy to work with you on the problem if you want to look into it. Or perhaps provide enough detail for me to recreate it here. Lee
-
I have relatively limited experience with ISY but have always entered the password twice. The first is the OS prompt when the Java app is invoked and again from the Admin Console code. Just assumed this was normal. Happens on 2.7.15, 2.8.0 and 2.8.1.
-
Are these 120V units or 240V units. Smarthome carries a 240V NC Load Controller that does sense the On/Off state of the load and sends that state information back to a responder. However, that raises a question. An AC unit that is switched Off will look the same as a unit which is Off due to reaching its temperature setting. How do you want to handle this.
-
You can poll that often but you really do not want to. Even at a 2 minute interval that is 6 outbound, 6 inbound Insteon messages to cover the 6 devices controlling AC units. That would be 360 Insteon messages per hour, every hour day and night. It is okay to poll perhaps every hour to catch up in case something was missed but not for normal minute to minute operation. There are better solutions. Just have to have time to work them out. With all the Insteon device experience on this forum and other Insteon forums such as the one at Smarthome someone will have a solution that does not revolve around the need to poll devices.
-
No. If the KPL button is Off (LED is Off) when you press the button it sends an ON command to all the responders. If the responder was Off it will turn on. If the responder was already On it will stay On. The other part will take some research.
-
Regardless of why the GUI is presenting the buttons, Secondary KPL buttons cannot be controlled directly. This is KPL hardware, not an ISY restriction. The KPL button feature of mutually exclusive buttons applies only to pressing the buttons on the KPL. The KPL hardware does not apply that button relationship to commands from another controller. To achieve the equivalent button behavior requires establishing various Scenes that allow all buttons in the group or some subset of those buttons to be turned Off under Scene control and the active button to be turned On by Scene control. EDIT: also note that the trick of issuing an ON command for a Scene and have some of the responders set to 0% Bright which turns those responders Off, does not work for KPL Secondary buttons. To turn a Secondary KPL button Off from another controller requires sending an Off for the Scene for which the KPL Secondary button is a responder.
-
I assume the question is in the context of the EZFlora Irrigation controller. The EZFlora hardware does not have that type of logic. When zones are activated is controlled by whatever automation software/firmware is controlling it.
-
Putting an Access Point on the end of the house reduces the effective coverage as there is nothing on one side of the Access Point. Better to put them in more central locations. Of course if there are dead spots in RF coverage putting an Access Point near the dead spot should eliminate the dead spot. Don't worry about signal collisions. Also when RF reception is good you will see the Motion Sensor sends two Group Broadcast commands. This is not the result of multiple Access Points (or equivalent) receiving a single command from the Motion Sensor.
-
You can right click on the EZIO4O node and Query which will correct the admin display.
-
This is a problem with the admin console display, the correct relay is being controlled. Also if the output relay is controlled through a Scene the correct relay state is indicated.
-
If you want to turn KPL button D Off from the ISY define a Scene with KPL button D as a Responder. Turning this Scene Off will turn the KPL button Off.
-
Joe, The trace is showing the commands expected when the sensor changes state. First a Group On command sequence is sent from the IOLinc followed by a Group Off command sequence. There is nothing in the trace that indicates you initiated a Scene to send a Group On or Group Off from the ISY to the IOLinc relay. Lee EDIT: did not mean to imply a Scene was the only way. There is nothing in the trace that any attempt was made from the ISY to control the IOLinc relay.
-
The Event Log does not look like it was set for level 3 but since it says success that may not be needed. Are you using the Link Management | Add Button to IRLinc Transmitter to add additional nodes.
-
garybixler Whether I2 works depends on how new the device is. Many of the internal PLMs indicate an I2 engine but do not support the ALDB command. How did you add the EZIO4O, Auto Discovery or explicit Device Type. If you are on a PC and have a PLM connected to the PC you can use the SHN Utility to configure all the EZIOxx options. Lee
-
The Scene where button D is the controller and the AppliaanceLinc is the responder will result in the ApplianceLinc turning On immediately because of the Scene definition. Delete the Scene with button D as the Controller. Define a Program that triggers from button D On and turn the ApplianceLinc On directly after the desired wait, without the use of a Scene.
-
I make the following assumptions. You want any of the four devices to be able to turn On/Off the load and all status LEDs on the ToggleLincs and KPL button LEDs should stay in sync. If this is correct define one ISY Scene with all four devices as Controllers. The ISY will write all the necessary links to cross link the four devices so that any device can control the load and all the LEDs will turn On/Off together. If that was not the right assumption about the relationship between the devices expand on that aspect which will likely change the number of ISY Scenes.
-
Yes and no. When you manually link the process creates a link record in the controller and the responder devices. Of course you can add additional responders one at a time but each manual operation is still writing a link record in the controller and a responder device. The same thing is done under the ISY. However, more complex relationships can be established such as cross linking devices simply by defining both devices as controllers. The ISY automatically writes the controller to responder device links between the two devices. You can do the same thing with manual linking, just much easier to define through the ISY. Also the ISY automatically adds the ISY PLM to the Scene so that it can be controlled from the ISY. There are only two types of active link records. A "Controller of" link record in the controller device and a "Responder to" link record in the responder device. Same type of link records are written whether done manually or through the ISY. Same number of link records whether done manually or through the ISY assuming you manually establish the same relationships the ISY does automatically.
-
A Dual Band PLM could improve communication by sending PLM commands out on RF to your other RF coupling devices (Access Points, or other Dual Band device). If the problem causing intermittent communication problems is something generating noise intermittently a Dual Band PLM has less chance of improving the situation. Bottom line is there is no way to tell for sure without actually doing it. Moving to a later PLM revision is generally a good idea. EDIT: if you do go with a Dual Band PLM you will also need an external power supply to power the ISY as Dual Band PLMs do not provide 12V power as the old PLMs do.
-
The -5011 error is "PROCESS DEVICE STATE CHANGE SID NOT FOUND ". The ISY is not recognizing the device type during Auto Discovery if listed as Unsupported Device (I assume you added the devices using Auto Discover). Are they 220V SwitchLincs or 240V Dual Band Load Controllers? Either way I would Remove the devices and add them back selecting the appropriate Device Type from the pulldown.
-
From the picture it appears you have a Common wire but you are asking can you install the Venstar without a Common. I'm pretty sure the Venstar requires 5 wires. If you have 5 wires then you should be okay. If not Smarhome has an Add A Wire kit that I think converts a 4 wire run to a 5 wire run. There is a good guy on the Smarthome forum that knows all about HVAC and Venstar. You should post the question on the Smarthome forum under "Thermostats and HVAC Control".
-
You did not indicate whether the problem is with the Program Then not being invoked or the Scene not working.
-
If the Motion Sensor is linked to the Garage Light switch the Motion Sensor will send an Off command to the Garage Light switch. No way to override that direct link unless you set the Motion Sensor to On commands only mode. You can remove that direct link and run an ISY Program that triggers from a Motion Sensor On command. Then have the logic in ISY Programs decide whether the last On command to the Garage Light switch came from the Motion Sensor On command triggered Program in which case it turns Off the switch after some delay value. If the last On command comes from the Garage Light switch (manual On) then a different delay value is used. There is some technique that uses the true/false state of another Program to act as a logical indicator whether the last On condition came from the Motion Sensor or from a manual On from the Garage Light switch itself. Unfortunately I cannot tell you how to code the technique of using another Program true/false state as a logical switch but there are multiple references to the technique in various forum topics.
-
Upgraded PLM to new dual band - now having ISY problems
LeeG replied to theedudenator's topic in ISY994
Individual device control is done with Insteon Direct commands which do not require link records. Are the Programs that do not function controlling Scenes? If so it sounds like the new PLM did not get the link records restored or the devices that are part of the Scene did not get updated with the new PLM Insteon address. Either condition will prevent Scenes from functioning. If the Program is controlling an individual device rather than a Scene there should be no difference between running the Program and the commands issued through My Lighting. The Event Viewer at Change Level 3 will show what commands are being issued by the Program and what if any device response is received. -
There is no independent control over a KPL button LED separate from the control of the button itself. When a KPL button is logically turned On the underlying LED turns On. When a KPL button is On, the next physical button press causes the KPL to send a Group Off to any device linked as a Responder to the button and of course the button LED turns Off. When a button is logically turned Off the underlying LED turns Off. The next physical button press causes the KPL to send a Group On to any device linked as a Responder to the button and of course the LED turns On. This is assuming the KPL button is in the default toggle mode. The KPL local load control button (ON/OFF in 6 button mode, Main in 8 button mode) can be turned On/Off with an Insteon Direct On/Off command or by turning a Scene On/Off where the KPL load control button is a Responder to the Scene. A KPL Secondary button can only be turned On/Off by turning a Scene On/Off where the KPL Secondary button is a Responder to the Scene. Regardless of how a KPL button is turned On or Off (physical button press, Insteon Direct command, Insteon Group/Scene command) when the button is Off the underlying LED is Off, when the button is On the underlying LED is On. Some folks refer to a button being turned On/Off by talking about turning the LED On/Off. Some folks talk about turning a button On/Off. A difference without distinction. When a button is On the LED is On. When an LED is On the button is On.
-
I am on 2.7.15, I added all my devices using New INSTEON Device and specified both the Insteon address and selected the device type from the pulldown. I do not have a + along side the primary button entry in My Devices tree. All eight buttons are listed as I posted before.